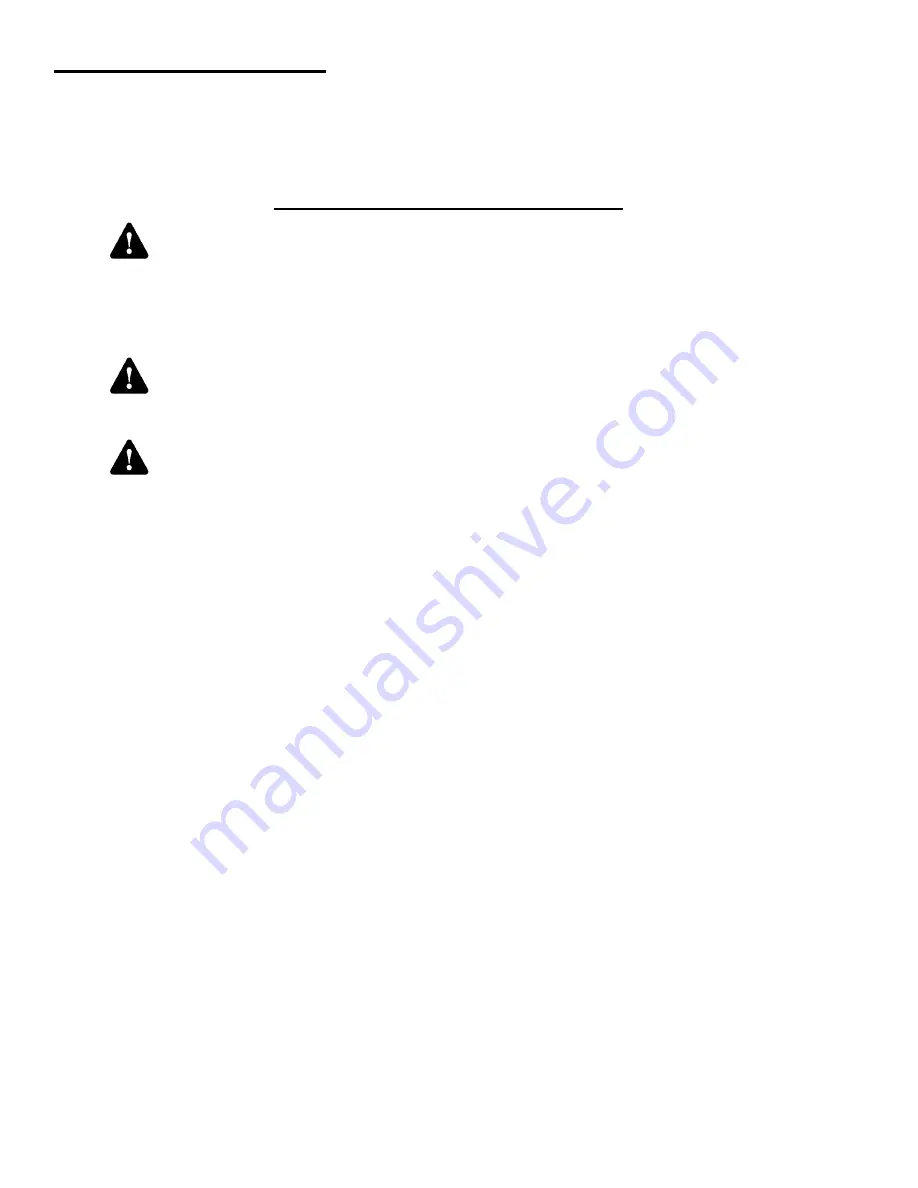
3
Important Safety Messages
Franklin Fueling Systems (FFS) equipment is designed to be installed with volatile hydrocarbon liquids such as gasoline.
Installing, servicing, or testing this equipment means working in an environment where these highly flammable liquids may
be present. Working in such a hazardous environment presents a risk of severe injury or death if these instructions and
standard industry practices are not followed. Read and follow all instructions thoroughly before installing or working on
this, or any other related, equipment.
Follow all applicable codes governing the installation and servicing of this product and the entire system.
Always lock out and tag electrical circuit breakers while installing or servicing this equipment and any
related equipment. A potentially lethal electrical shock hazard and the possibility of an explosion or fire from
a spark can result if the electrical circuit breakers are accidentally turned on during installation or servicing.
Please refer to the appropriate documentation for any other related equipment for complete installation and
safety information.
Follow all federal, state and local laws governing the installation of this product and its associated systems.
When no other regulations apply, follow NFPA codes 30A and 70 from the National Fire Protection
Association. Failure to follow these codes could result in severe injury, death, serious property damage
and/or environmental contamination.
Always secure the work area from moving vehicles. The equipment in this manual is usually mounted in
dispensers, so reduced visibility puts service personnel working on this equipment in danger from moving
vehicles entering the work area. To help eliminate these unsafe conditions, secure the area by using a
service truck to block access to the work environment, or by using any other reasonable means available to
ensure the safety of service personnel.
Warning
Warning
Warning
Summary of Contents for HEALY VP1000-220-IC
Page 15: ...15 Page intentionally blank ...
Page 16: ... 2012 FFS 405177002 Rev 3 ...