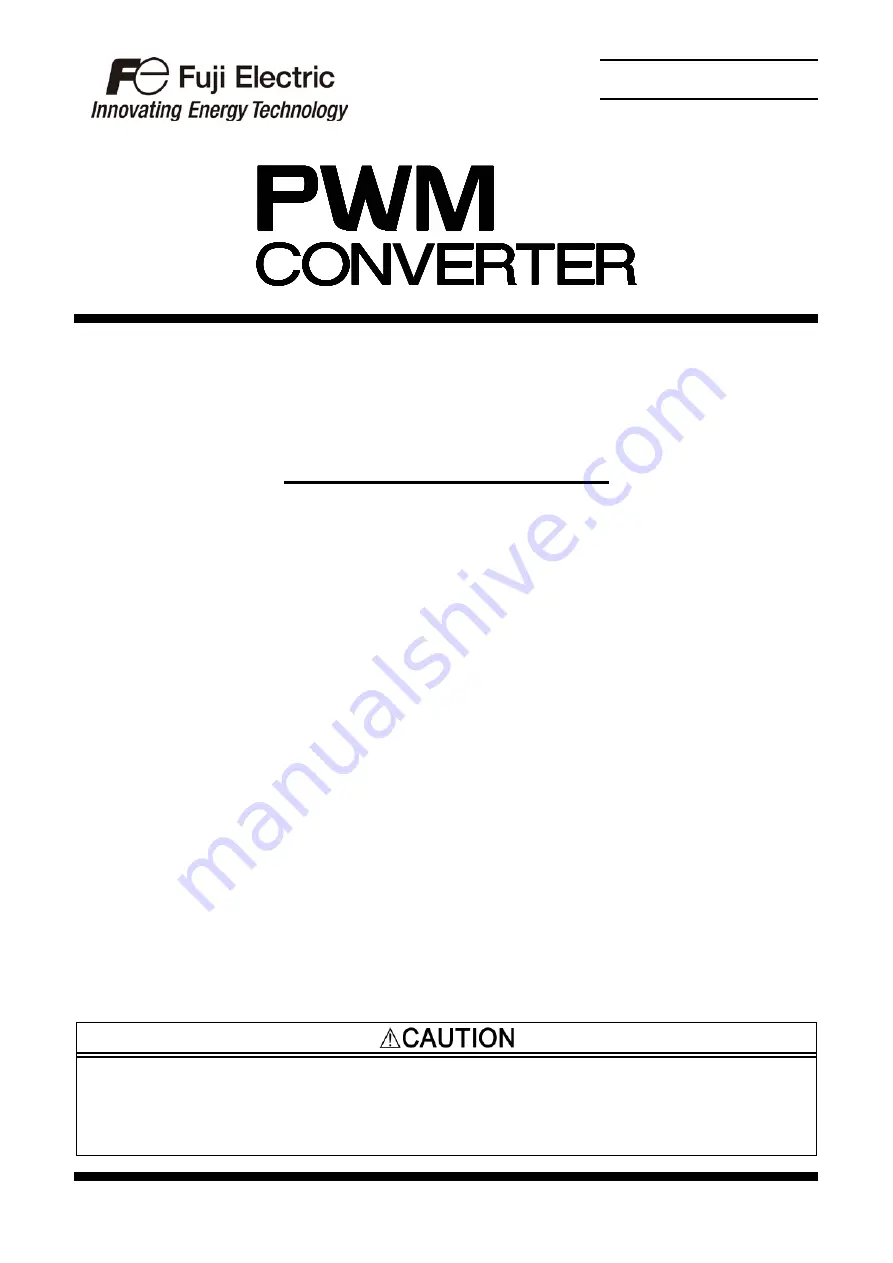
Instruction Manual
High Power Factor PWM Converter
with Power Regenerative Function (Stack Type)
RHC-D 690V Series
RHC132S-69DE to RHC450S-69DE
• Read through this instruction manual to become familiar with the handling procedure of this product, and proceed to
installation, connection (wiring), operation, and maintenance inspection.
• Deliver this manual to the end user of this product. Keep this manual in a safe place until this product is discarded.
• The product is subject to change without prior notice.
Fuji Electric Co., Ltd.
INR-SI47-1944-E