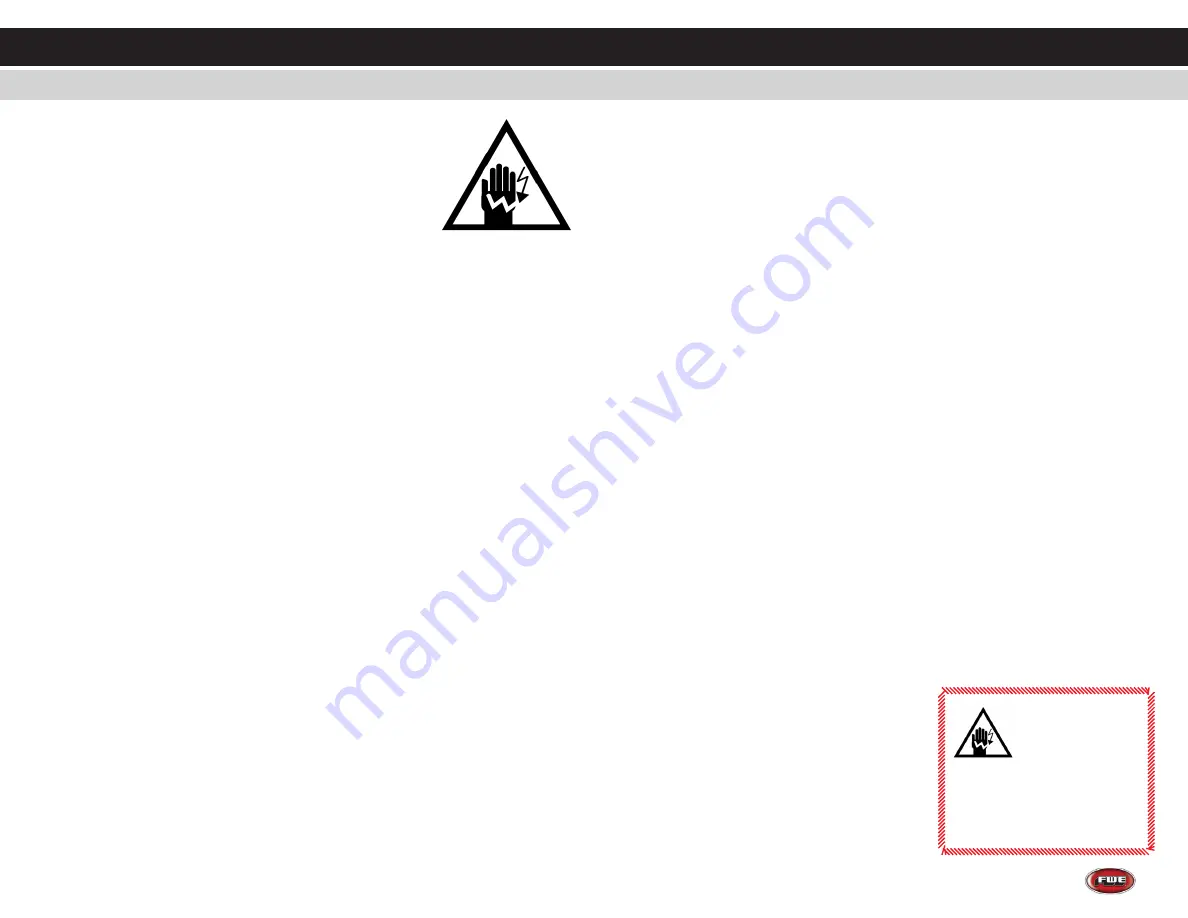
TROUBLESHOOTING GUIDE
19
FWE
REFRIGERATED "AIRSCREEN" SERIES
18
FWE Operating Instructions | Refrigerated "AirScreen" Series
TROUBLESHOOTING GUIDE
FWE
REFRIGERATED "AIRSCREEN" SERIES
TROUBLESHOOTING GUIDE
(CONTINUED)
6. Condensing unit operates for prolonged periods or continuously:
A. Evaporator coil iced – Defrost.
B. Prolonged or too frequent door openings – Train staff on proper use.
C. Excessive heat load placed in the cabinet. Allow sufficient time for removal of heat.
D. Dirty condenser coil- clean
E. Controls relay failure. Technician required.
F. Low refrigerant or other refrigeration system issue. Technician required.
7. Noisy condensing unit:
A. Loose parts or mounting. Technician required.
B. Tubing rattles - Find and increase tube clearance. Technician required.
C. Bent fan blade causing vibration – replace blade. Technician required.
D. Noisy motor - May require replacement. Technician required.
8. Unit evaporator coil excessive icing:
A. Operating in a highly humid environment. Additional manual defrosting may be
required.
B. Door gasket not sealing properly. Adjust or replace gasket.
C. Door requires adjustment. Technician required.
D. Room ventilation or fans blowing air into the unit. Move unit, block air baffles or move
fans.
9. Vapor pan overfilling (water on the floor under the unit):
A. Door being kept open to long allowing excessive ice buildup on evaporator coil.
Review operating parameters.
B. High room humidity causing excessive ice buildup on evaporator coil. Review
operating parameters.
C. Vapor pan drain plug out. Put plug back in place.
D. Attach hose to drain pan and run into a floor drain.
10. Control Error Messages:
“Err1”
Sensor Failure
“Err2
Configuration Connector Error
“Err3”
Not Defined
“Err4”
Under Temperature
“Err 5”
Over Temperature
“Err6”
Key Shorted
“Err7”
Door Switch
“Err8”
EPROM Possible corruption
TROUBLESHOOTING GUIDE
1. AirScreen does not turn on (control display does not light up):
A. Check that unit is plugged in.
B. Check circuit breakers and fuses.
C. Check for damaged cord. Technician required.
D. Control issue or other internal issue. Technician required.
2. Closed door cabinet temperature too high (unit running):
A. Control Setting is too high – Set a lower temperature on the control.
B. Product temperature very warm. Give the unit time to pull product down to
temperature.
C. Unit may be in a defrost cycle. Wait for the defrost cycle to finish.
D. Dirty or clogged condenser coil. Clean condenser coil.
E. Iced up evaporator coil. Unit may require additional manual defrosting.
F. Refrigerant system issue. Technician required.
3. Open door cabinet temperature to high (unit running):
A. Control Setting is too high – Set a lower temperature on the control.
B. Product load was not properly pre-chilled.
C. Door left open to long.
D. Inadequate Air Circulation – Rearrange the product load to improve air circulation.
E. Room ventilation or fans blowing air into the unit. Block air baffles or move fans.
F. All 10 shelves should have trays on them. Keep empty trays in the unit.
G. Unit may be in a defrost cycle. Wait for the defrost cycle to finish.
H. Dirty or clogged condenser coil. Clean condenser coil.
I. Iced up evaporator coil. Unit may require additional manual defrosting.
J. Review operation, installation and performance guidelines.
K. Refrigerant system issue. Technician required.
4. Closed door cabinet temperature to low:
A. Control setting to low – set a higher temperature on control.
B. Compressor running continuously (not cycling) and open displayed on control
indicates a bad or out of adjustment door switch. Technician required.
C. Compressor relay stuck closed. Technician required.
5. Condensing unit fails to start- hums but trips on overload protector:
A. Turn unit off and wait 30 minutes before turning back on to see if unit resets itself.
B. Low voltage should be checked by an electrician and corrected.
C. Compressor motor Start capacitor failure. Technician required.
D. Condenser relay not closing or defective. Technician required.
E. Compressor motor winding open or shorted. Technician required
F. Internal mechanical trouble with compressor. Technician required.
SHOCK HAZARD
NOTICE
WARNING:
RISK OF ELECTRICAL
SHOCK. DISCONNECT ELECTRICAL
POWER SUPPLY BEFORE CLEANING
ANY PARTS OF THE UNIT OR PRIOR
TO ANY SERVICE.
SHOCK HAZARD
NOTICE