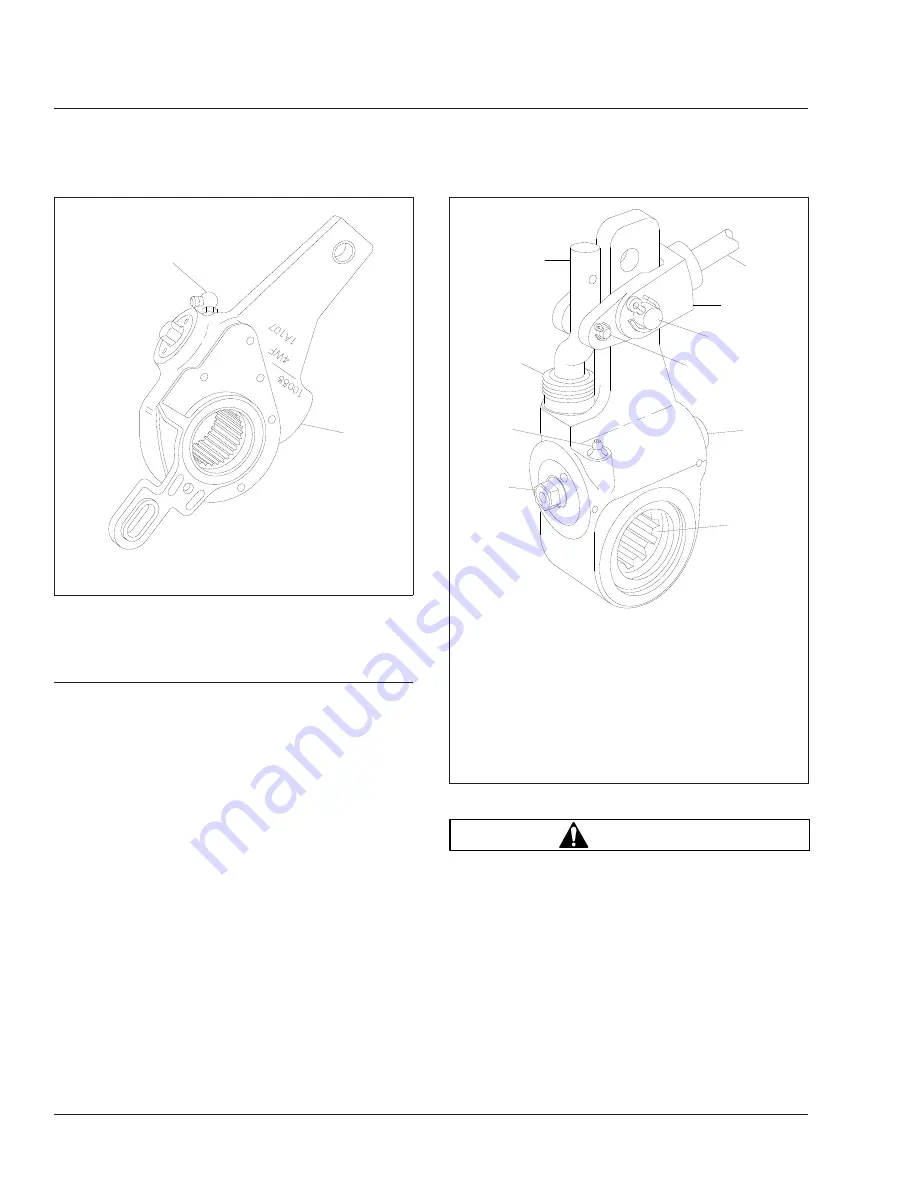
42–07 Meritor Camshaft
Bracket Lubrication
IMPORTANT: Perform
before lubri-
cating the camshaft brackets.
NOTE: If equipped with an extended-
maintenance Q Plus
™
brake system, the cam-
shaft bracket will not have a grease fitting.
These camshafts use a special NLGI grade syn-
thetic polyurea grease, and do not require lubri-
cation for 3 years or 500,000 miles (800 000
km), whichever comes first. Extended-
maintenance camshaft bushings are lubricated
during the brake reline service interval. For ser-
vice and lubrication instructions, see
Group 42
of the
108SD and 114SD Workshop Manual
.
For camshaft brackets with grease fittings, use an
NLGI Grade 1 or Grade 2 multipurpose chassis
grease. Lubricate the camshaft bushings through the
grease fitting on the camshaft bracket or the spider
until new grease flows from the inboard seal. See
WARNING
If grease leaks out under the camhead, the cam-
shaft bracket grease seal is worn or damaged. See
Group 42 of the
108SD and 114SD Workshop
Manual
for grease seal replacement instructions. If
this seal is not replaced, the brake linings could
become contaminated with grease. The stopping
distance of the vehicle will be increased, which
could result in personal injury or property dam-
age.
02/01/2001
1
2
f421649a
1.
Grease Fitting
2.
Slack Adjuster
Fig. 10, Haldex Slack Adjuster Grease Fitting
f420653a
1
2
3
4
5
6
7
8
10
9
10/27/93
1.
7/16-Inch Adjusting Nut
2.
Grease Fitting
3.
Boot
4.
Link
5.
Brake Chamber Piston Rod
6.
Clevis
7.
1/2-Inch Clevis Pin
8.
1/4-Inch Clevis Pin
9.
Grease Relief Opening
10. Slack Adjuster Spline
Fig. 11, Gunite Automatic Slack Adjuster
Brakes
42
108SD and 114SD Maintenance Manual, October 2019
42/14
Summary of Contents for 108SD 2021
Page 3: ......
Page 11: ......
Page 27: ......
Page 31: ......
Page 33: ......
Page 35: ......
Page 37: ......
Page 39: ......
Page 41: ......
Page 43: ......
Page 45: ......
Page 49: ......
Page 51: ......
Page 57: ......
Page 59: ......
Page 67: ......
Page 77: ......
Page 85: ......
Page 87: ......
Page 97: ......
Page 107: ......
Page 109: ......
Page 111: ......
Page 117: ......
Page 119: ......
Page 139: ......
Page 141: ......
Page 145: ......
Page 147: ......
Page 161: ......
Page 163: ......
Page 173: ......
Page 177: ......
Page 179: ......
Page 181: ......
Page 183: ......
Page 185: ......
Page 189: ......
Page 191: ......