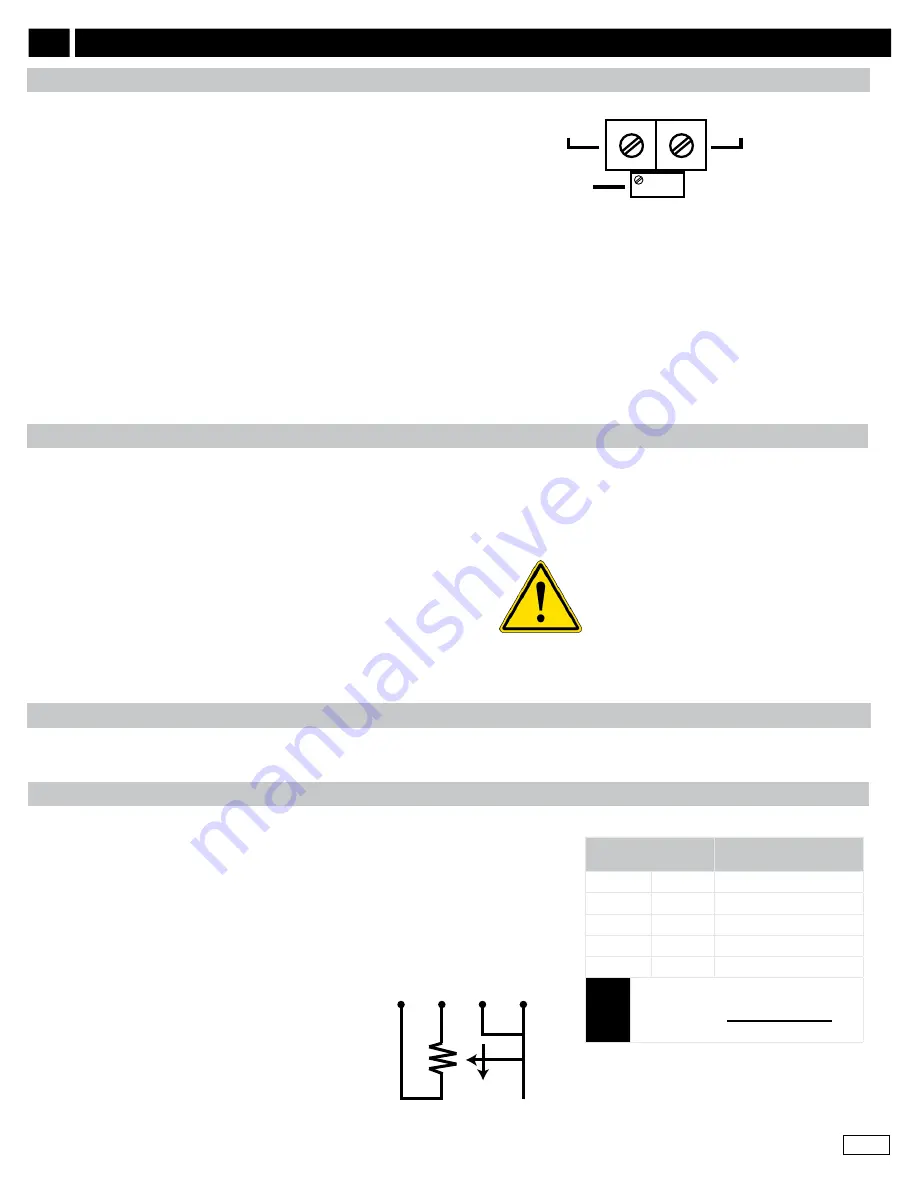
6
Governors America Corp. © 2021 Copyright All Rights Reserved
ESD5500-II Fusion Series Speed Control Unit 1-2020-A4 PIB2180
12
ADDITIONAL FEATURES & OPTIONAL WIRING
Droop
Idle
Speed
SPeeD ranGe
PoTenTIomeTer
vaLUe
900 Hz
540 RPM
1 K
2400 Hz
1440 RPM
5 K
3000 Hz
1800 RPM
10 K
3500 Hz
2100 RPM
25 K
3700 Hz
2220 RPM
50 K
noTe
RPM values shown are for 100 teeth flywheel
MPU Signal (Hz) = RPM x Flywheel Teeth
TaBLe 1
60 s
G
J
K
L
CW
*
* Select proper potentiometer
value from Table 1
POTENTIOMETER WIRING
Droop is based on a speed sensor frequency of 4000 Hz. and an actuator current change of 1 amp from no load to full load. Applications with
higher speed sensor signals will experience less percentage of droop. Applications with more actuator currant change will experience higher
percentages of droop.
Though a wide range of droop is available with internal control, droop level requirements of 10% are unusual. If droop levels experienced are
higher or lower than those required, contact GAC for assistance.
1. Terminal N is sensitive. Accessory connections must be shielded.
2. When an accessory is connected to Terminal N, speed will de-
crease and speed adjustment must be reset.
3. When operating in the upper end of the control unit frequency
range, a jumper wire or frequency trim control may be required
between Terminals G and J. This increases the frequency range of
the speed control to over 7000 Hz (4200 RPM).
4. If the auto synchronizer is used alone, not in conjunction with a load
sharing module, a 3 ohm resistor should be connected between Termi-
nals N and P. This is required to match the voltage levels between the
speed control unit and the synchronizer.
A short circuit on Terminal N can damage the
speed control unit.
Never jumper Terminal P directly to Terminal N.
Droop is typically used for paralleling engine-driven generators. When in droop
operation, the engine speed will decrease as engine load increases. The per-
centage of droop is based on the actuator current change from no engine load
to full load. Factory setting for Droop is 0%.
To set droop:
1. Place the optional external selector switch in the Droop position. Droop is
increased by clockwise rotation of the Droop adjustment control.
2. After the droop level has been adjusted, the rated engine speed setting may
need to be reset. Check the engines speed and adjust that speed setting
accordingly.
The AUX Terminal N accepts input signals from load sharing units, auto synchronizers, and other governor system accessories, GAC acces-
sories are directly connected to this terminal.
The following apply when using the accessory input:
The +10 volt regulated supply, Terminal P, can be utilized to provide power to GAC governor system accessories. Up to 20 mA of current
can be drawn from this supply. Ground reference is Terminal G.
SPeeD DrooP oPeraTIon
acceSSorY InPUT
acceSSorY SUPPLY
A single remote speed adjustment potentiometer can be used to adjust
the engine speed continuously over a specific speed range. Select the
desired speed range and corresponding potentiometer value. (TABLE 1)
If the exact range cannot be found, select the next higher range potenti-
ometer.
Place an additional fixed resistor across the potentiometer to obtain the
exact desired range. Connect the speed range potentiometer using
Terminals G and J.
To maintain engine stability at the minimum speed set-
ting, a small amount of droop can be added using the
DROOP adjustment. At the maximum speed setting
the governor performance will be near isochronous,
regardless of the droop adjustment setting.
WIDe ranGe remoTe varIaBLe SPeeD oPeraTIon