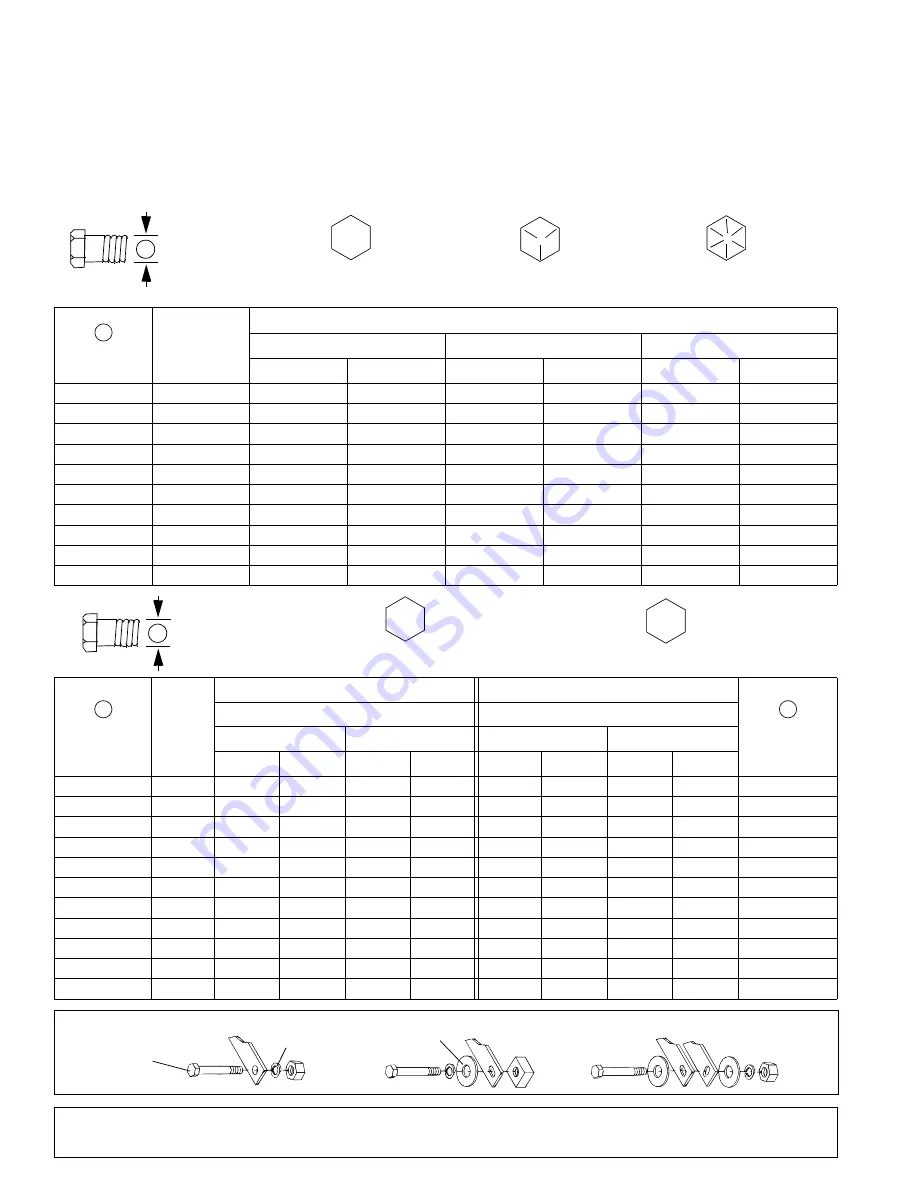
22
Appendix
Bolt Torque & Size Charts (Rev. 3/28/2007)
BOLT TORQUE CHART
Always tighten hardware to these values unless a different torque value or tightening procedure is listed for a specific
application.
Fasteners must always be replaced with the same grade as specified in the manual parts list.
Always use the proper tool for tightening hardware: SAE for SAE hardware and Metric for metric hardware.
Make sure fastener threads are clean and you start thread engagement properly.
All torque values are given to specifications used on hardware defined by SAE J1701 MAR 99 & J1701M JUL 96.
Diameter
(Inches)
Wrench
Size
MARKING ON HEAD
SAE 2
SAE 5
SAE 8
lbs-ft
N-m
lbs-ft
N-m
lbs-ft
N-m
1/4"
7/16"
6
8
10
13
14
18
5/16"
1/2"
12
17
19
26
27
37
3/8"
9/16"
23
31
35
47
49
67
7/16"
5/8"
36
48
55
75
78
106
1/2"
3/4"
55
75
85
115
120
163
9/16"
13/16"
78
106
121
164
171
232
5/8"
15/16"
110
149
170
230
240
325
3/4"
1-1/8"
192
261
297
403
420
569
7/8"
1-5/16"
306
416
474
642
669
907
1"
1-1/2"
467
634
722
979
1020
1383
Diameter &
Thread Pitch
(Millimeters)
Wrench
Size
Coarse Thread
Fine Thread
Diameter &
Thread Pitch
(Millimeters)
Marking on Head
Marking on Head
Metric 8.8
Metric 10.9
Metric 8.8
Metric 10.9
N-m
lbs-ft
N-m
lbs-ft
N-m
lbs-ft
N-m
lbs-ft
6 x 1.0
10 mm
8
6
11
8
8
6
11
8
6 x 1.0
8 x 1.25
13 mm
20
15
27
20
21
16
29
22
8 x 1.0
10 x 1.5
16 mm
39
29
54
40
41
30
57
42
10 x 1.25
12 x 1.75
18 mm
68
50
94
70
75
55
103
76
12 x 1.25
14 x 2.0
21 mm
109
80
151
111
118
87
163
120
14 x 1.5
16 x 2.0
24 mm
169
125
234
173
181
133
250
184
16 x 1.5
18 x 2.5
27 mm
234
172
323
239
263
194
363
268
18 x 1.5
20 x 2.5
30 mm
330
244
457
337
367
270
507
374
20 x 1.5
22 x 2.5
34 mm
451
332
623
460
495
365
684
505
22 x 1.5
24 x 3.0
36 mm
571
421
790
583
623
459
861
635
24 x 2.0
30 x 3.0
46 mm
1175
867
1626
1199
1258
928
1740
1283
30 x 2.0
A
SAE SERIES
TORQUE
CHART
SAE Bolt Head
Identification
SAE Grade 2
(No Dashes)
SAE Grade 5
(3 Radial Dashes)
SAE Grade 8
(6 Radial Dashes)
A
METRIC SERIES
TORQUE
CHART
Metric Bolt Head
Identification
8.8
Metric
Grade 10.9
10.9
Metric
Grade 8.8
A
A
A
Typical Washer
Installations
Lock Washer
Flat Washer
8/9/00
Bolt