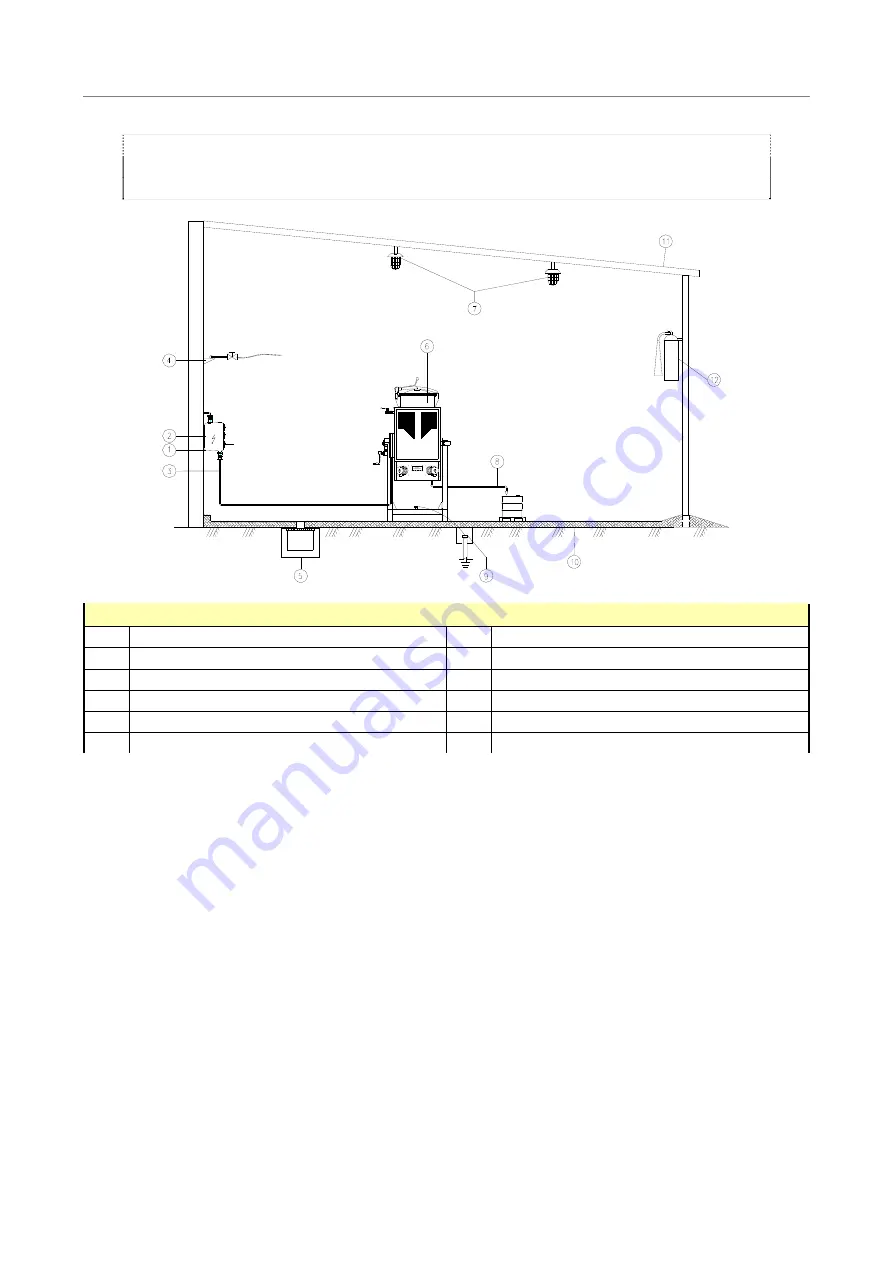
- 5 -
3.
INSTALLATION LOCATION
3.1.
Installation location
For the correct installation of the distillation unit it is necessary to classify the risk area, and as-
sure a proper ventilation and the use of certified electrical and non-electrical equipment ac-
cording to ATEX 95 (directive 94/9/EC)
LEGEND
1
Feed box
7
Lighting
2
Fuses or magnet switch
8
Distillate outlet
3
Feeding cable
9
Earth connection
4
Compressed air connection (for optionals)
10
Containment basement
5
Collection reservoir
11
Roof
6
Distillation unit
12
Fire extinguisher
It is necessary to install fire extinguishers (12), in correct places and in adequate number. The extinguishers must be for
fires of class B (fires of inflammable liquids) and class C (inflammable gas fires). Warning signs have to be installed
bringing attention to the possible dangers.
If the machine is installed outside, it has to be protected by a roof (13).
When treating flammable solvents, all electrical equipment present (lighting, sockets, etc.) have to be installed according
to the existing norms regarding the areas of explosion risk.
a.
Containment bund
The containment bund (10) for machines up to 120 litres can be formed by a metallic bund. For bigger ma-
chines the floor can be in cement with a small wall, to contain accidental spillage. The volume of the bund
should be at least 1.5 times the amount of solvent in the machine.
The basement should have a slight slope (1%) towards the collection reservoir (5).
b.
Collection reservoir
To collect accidental spills.
The collection reservoir should have a size to be able to install a pump to remove the accidentally spilled sol-
vent (e.g..: 500 x 500 x depth 600 mm).