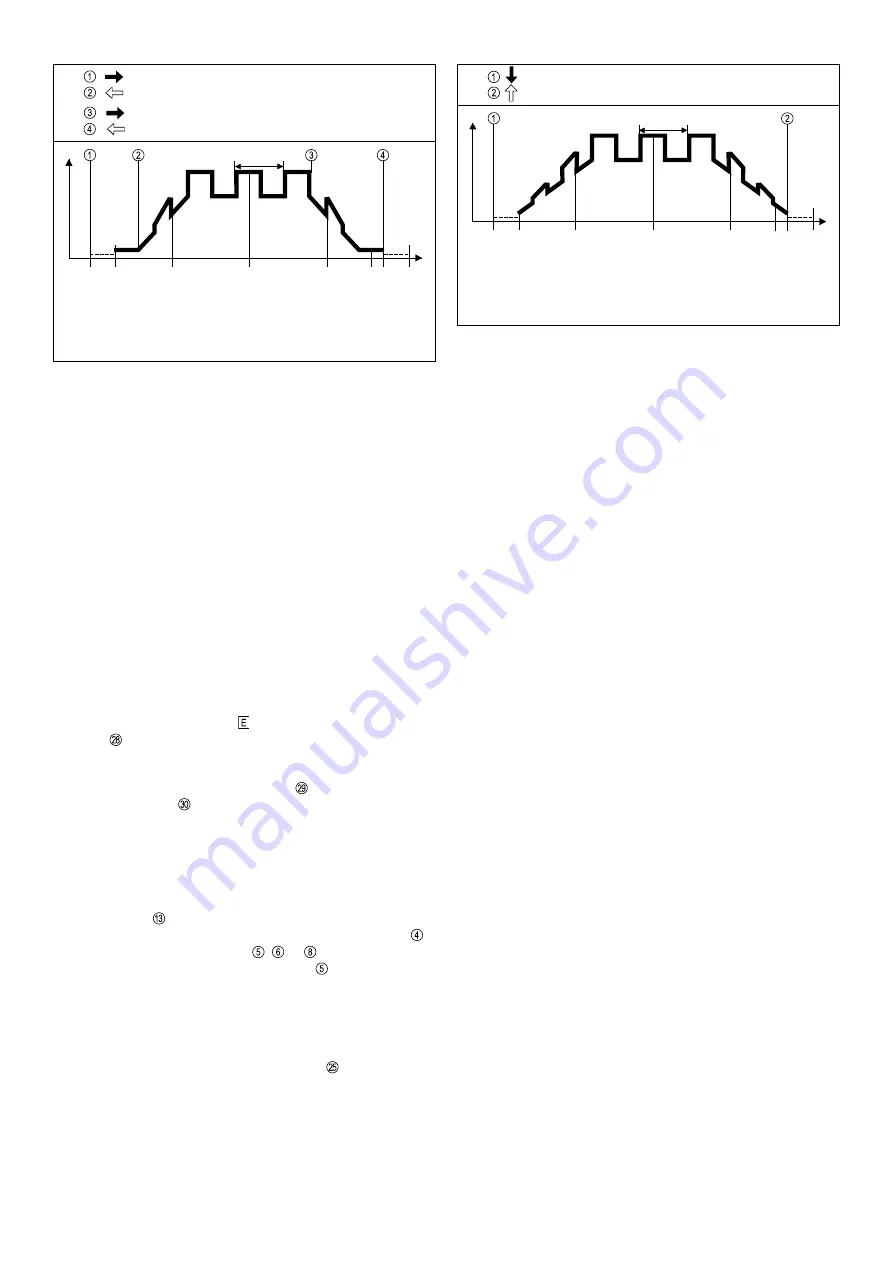
16
Practical hint!
When FRONIUS welding torches with twin-function triggers are
used, the facility for lowering the current from main current to
crater-fill current and back again, without interrupting the welding
sequence, is available in the pulsed-arc operating mode as well.
For details of the functional sequence, see "Description of 4-step
operation / variant 2"
(page 9, 10 Fig. 7).
Description of operating mode --> regulation of pulse
current I
1
using TR 52mc remote-control pedal unit
A combination of the REMOTE CONTROL PULSING UNIT and
the REMOTE CONTROL PEDAL UNIT is particularly advantage-
ous with manual TIG welding in cases where it is necessary to alter
the welding pulse current during the welding operation.
(Where
the welder is dealing with materials of different strengths, for
example)
.
Connecting the remote control unit:
- Link the connecting socket on the power source and the
socket on the remote-control pulsing unit electrically with the
remote control cable.
- A remote control cable of the same type may be used for linking
the remote-control pulsing unit
(socket )
to the remote control
pedal unit
(socket )
.
- Plug in the pug-in connections the right way round, and screw
the coupling ring on as far as possible.
Functional description:
- When the TR 52mc remote-control pedal unit is connected, the
machine automatically switches over to 2-step operation.
- LED indicator blinks up on the power source
- Set desired operating mode with function selector switch
- The appropriate LED indicator , or lights up -
operating mode electrode
(LED indicator )
is possible
- The mean welding-current amperage is indicated on display A.
- No "Hold" function
- To initiate the ignition process, gently step on the pedal.
- The level of the start arc current, the pulse current I
1
and the final
crater current can also be controlled from the pedal.
- The base current I
2
that is set using the dial on the TR 50mc
is a constant percentage of the value of the pulse current I
1
.
- When the welder takes his foot right off the pedal, the welding
current is switched off, thus interrupting the welding operation.
- Gas post-flow time elapses.
Pedal pressed down
ð
"Welding ON"
Foot off the pedal
ð
"Welding OFF"
Fig.17
Functional sequence in pulsed-arc operation, in conjunction with the
TR52mc remote-control pedal unit (2-step)
I
1
I
2
I
t
Start of cycle
Gas pre-flow time
Pulsed current rise,
controlled from pedal
Gas post-flow time
End of welding
Welding in pulsed-arc
mode: I
1
- I
2
Arc ignition with minimum current
Pulsed current drop, controlled from pedal
f
(Hz)
Release the torch trigger
Pull back and hold down the trigger once again
Fig.16
Functional sequence in pulsed-arc welding operation using TR 50mc (4-step)
I
S
I
1
I
2
I
t
Pull back torch trigger and hold down
Release the torch trigger
I
E
Start of cycle
Gas pre-flow time
Pulsed current rise via
upslope
Gas post-flow time
End of welding
Welding in pulsed-arc
mode: I1, I2 / f / duty
cycle
Arc ignition with start-
arc current I
S
Pulsed current drop
via downslope
Crater-fill current
f
(Hz)
Crater-fill current
Summary of Contents for MAGIC WAVE 2000 FUZZY
Page 2: ...2...
Page 25: ...1 ENGLISH OPERATING INSTRUCTIONS...
Page 26: ...2...
Page 49: ...1 FRAN AIS MODE D EMPLOI...
Page 50: ...2...
Page 73: ...ERSATZTEILLISTE SPARE PARTS LIST LISTE DE PI CES DE RECHANGE ud_fr_st_tb_00150 012000...