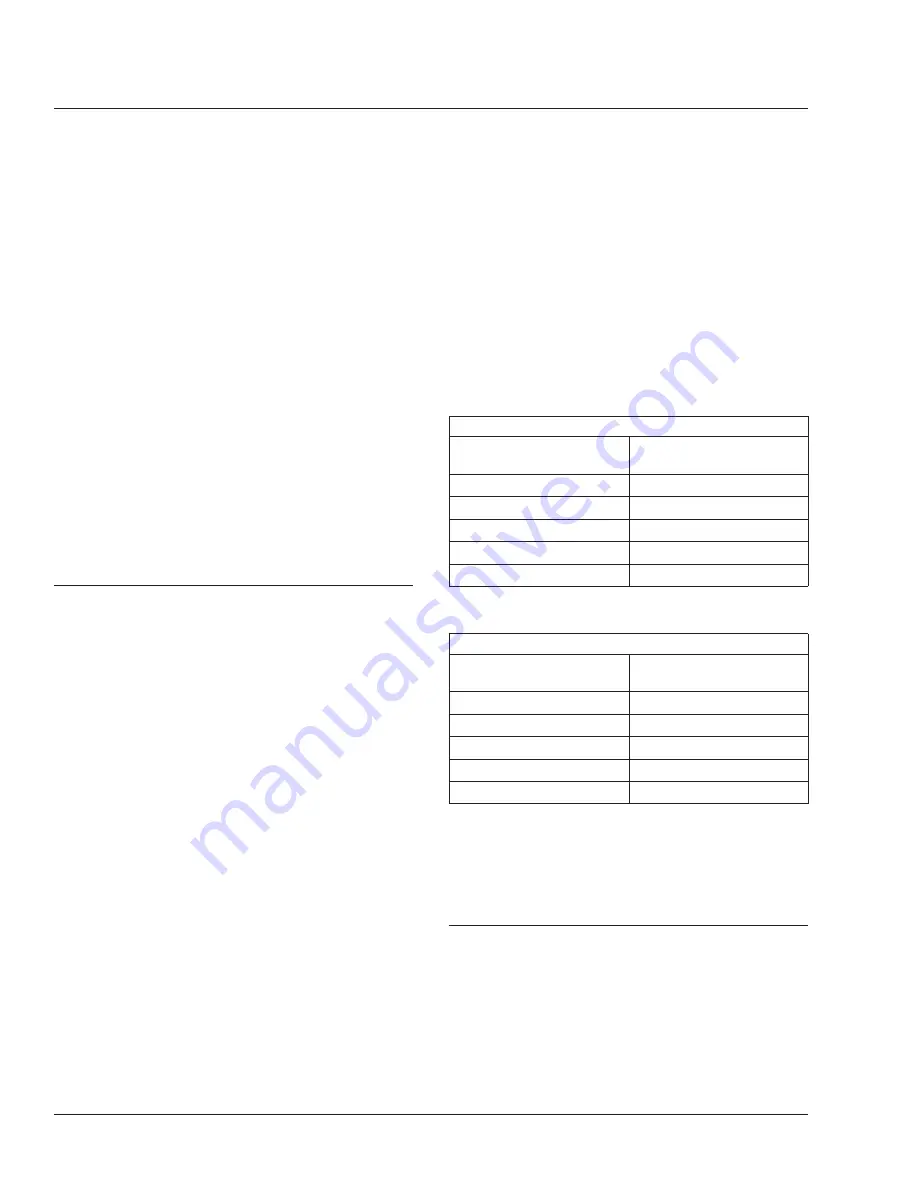
2.
Using a strap wrench, turn the desiccant car-
tridge counterclockwise and remove it.
3.
Remove and discard the O-ring.
4.
Clean the top surface of the dryer base with a
commercial cleaning solvent.
IMPORTANT: If the air dryer base is damaged,
preventing a tight seal, replace the air dryer.
5.
Using a multipurpose, high-temperature grease
that resists water, steam, and alkali, lightly coat
the surfaces of the new O-ring and the dryer
base. Install the O-ring.
6.
Thread the desiccant cartridge onto the dryer
base (turn clockwise). When the seal contacts
the base, tighten the cartridge one complete turn
more. Do not overtighten.
42–11 Versajust Slack Adjuster
Inspection and
Lubrication
IMPORTANT: Perform the
Brake Inspection
maintenance operation before lubricating the
slack adjusters.
1.
Visually check for physical damage, such as bro-
ken air lines and broken or missing parts.
2.
Using a quality multipurpose chassis lubricant,
NLGI Grade 2, lubricate the slack adjuster
through the grease fitting until clean lubricant
flows from the grease relief opening in the boot.
3.
Perform the "In Service Inspection."
In Service Inspection
1.
Apply and release the brakes several times while
observing the slack adjuster. The slack adjuster
and brake actuator should move freely, without
binding or interference, and should return to the
full released position. Observe the looseness that
exists between the clevis and adapter bushing
and the yoke and link pins and their mating parts
(clevis, body, link). Replace these parts if loose-
ness appears excessive. Make certain the brake
actuator pushrod jam nut is tightened securely.
2.
Inspect the slack adjuster for physical damage,
paying attention to the link, boot, and clevis. If
any components are damaged, repair or replace
them as necessary.
3.
Measure the brake actuator pushrod stroke while
making an 80 to 90 psi (552 to 621 kPa) brake
application. Actuator pushrod strokes should not
exceed the values shown in
and
. To achieve the correct pressure for this
test, build the system pressure up to a 100 psi
(690 kPa). Shut down the engine. Fan the
brakes to attain a 90 to 95 psi (621 to 655 kPa)
reading. Make and hold a full brake application
while the strokes are checked.
Actuator Stroke–Standard Stroke
Brake Actuator Size
Recommended Maximum
Operating Stroke (Inches)
30
2
24
1-3/4
20
1-3/4
16
1-3/4
12
1-3/8
Table 3, Actuator Stroke–Standard Stroke
Actuator Stroke–Long Stroke
Brake Actuator Size
Recommended Maximum
Operating Stroke (Inches)
30 Long Stroke
2-1/2
24 Long
2
24 Long Stroke
2-1/2
20 Long
2
16 Long
2
Table 4, Actuator Stroke–Long Stroke
42–12 Bendix Automatic Drain
Valve Operating and
Leakage Tests
Operating Test
Perform the following test after repairing or replacing
the DV-2 valve, to ensure that the valve is function-
ing properly.
With the system charged, apply the brakes several
times. Each time the brakes are applied, an exhaust
Brakes
42
108SD and 114SD Maintenance Manual, October 2019
42/18
Summary of Contents for 108SD 2021
Page 3: ......
Page 11: ......
Page 27: ......
Page 31: ......
Page 33: ......
Page 35: ......
Page 37: ......
Page 39: ......
Page 41: ......
Page 43: ......
Page 45: ......
Page 49: ......
Page 51: ......
Page 57: ......
Page 59: ......
Page 67: ......
Page 77: ......
Page 85: ......
Page 87: ......
Page 97: ......
Page 107: ......
Page 109: ......
Page 111: ......
Page 117: ......
Page 119: ......
Page 139: ......
Page 141: ......
Page 145: ......
Page 147: ......
Page 161: ......
Page 163: ......
Page 173: ......
Page 177: ......
Page 179: ......
Page 181: ......
Page 183: ......
Page 185: ......
Page 189: ......
Page 191: ......