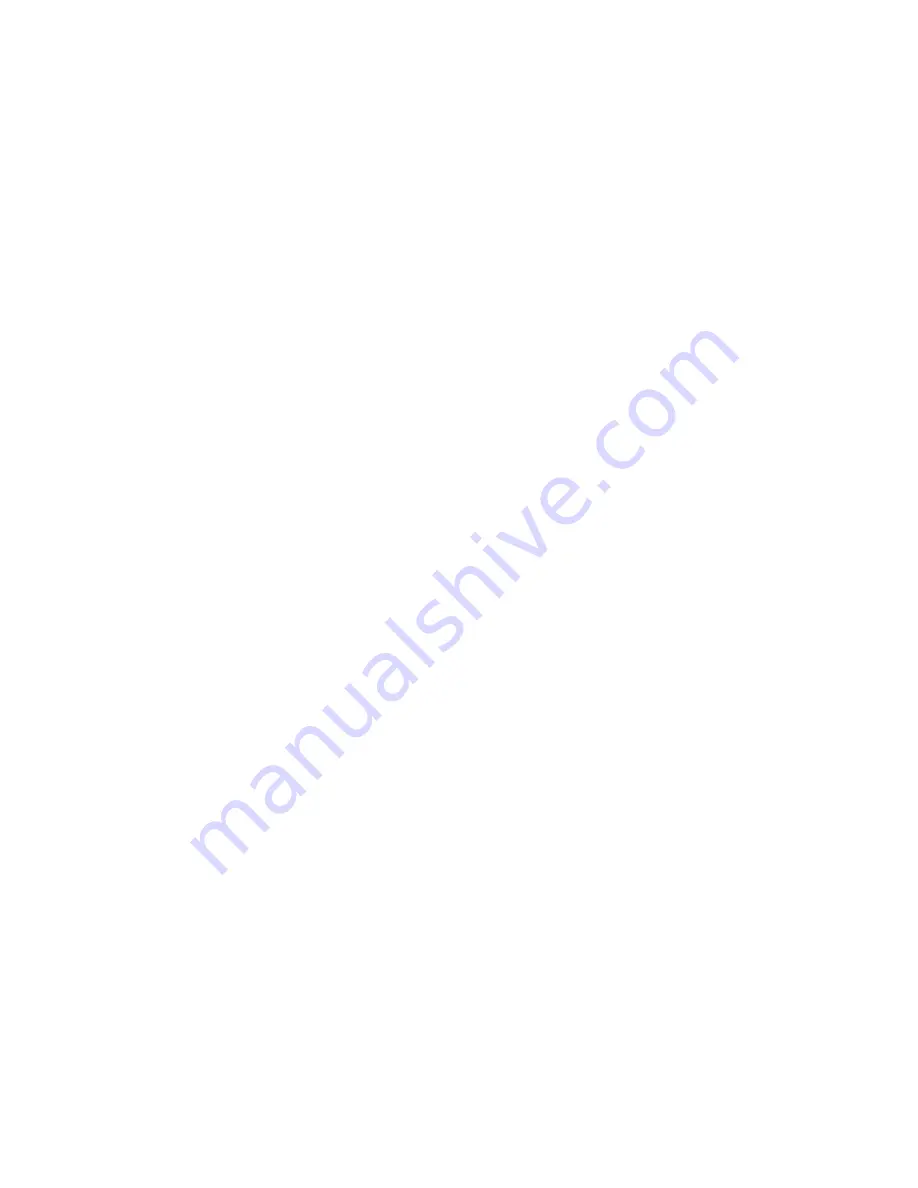
1-22
11.
Remove the upper burner rails (11).
NOTE:
For the following steps, refer to the frypot exploded
view on page 1-24 for component identification.
12.
Remove any residual insulation, sealant, and/or oil from the exterior of the frypot.
13.
Place the “L” shaped pieces of the combustion chamber insulation (1) in the front and rear
corners of both upper rail-retaining slots. (See page 1-24).
14.
Using a mallet and short piece of wood, tap the corner tabs of the combustion chamber over the
insulation to ensure a solid seal of the burner.
15.
Install the upper burner rails (2) with the heat deflectors slanting toward the rear of the frypot.
The rails will cover the “L” shaped pieces of combustion chamber insulation previously
installed.
16.
Place the upper inner combustion chamber insulation and insulation retainers (3) on the top two
studs on each side of the front of the frypot and secure with ¼”-20 washer-nuts.
It is normal for
the retainers to slice off the overhanging insulation.
17.
Place the lower rear combustion chamber insulation (4) on the lower four studs at the rear of the
frypot.
18.
Place one 1.625-inch tubular spacer (5) on each of the flue assembly (upper) studs at the rear of
the frypot.
NOTE:
There are three different sizes of spacers. Verify the size to ensure the
correct spacers are installed.
19.
Press the flue assembly (6) over the burner rails. It may be necessary to use a rubber mallet or
screwdriver to align the components. Use four ¼”-20 washer nuts to secure the flue assembly.
Do not tighten the retainer nuts at this point. They should be finger-tight only.
NOTE:
The flue edge will cover one to two inches of the lower insulation.
20.
Install the lower rear combustion chamber back(s) and retainer(s) (7) with the flanged edge(s)
against the flue. Secure with ¼”-20 washer nuts.
NOTE:
Full-vat units have two-piece backs
and four retainers. Dual-vat units come with one-piece backs and only two retainers.
21.
Insert the burners (9) into the rails to ensure the rail spacing and alignments are correct. The
burner should slide freely into and out of the rails. The upper rail can be bent slightly to increase
or decrease tension on the burner and the edges of the slot can be closed or opened slightly to
best fit the burner frame.
22.
Carefully wrap a strip of burner insulation (8) tightly around the rear and sides of the burner
frame (9), with the glass-tape side of the strip on the outside.
Do not use duct tape or adhesive
to secure the strip to the burner frame.
23.
Align the burner to the burner rails while maintaining tension on the insulation strip. Insert the
burner at a slight angle and begin pushing the burner slowly into the rails until it contacts the
rear combustion chamber. The fit should be snug, but not excessively tight.
Summary of Contents for BIPH52 Series
Page 28: ...1 21 Disassembling A Frypot Full Vat Illustrated Spacers Spacer 10 2 3 4 5 6 7 8 1 11 9 ...
Page 46: ...1 39 1 11 2 Transformer Filter Boxes 1 11 2 1 MPH152 155 Transformer Filter Box ...
Page 48: ...1 41 1 11 2 3 BIPH252 255 and 452 455 Transformer Filter Box International 8051340C ...
Page 50: ...1 43 1 11 2 5 BIPH352 355 Transformer Filter Box International ...
Page 66: ...2 13 2 4 2 Drain Valves and Associated Components ...
Page 68: ...2 15 2 4 3 Rear Flush Oil Return Line Components ...
Page 72: ...2 19 2 5 2 Transformer Boxes ...
Page 76: ...2 23 2 7 Frypots and Associated Components 2 7 1 Full Vat Frypot Components ...
Page 78: ...2 25 2 7 2 Dual Vat Frypot Components ...
Page 86: ...2 33 Transformer Box Cable Assemblies 1 2 3 4 5 6 7 8 9 10 11 ...