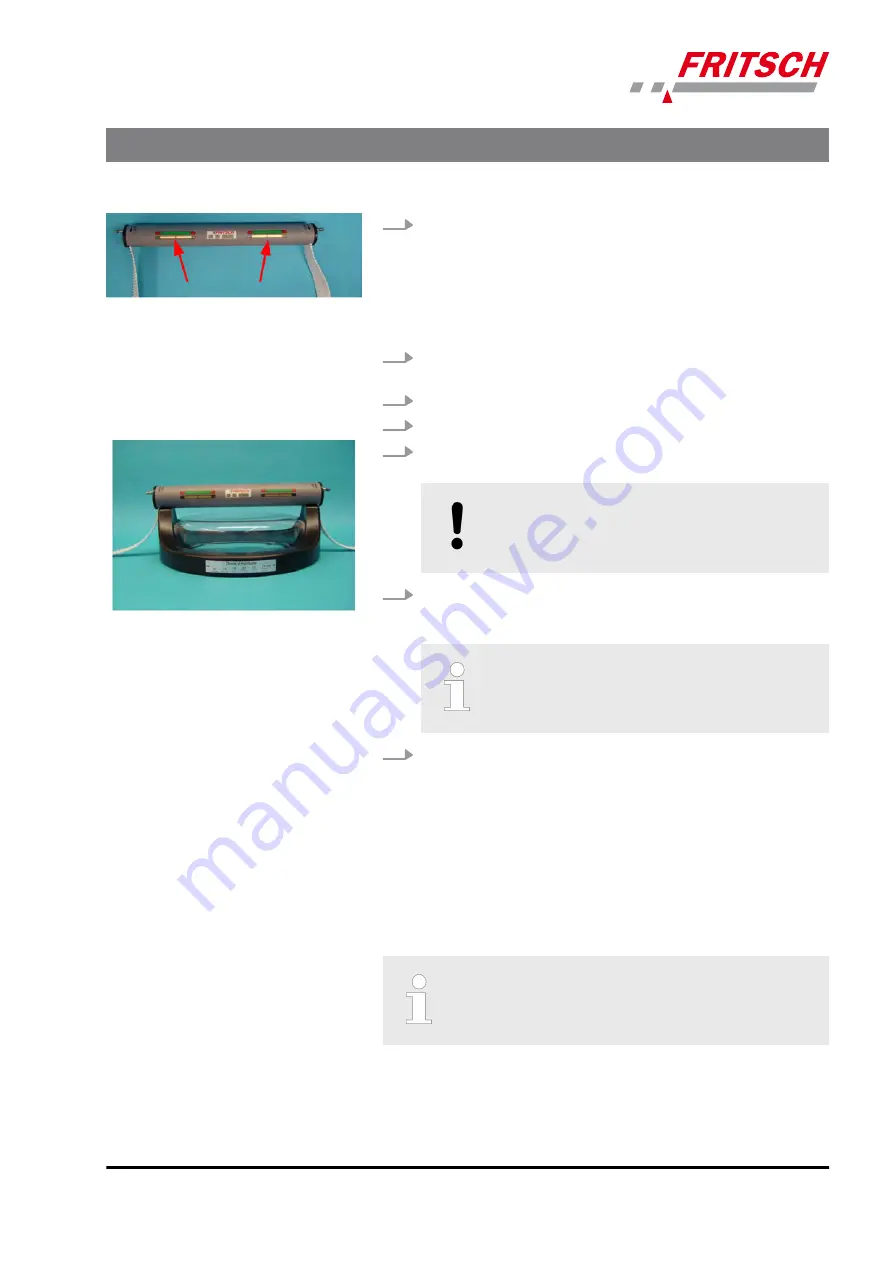
1.
The starting position of the clamping system is the position at
which both indicators are roughly in the centre of the respective
display range.
This position later ensures that sieve stacks of various heights can
be clamped easily, or that there is sufficient space to release the
system, remove it from the sieve stack and place it behind the
device.
2.
Insert the toothed belt in the belt clamping device as described in
Chapter 7.2.1.2 ‘Fitting and clamping the sieves’ on page 26.
3.
Insert the sieve set and pour in the sieving stock.
4.
Fit the TorqueMaster clamping lid.
5.
Place the clamping unit on the clamping lid. The clamping unit
must be fitted as centrally as possible.
NOTICE!
This symmetry is ensured by correctly adjusting and
securing the toothed belt.
6.
Lightly tighten the toothed belts on both sides and move the
clamping lever upwards, as described in
and clamping the sieves’ on page 26 under point 9.
Make sure that both indicators remain in their central
position.
7.
The clamping system can now be clamped using the cordless
screwdriver.
7.2.7.2
Clamping the TorqueMaster
Clamping with a cordless screwdriver until it disengages applies a repro-
ducible force of ~ 1 kN to the sieve cover.
Clamping processes during which the friction clutch of the cordless
screwdriver does not disengage (e.g. due to defect, dead battery or
operating error) do not provide the desired clamping force.
The correct clamping force is only achieved if the friction
clutch of the cordless screwdriver triggers during the
clamping process.
Accessories
- 35 -
Summary of Contents for PULVERISETTE 0
Page 6: ...13 Exclusion of liability 46 14 Safety logbook 48 15 Index 50 Table of contents 6 ...
Page 40: ...NOTICE The plexiglas lid must not be cleaned with alcohol or organic solvents Cleaning 40 ...
Page 48: ...14 Safety logbook Date Maintenance Repair Name Signature Safety logbook 48 ...
Page 49: ...Date Maintenance Repair Name Signature Safety logbook 49 ...
Page 51: ......