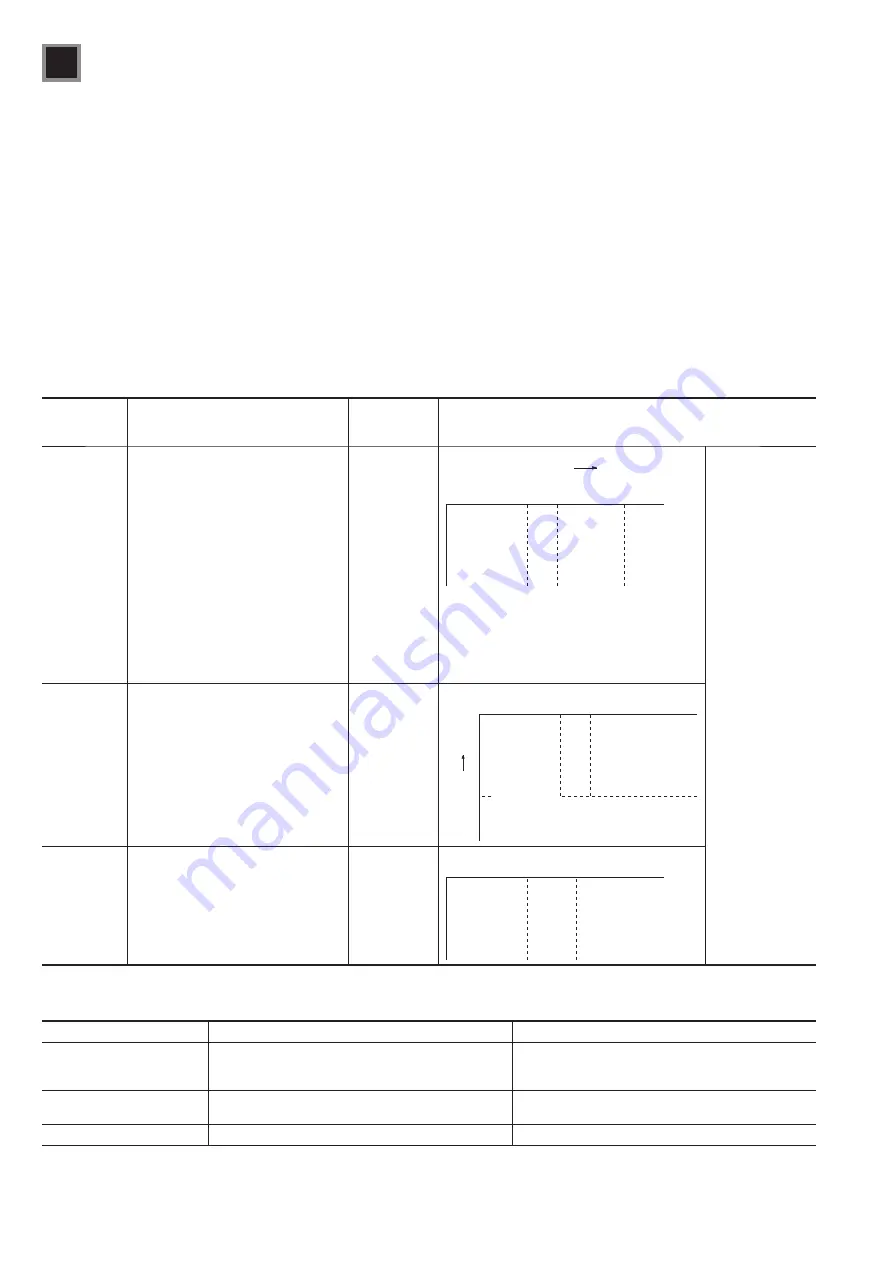
92
4
Environment and usage precautions
4-2 Application to special environments
Table 4-4 Corrosive gas effects and protective measures
Gas type
Effect on metal
Effect on
insulation
materials
MCCB application
Hydrogen
sulfide gas
(H
2
S)
(1) Copper and copper alloy:
A sulfide film develops that forms a
high-resistance layer. Components
that make actual physical contact
as well as components that operate
with high levels of mechanical
stress, such as terminals, require
anti-corrosion measures like surface
treatment using Sn plating or clear
coating with lacquer.
(2) Silver and silver alloy:
Although a sulfide film develops, it is
not a problem here because the film
peels off the contact with arcing or
sliding action during switching.
(3) No problems have been found with
other metals.
No problems
0
to
0.02 to 0.07
to
to
0.3
Gas density (ppm)
Standard parts
Parts
treated for
anti-
corrosion
and (B) or
(C)
Parts
treated for
anti-
corrosion
and (D)
*
1
*
2
Note:
*1
Use parts treated
for anti-corrosion.
*2
Protective
measures for
equipment and
control panels
(A) Lower the
humidity with
equipment like
a space heater
to prevent
condensation.
(B) Use an
activated
charcoal filter
to improve the
environment.
(C) Install the
packing
provided for
the doors and
seal the control
panel floor as
well as cable
ports.
(D) Use an air
purging system.
Sulfurous acid
gas (SO
2
)
Nitrous acid
gas (NO
2
)
High temperature and high humidity
conditions that are particularly prone to
condensation will accelerate corrosion.
There is less chance of corrosion with
humidity at 65% or lower.
No problems
0
to
0.04 to 0.5
to
100
%RH
65
Standard parts
Parts treated for
anti-corrosion
and (A+C) or (B)
*
1
*
2
Chlorine gas
(CI
2
)
Chlorine gas is far more corrosive than
nitrous acid gas or sulfurous acid gas.
Because it corrodes just about any
metal, protective measures are critical
for equipment and control panels.
Moisture
absorbed
by premixed
polyester
lowers its
insulation
resistance.
0
to
0.02
to 0.1
to
Standard parts
Parts treated
for anti-
corrosion and
(D)
*
1
*
2
Table 4-5 Special environment problems and protective measures
Environment
Potential problems
Protective measures
Water vapor, water drops and
oil vapor
s-ETALCORROSION
s-OISTUREABSORBEDBYINSULATIONMATERIAL
s,OWERINSULATIONRESISTANCE
s0LACEINAWATERPROOFCASING)0
s#ONDUCTPERIODICMAINTENANCEINSPECTIONS
Dust
s#ONTACTFAILURE
s0OORINSULATION
s0LACEINADUSTPROOFCASING)08
Flammable gas
s%XPLOSIVECOMBUSTION
s$ONOTUSEINTHISENVIRONMENT
4-2-4 Application to special atmospheres
(1) Corrosive gas and salt
The contacts of MCCBs are generally made of silver or silver
alloy that readily forms a sulfide film on contact with sulfurized
gas. Although this may degrade the quality of the contacts, the
film peels off easily so the problem is not significant, especially
with frequent switching. Intentional switching may be required
periodically when ordinary switching occurs infrequently. An
MCCB designed for special atmospheres should be used in
areas with high concentrations of sulfurized gas.
(2) Others
Table 4-5 shows special atmosphere problems and protective
measures.