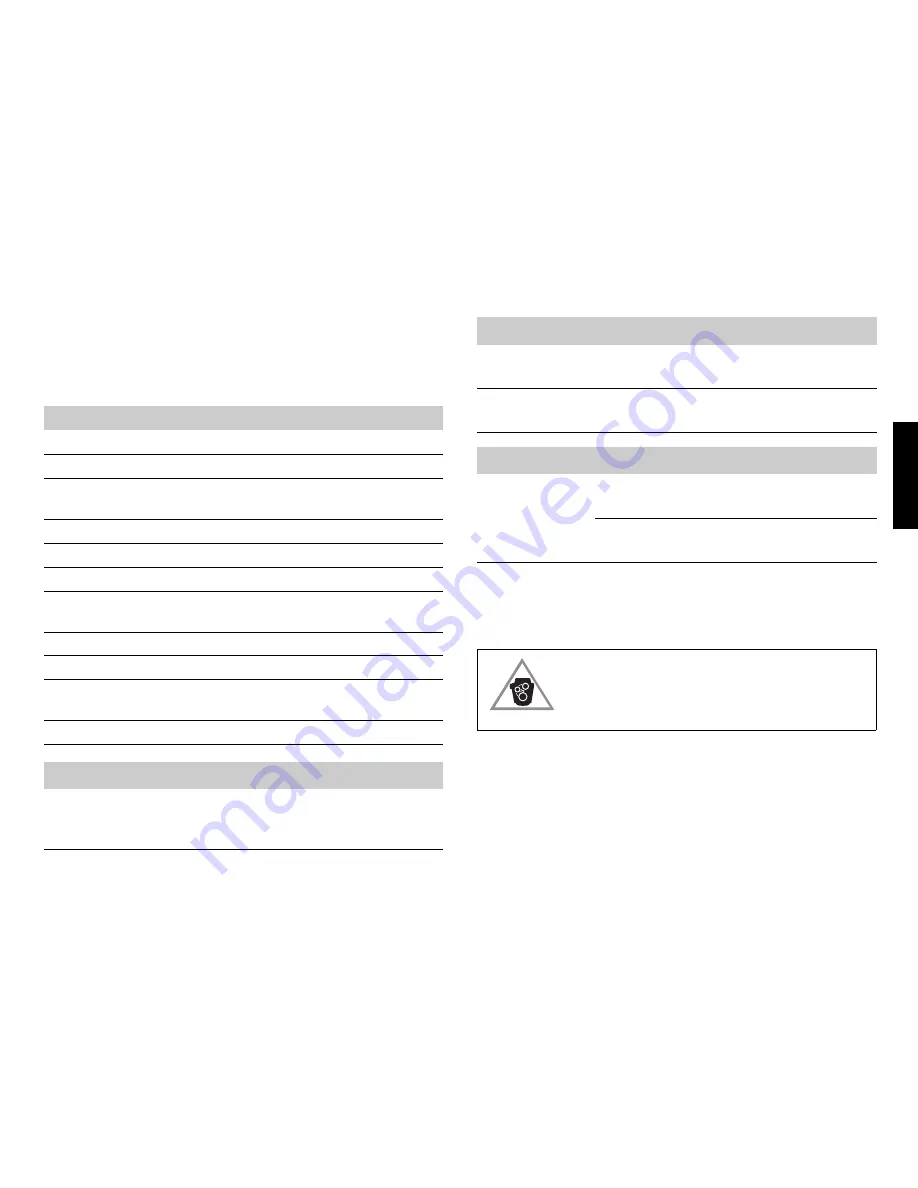
5
ENG
L
IS
H
ENGINE TECHNICAL DATA
The technical code and serial number are indicated on a plate, which
is located on different parts of the engine, according to the model:
flywheel casing, tappet cover, other.
(*)Net power to the flywheel in compliance with ISO 8528. Test
conditions: temperature 25 °C; atmospheric pressure 100 kPa;
relative humidity 30%.
Code
NF67TE8W.S550
Engine family
F4
Cycle
Diesel 4-stroke
Number and arrangement of
cylinders
6, in line
Bore x stroke
104 x 132 mm
Total displacement
6,728 cm
3
Air system
Turbocharged - with intercooler
Injection type
Direct - high pressure pump
supply and common rail system
Compression ratio
17.5 : 1
Cooling
Liquid
Engine direction of rotation
Anticlockwise
(seen from flywheel side)
Dry weight
~530 kg
Electrical system
24 V
Reccomanded Battery
capacity
- discharge current (EN 50342)
44 - 110 Ah
357 - 765 A
Electric starter motor
- Maximum output power
4 kW
Alternator
- Output
70 A
Performance (*)
F4HFA615A*D001
NF67TE8W.S550
50 Hz
Stand-by 236 kWm (net) @ 1500 rpm
Prime 215 kWm (net) @ 1500 rpm
60 Hz
Stand-by 255 kWm (net) @ 1800 rpm
Prime 231 kWm (net) @ 1800 rpm
Any alteration of the above mentioned characteristics
is strictly prohibited, penalty invalidation of the
guarantee and absence of all liability on the part of
FPT.
Electrical system
24 V