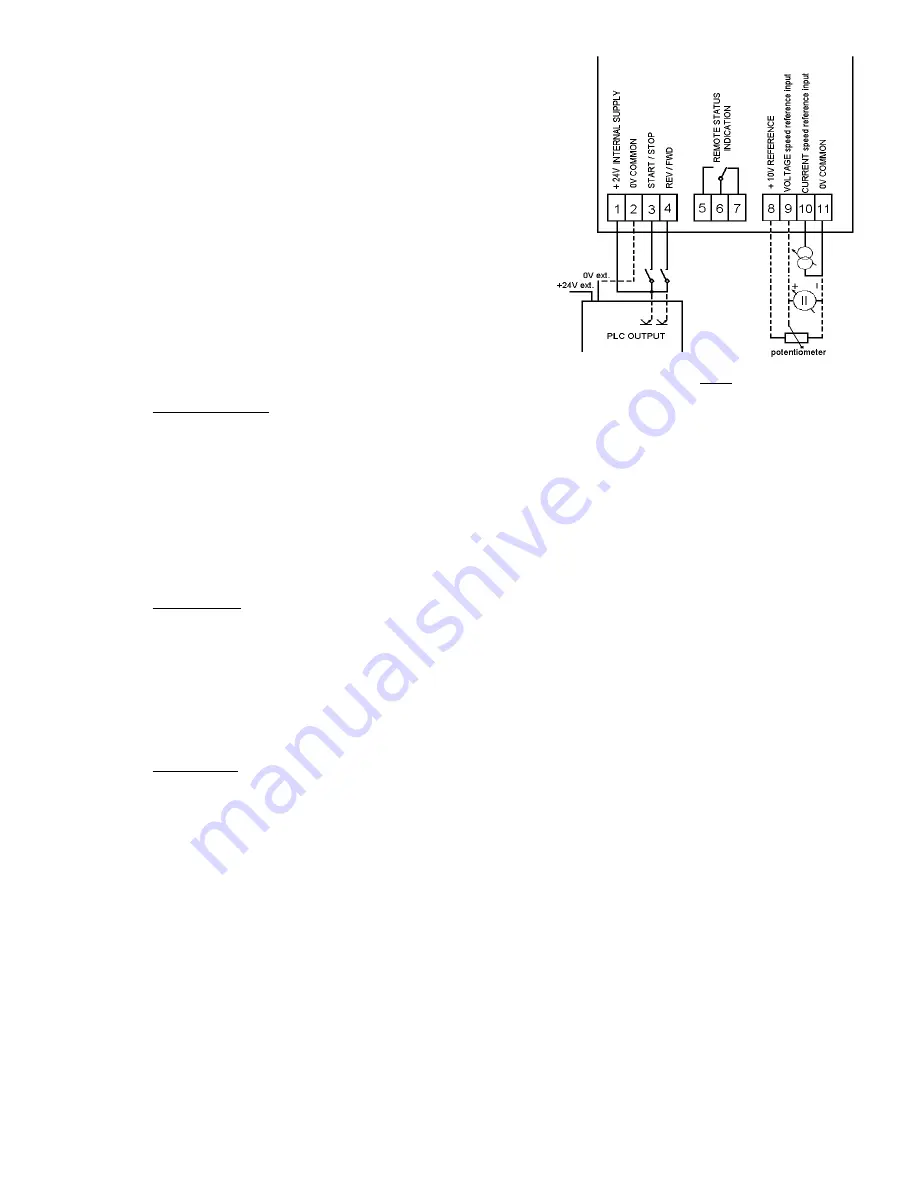
5
5.3. Control connections
5.3.1. Connection procedure
•
remove the front panel that is secured with screws.
•
for control connections use cable of 0,5 mm
2
screened
•
connection cable should enter at bottom.
•
connect screen to earth at the drive only .
•
connect control cable to terminals
(connections are shown in FIG 2).
•
refit the front panel
NOTE : always segregate control and power cabling !
5.3.2. Specifications of control inputs and outputs
Complete isolation between control and power electronic circuits.
•
Analogue inputs
- speed control
current input : 0
÷
20 mA (4
÷
20 mA)
120
Ω
input impedance
voltage input : 0
÷
10 V (2
÷
10 V)
67 k
Ω
input impedance
potentiometer : 2
÷
20 k
Ω
recommended value 10 k
Ω
•
Logic inputs
- run/stop : control switch or PLC output
- forward/reverse : control switch or PLC output
Input voltage : min : 15 V
DC
Input current : approx. 8,5 mA (24 V
DC
)
nominal : 24 V
DC
max : 30 V
DC
Input signal delay : max 5 ms
•
Logic output
- drive status : volt-free change-over relay contact - 250 V
AC
;
8 A
6. Drive status indication
6.1. On the front panel of the drive
•
LED "POWER" (red) : input voltage is present, all internal voltage levels are correct
•
LED "FAILURE" (red) : internal or external trip (e.g. overvoltage, overcurrent, short-circuit ...)
the drive is stopped (disconnected from the load)
6.2. Remote indication
•
Volt-free change-over relay contact
Control terminals :
5
- normally open
6
- common
7
- normally closed
Relay energised when : drive healthy
Relay de - energised when : power off or drive tripped (disconnected from the load)
FIG. 2