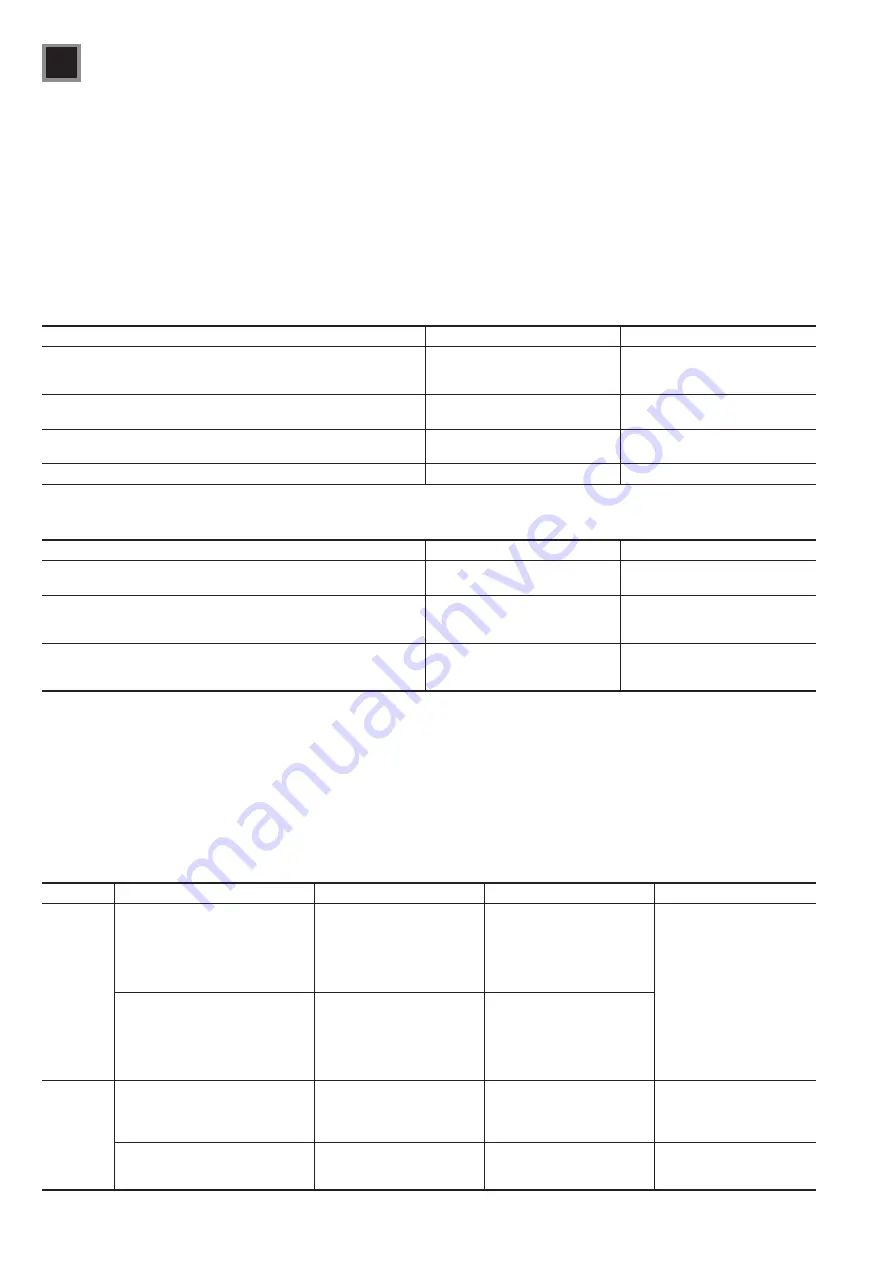
98
5
Maintenance inspections
5-2 Periodic inspections
Table 5-4 Inspection standards
Conditions
Environment
Examples
Inspection interval
Remarks
Normal
operating
conditions
A location with a constant supply of
clean and dry air
A dustproof, air-conditioned
electrical equipment room
Once every two or three
years Once a year for MCCBs
installed more than ten years
Once every six months for
MCCBs installed more than
15 years
Use standard specification
MCCBs.
Set inspection intervals
according to actual
circumstances.
An indoor location with minimal dust
and no corrosive gases
Installed in a control panel in a
separate electrical equipment
room with no dustproofing or
air conditioning, or inside an
enclosure.
Once a year
Once every six months for
MCCBs installed more than
10 years
Once a month for MCCBs
installed more than 15 years
Poor
environment
A location with minimal dust con-
taining nitrous acid gas, hydrogen
sulfide gas, salt or high-temperature
gases
Geothermal power generation
equipment and sewage plants
as well as paper, steel, and
pulp plants
Once every six months Once a
month for MCCBs installed for
more than 5 years
Requires appropriate action.
(See 4-2-4, Chapter 4.)
A location where people could not
stay for long periods, or a location
with excessive dust or corrosive gas
Chemical factories, quarries,
or mines
Once a month
Requires enclosing or other
appropriate action.
5-2-2 Periodic inspections
No time-related durability performance criteria are determined
for MCCBs. Durability performance can vary significantly
with the operating environment, operating load, switching
frequency, and the quality of periodic inspections and repairs.
Proper operating conditions must be maintained at all
times in order to ensure MCCB performance and to prevent
unexpected failure. However, performance may decline for a
number of reasons, including dust accumulation, loose screws,
wear on mechanical parts due to excessive switching, or
contact wear. This is why periodic inspections are important.
Table 5-4 shows inspection standards and Table 5-5 shows
inspection procedures.
Table 5-2 Initial inspection and judgment criteria prior to the operation starting
Inspection item
Criteria
Countermeasures for defects
1. Inspect the area around the terminals to make sure no dust, frag-
ments, pieces of wiring, screws, or other conductive foreign matter
were left behind.
No foreign matter
Vacuum up foreign matter. Wipe the
area with a dry cloth.
2. Inspect the MCCB case and cover to make sure there are no cracks
or damage.
No cracks or damage
Replace the enclosure.
3. Inspect the connector to make sure the conductors are securely
tightened.
Conductors are tightened to the
specified torque
Tighten conductors to the specified
torque.
4. Measure insulation resistance with a 500V DC megger.
5M
:
min.
Replace with a new part.
Note: Do not inspect until you are sure there is no voltage applied to the MCCB terminals.
Table 5-3 Inspection and judgment criteria within one month after the operation starting
Inspection item
Criteria
Countermeasure for defects
1. Loose conductor connectors?
Conductors tightened at the
specified torque
Tighten conductors at the specified
torque.
2. Inspect the area around the terminals to make sure no dust, frag-
ments, pieces of wiring, screws, or other conductive foreign matter
were left behind.
No noticeable dust, oil or
conductive foreign matter
Vacuum up the foreign matter. Wipe
the area with a dry cloth.
3. No abnormal temperature rise?
No discoloration of the terminal
connectors or molded plastic due
to excessive heat
Replace with a new part.
Note: Do not inspect until you are sure there is no voltage applied to the MCCB terminals.
5-2 Periodic inspections
5-2-1 Initial inspection
When newly installed equipment first goes into operation,
there may be unexpected oversights or mistakes such that
screws were not properly tightened or cable connections were
incorrect. This is why the items shown in Tables 5-2 and 5-3
should be inspected before initial operation and again within
the following month.