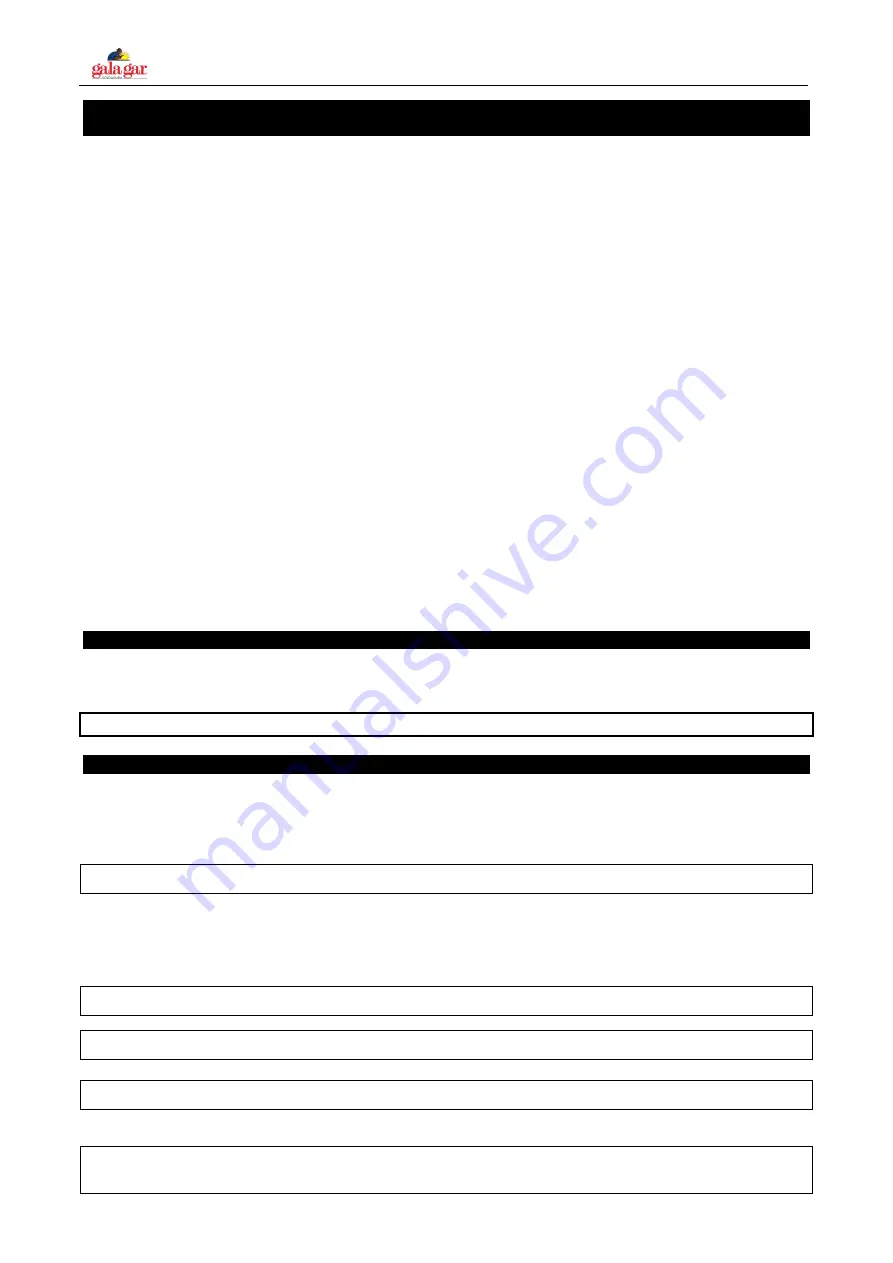
D-20C / D-20C (V-I)
13
3.1. RECOMMENDATIONS FOR THE USE OF THE EQUIPMENT AND WELDING OPERATION.
MATERIALS AND GASES.
The adjustment of the welding parameters in the MIG-MAG equipment is a much more sensitive job than
in traditional welding equipment. The adjustment depends mainly on:
- Welding voltage. It can be carried out from the wire-feed unit if the power source is electronic.
- Wire speed.
- Type of gas used.
- Thickness and material of the part to be welded.
- Arc length, torch position and type of seam.
The welding intensity depends on the wire speed. If the wire speed increases, the welding current value will
increase resulting in a shorter arc.
If maximum penetration is desired, the minimum voltage possible must be used. Although it must be taken
into account that as the voltage drops the seam aspect worsens.
The correct adjustment of the welding parameters results in a smooth and quiet operation, with a typical
sound during operation.
If the wire speed is high, the wire tends to trip up and the arc becomes unstable. If the speed is low there
may be many projections or the wire can get burnt.
If the reactance value chosen is low (respect to that needed) the number of projections is high; if the
reactance is very high the wire tends to get wound up. The greater the wire diameter, we must consider a high
reactance.
The direction of the torch movement and the position of the torch affect the quality of the welded seam.
You can consult a series of recommendations depending on the material to be welded in section 3.5 of the
power source instructions manual.
CHAPTER 4. MAINTENANCE OPERATIONS. RECOMMENDATIONS.
In order for the equipment to have a long life we must follow some essential rules for maintenance and
use. Abide by these recommendations.
CORRECT MAINTENANCE OF THE EQUIPMENT WILL AVOID A GREAT PERCENTAGE OF FAULTS.
4.1 MACHINE MAINTENANCE. GENERAL RECOMMENDATIONS.
Before carrying out any maintenance operation on the wire-feed unit, it is advisable to have disconnected it
from the power source.
Specialized personnel must handle the machine to carry out maintenance and repair operations.
)
BLOW THE INSIDE OF THE MACHINE WITH COMPRESSED AIR FROM TIME TO TIME.
The accumulation of metal dust on the inside is one of the main causes of breakdowns in this type of
equipment as they are subject to a great amount of pollution. As an essential measure, the equipment must be
kept separate from the welding place, not placing it a short distance away. Avoid the accumulation of metal
powder at the base of the driving motor.
)
PLACE THE EQUIPMENT SOMEWHERE WHERE CLEAN AIR IS RENEWED.
)
KEEP THE MACHINE PANELS CLOSED.
)
KEEP THE WELDING GUN IN GOOD CONDITIONS FOR USE.
A damaged or worn gun can cause inefficient welding.
)
WHEN FINISHING THE WELDING OPERATION MAKE SURE THAT THE TORCH CATCH IS
UNLOCKED. (If mechanical lock guns are used)