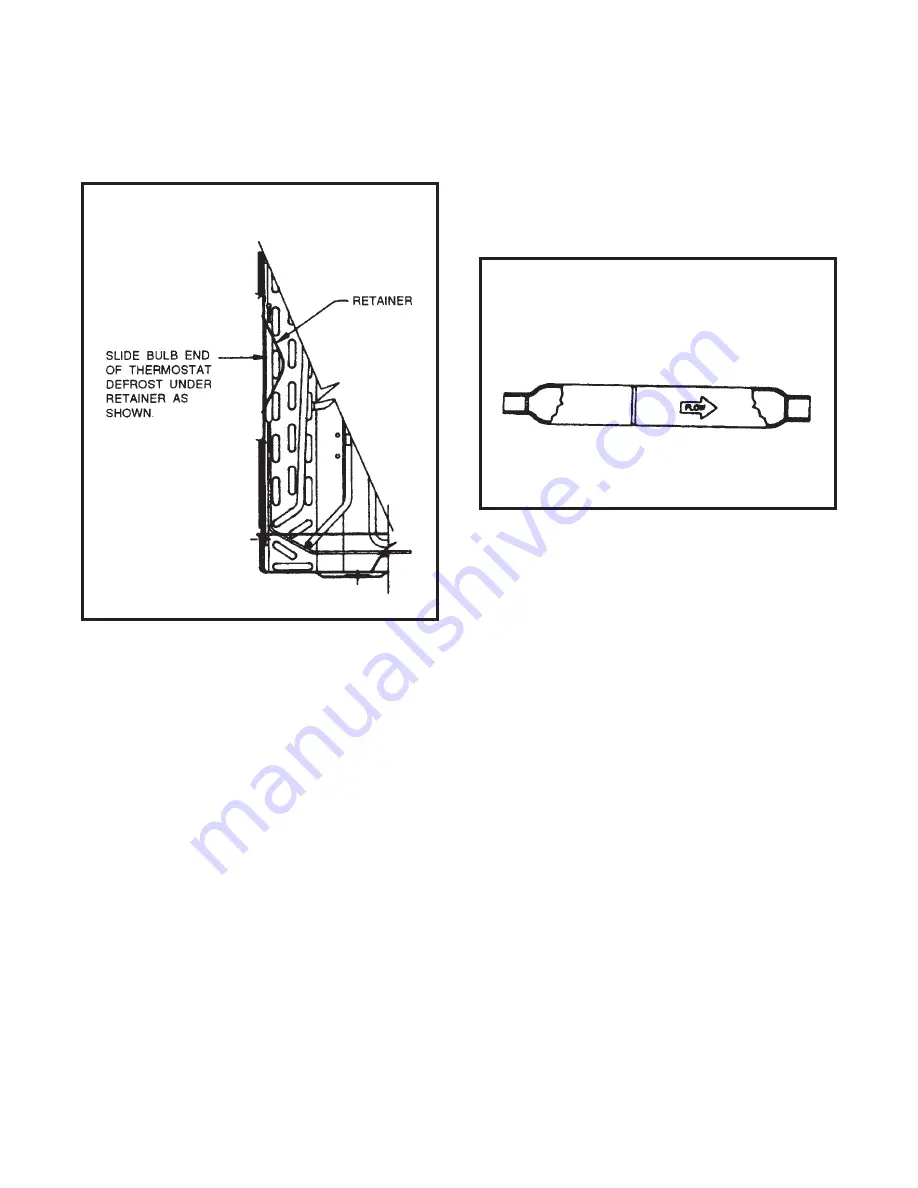
(Page 22 of 64)
TTJ-0197 (1/97)
DEFROST BULB LOCATION
(Heat Pump Models Only)
The defrost control bulb must be mounted securely and
in the correct location to operate properly (see Figure
14.)
Figure 14: DEFROST THERMOSTAT BULB
LOCATION (All Heat Pump Models)
CHECK VALVE (Figure 15)
(Heat Pump Models Only)
A one-way check valve is installed in the capillary tube
circuit to allow the flow of refrigerant through both tubes
to the evaporator during the cooling mode.
In the heating mode, one capillary is closed by the check
valve to allow flow through one capillary only to the
condenser.
Figure 15:
ONE-WAY CHECK VALVE
(Heat Pump Models)
NOTE: The slide (check) inside the valve is made of
teflon. Should it become necessary to replace
the check valve, place a wet cloth around the
valve to prevent overheating during the brazing
operation. The flow arrow on the valve must
point toward the evaporator.
VALVE, DRAIN PAN (see Figure 16)
During the cooling mode of operation, condensate which
collects in the drain pan is picked up by the condenser
fan blade and sprayed onto the condenser coil. This
assists in cooling the refrigerant plus evaporating the
water.
During the heating mode of operation, it is necessary
that water be removed to prevent it from freezing dur-
ing cold outside temperatures. This could cause the con-
denser fan blade to freeze in the accumulated water
and prevent it from turning.
To provide a means of draining this water, a bellows
type drain valve is installed over a drain opening in the
base pan.
SOLENOID COIL
(Heat Pump Models Only)
The solenoid coil is an electromagnetic type coil
mounted on the reversing valve and is energized dur-
ing the operation of the compressor in the heating cycle.
Should the reversing valve fail to shift during the heat-
ing cycle, test the solenoid coil. Also, refer to Touch
Test Chart on page 26.
TO TEST:
1.
Disconnect power to unit.
2.
Disconnect coil leads.
3.
Attach probes of ana ohmmeter to each coil lead
and check for continuity.
NOTE: Do not start unit with solenoid coil removed from
valve, or do not remove coil after unit is in op-
eration. This will cause the coil to burn out.
Summary of Contents for YL24J35
Page 7: ...TTJ 0197 1 97 Page 7 of 64 COOLING LOAD ESTIMATE FORM...
Page 9: ...TTJ 0197 1 97 Page 9 of 64...
Page 14: ...Page 14 of 64 TTJ 0197 1 97...
Page 26: ...Page 26 of 64 TTJ 0197 1 97...
Page 27: ...TTJ 0197 1 97 Page 27 of 64...
Page 28: ...Page 28 of 64 TTJ 0197 1 97...
Page 29: ...TTJ 0197 1 97 Page 29 of 64...
Page 30: ...Page 30 of 64 TTJ 0197 1 97...
Page 31: ...TTJ 0197 1 97 Page 31 of 64...
Page 32: ...Page 32 of 64 TTJ 0197 1 97...
Page 33: ...TTJ 0197 1 97 Page 33 of 64...
Page 34: ...Page 34 of 64 TTJ 0197 1 97...
Page 35: ...TTJ 0197 1 97 Page 35 of 64...
Page 36: ...Page 36 of 64 TTJ 0197 1 97...
Page 37: ...TTJ 0197 1 97 Page 37 of 64 WIRING DIAGRAM FOR MODELS YS13J33 YM18J34A YL24J35...
Page 39: ...TTJ 0197 1 97 Page 39 of 64...
Page 40: ...Page 40 of 64 TTJ 0197 1 97...
Page 46: ...Page 46 of 64 TTJ 0197 1 97...
Page 47: ...TTJ 0197 1 97 Page 47 of 64...
Page 52: ...Page 52 of 64 TTJ 0197 1 97...
Page 53: ...TTJ 0197 1 97 Page 53 of 64...
Page 57: ...TTJ 0197 1 97 Page 57 of 64...
Page 58: ...Page 58 of 64 TTJ 0197 1 97...