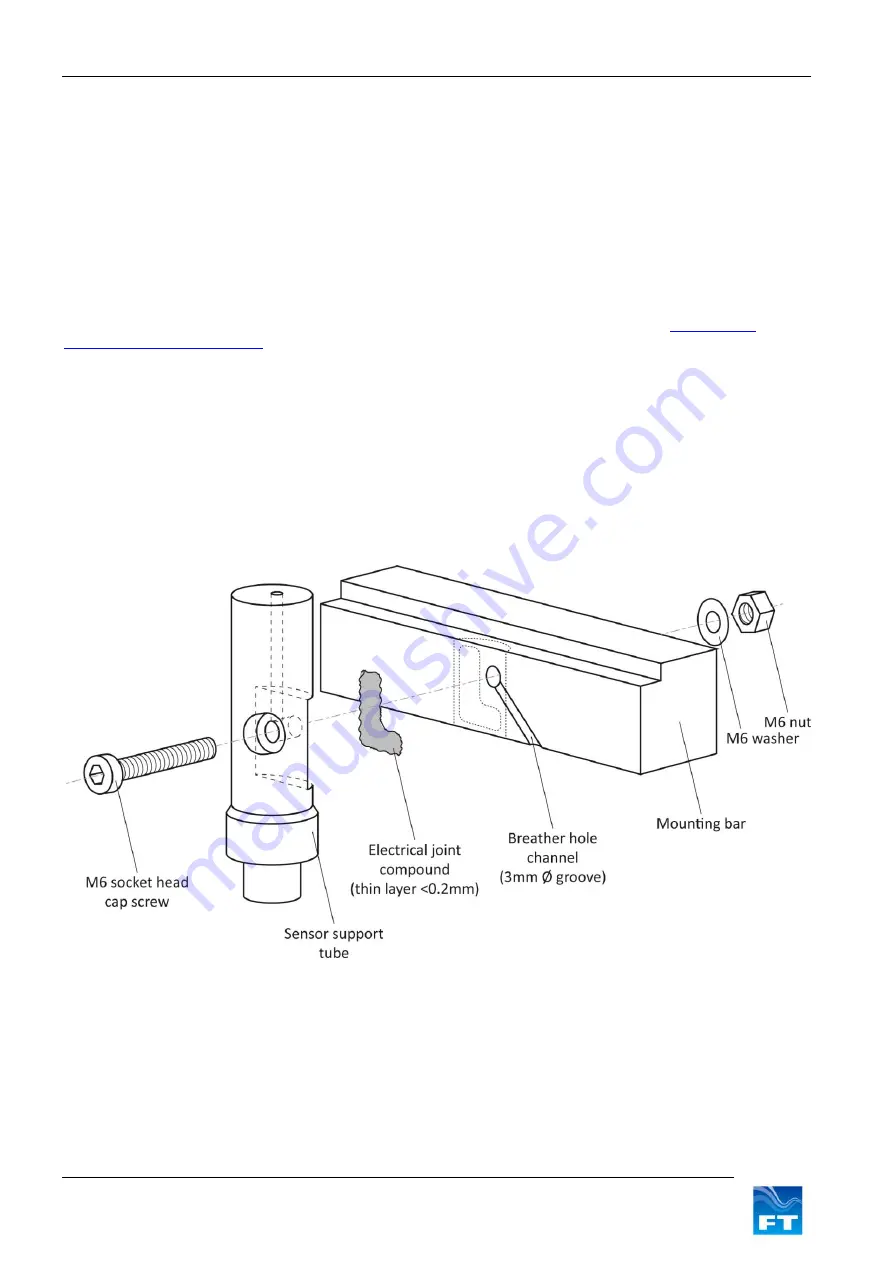
Section 3
Installation
14
FT702LT Flat Front Wind Sensor Manual
3.2 Description of Parts
The FT702LT is designed to be mounted using an M6 socket head cap screw, nut and washer. The mounting
flat on the support tube of the sensor (see Figure 7) allows for firm fitting against a flat surface. The preferred
finish of the screw, nut, washer and the mounting bar is hot dipped galvanised steel.
The mounting bar should have a minimum galvanising thickness of 50µm to ensure long-term protection against
corrosion. The galvanising quality should conform to ASTM A123, Standard Specification for Zinc (Hot-Dip
Galvanised) Coatings on Iron & Steel Products. Aluminium components of the appropriate grade could be used
as an alternative.
The mounting flat is provided free of coatings to allow for a good electrical connection between the body of the
sensor and ground through the mounting bar. In order to protect the mounting flat against corrosion, a very thin
layer (<0.2mm) of electrical joint compound should be applied. An example of this could be
. It should be applied directly to the sensor’s mounting flat, whilst avoiding the
fixing hole. Use of an electrical joint compound will also help to maintain long-term low impedance connection to
ground. This connection should be checked as part of the annual inspection of the sensor as detailed in Section
3.4.
Some electrical joint compounds contain fluoride etchants which may react with certain materials. Material
compatibility should therefore be checked prior to application (refer to the electrical joint compound
manufacturer
’s data).
In order to keep the pressure within the sensor equalised with the atmospheric pressure, a small breather hole
is located within its support tube. It is therefore important that the airway to this breather hole be kept clear. This
can be achievable by cutting a small 3mm channel in the mounting bar as shown (see Figure 7).
Figure 7: Sensor Installation
It is recommended that a protective sleeve be fitted over the base of the sensor and the connector. This will
provide environmental protection as well as stress-relief from vibration. Heat shrink or cold shrink would be
suitable for this purpose. FT offers a cold shrink solution which is available on request (part number FT909).
The sleeve should cover the lower part of the support tube, the connector itself and at least 25mm of cable, (see
Figure 8).