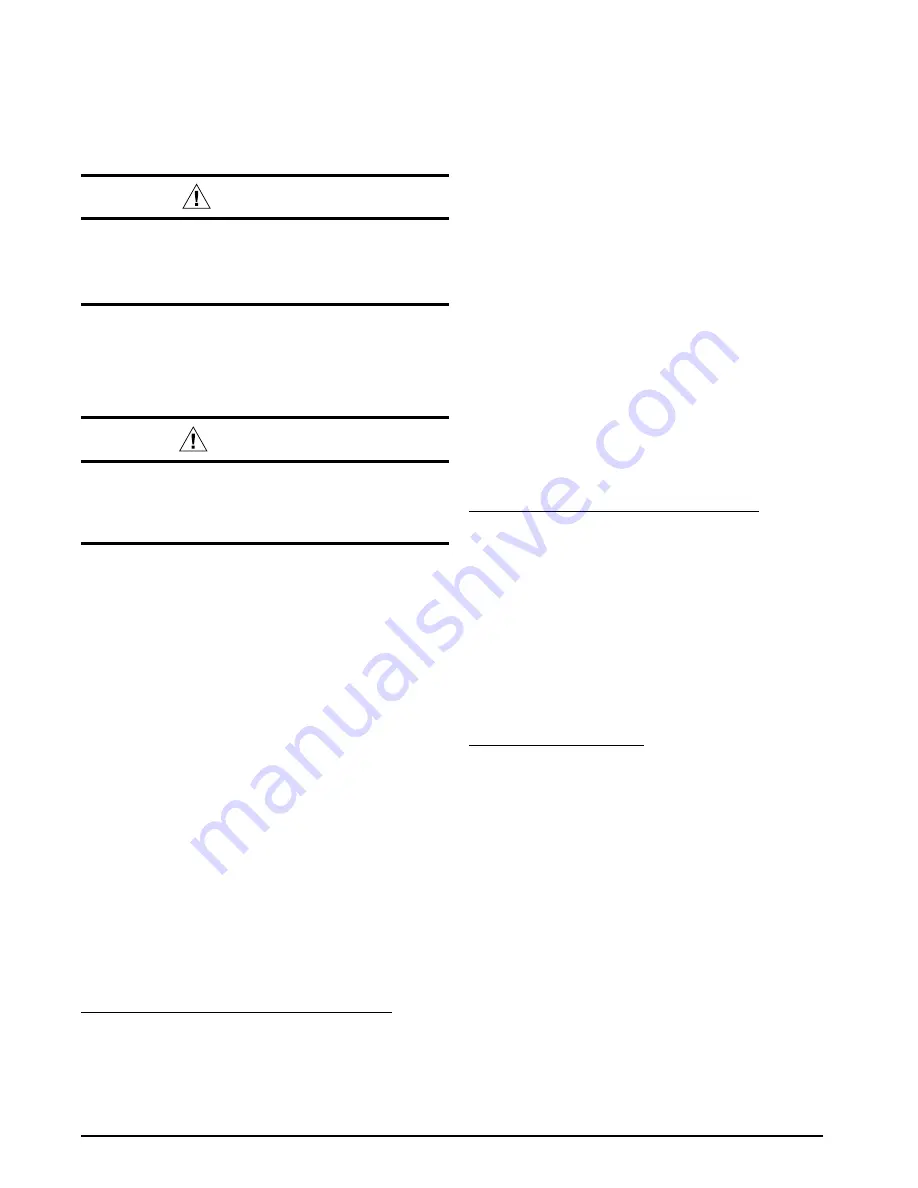
9
for connecting the supply wires to the unit. Use of rain
tight conduit is recommended.
• See the unit wiring label for proper high and low voltage
wiring. Make all electrical connections in accordance
with all applicable codes and ordinances.
cauTion:
label all wires prior to disconnection when
servicing controls. wiring errors can cause
improper and dangerous operation. Verify proper
operation after servicing.
•
Units are shipped from the factory wired for 240 volt
transformer operation. For 208V operation, remove the
lead from the transformer terminal marked 240V and
connect it to the terminal marked 208V.
Table 4 (page 10) lists the basic airflow values versus the
airflow selector switch settings and the range of basic
air flow settings recommended for each nominal system
capacity.
noTeS:
•
The CFM values listed in the tables are not dependent
on duct static pressure. The motor automatically
compensates for changes in duct static pressure (within
the limits of the motor).
•
For maximum capacity and energy efficiency, select an
airflow at or near the top of the range for that nominal
capacity.
•
For maximum dehumidification, select an airflow near
the middle or bottom of the range for that nominal
capacity. Additional information on humidification and
dehumidification can be found on page 13.
• If
coil icing is observed, the basic cooling/heat-pump
airflow selected may be too low. Check the setting and
make sure it is within the range shown in Table 4. Also
verify the system is properly charged. See charging
charts on pages 20 - 21. If icing continues to occur,
raise the selected airflow one or two steps.
Selecting the Minimum Electric Heat Airflow
The minimum electric heat airflow is selected by setting
switches 5 and 6. Selecting the minimum electric heat
airflow sets the minimum air flow that will be produced
whenever electric heater kits are used. When the electric
heater kits are energized along with a heat pump, the
airflow may be higher depending on the basic cooling/
heat-pump airflow setting.
See Table 2 (page 10) for recommended minimum electric
heat airflow settings. The minimum electric heat airflow
setting may be set higher, but must never be set lower
than the setting shown in the table.
Selecting the Delay Profile
Delay profile selection controls the start-up and shut-down
characteristics of the packaged heat pump unit. By varying
the start-up and shut-down characteristics, the system can
be optimized for energy efficiency, humidity control, and
comfort. The delay profile is selected by setting switches
7 & 8 (See Table 3 page 10).
Select Delay a or Delay b
for highest energy efficiency:
•
Delay a has a two-step ON delay. The blower will
begin operation at 31% airflow for 30 seconds. The
second step operation is 75% airflow for 30 seconds.
After the two-step ON delay has been completed, the
blower operation will run at 100% until the thermostat
has been satisfied. Delay a also provides a 60 second
OFF delay at 50% airflow.
•
Delay b has a single step 30 second ON delay at 50%
airflow and also provides a 90 second OFF delay at
50% airflow. Select the delay profile which is most
suited to the application. See Table 3.
•
The DeHum delay profile may be used when humidity
control is needed without the use of an optional
grounding
waRning:
The unit cabinet must have an uninterrupted or
unbroken electrical ground to minimize personal
injury if an electrical fault should occur. Do not
use gas piping as an electrical ground
!
This unit must be electrically grounded in accordance
with local codes or, in the absence of local codes, with
the National Electrical Code (ANSI/NFPA 70) or the CSA
C22.1 Electrical Code. Use the grounding lug provided in
the control box for grounding the unit.
Selecting Proper airflow for Variable Speed units
Th Q4SE packaged heat pump is equipped with a
microprocessor-controlled variable speed motor that is
pre-programmed to deliver optimum airflow in a variety of
conditions and system configurations. The unit responds
directly to the thermostat inputs, as well as the optional
humidistat (If installed). During normal operation, the motor
will gradually change speeds during start-up, shut down,
when thermostat inputs change, and when the duct static
pressure changes (vents closed or opened, filter clogging,
etc.). The heat pump unit is also configured by setting
the selector switches and removing jumper connectors
as directed below.
noTe: This packaged heat pump has been designed to
give the installer maximum flexibility to optimize system
performance, efficiency, and comfort. With so many
different ways to set up the packaged heat pump, it is
important to read and follow all directions carefully.
Selecting the Basic Cooling/Heat Pump Airflow
The basic cooling/heat-pump airflow is selected by setting
switches 1 - 4 on the thermostat input board located on the
blower. All airflows for other modes of operation (except
electric heat) are determined by this basic setting.