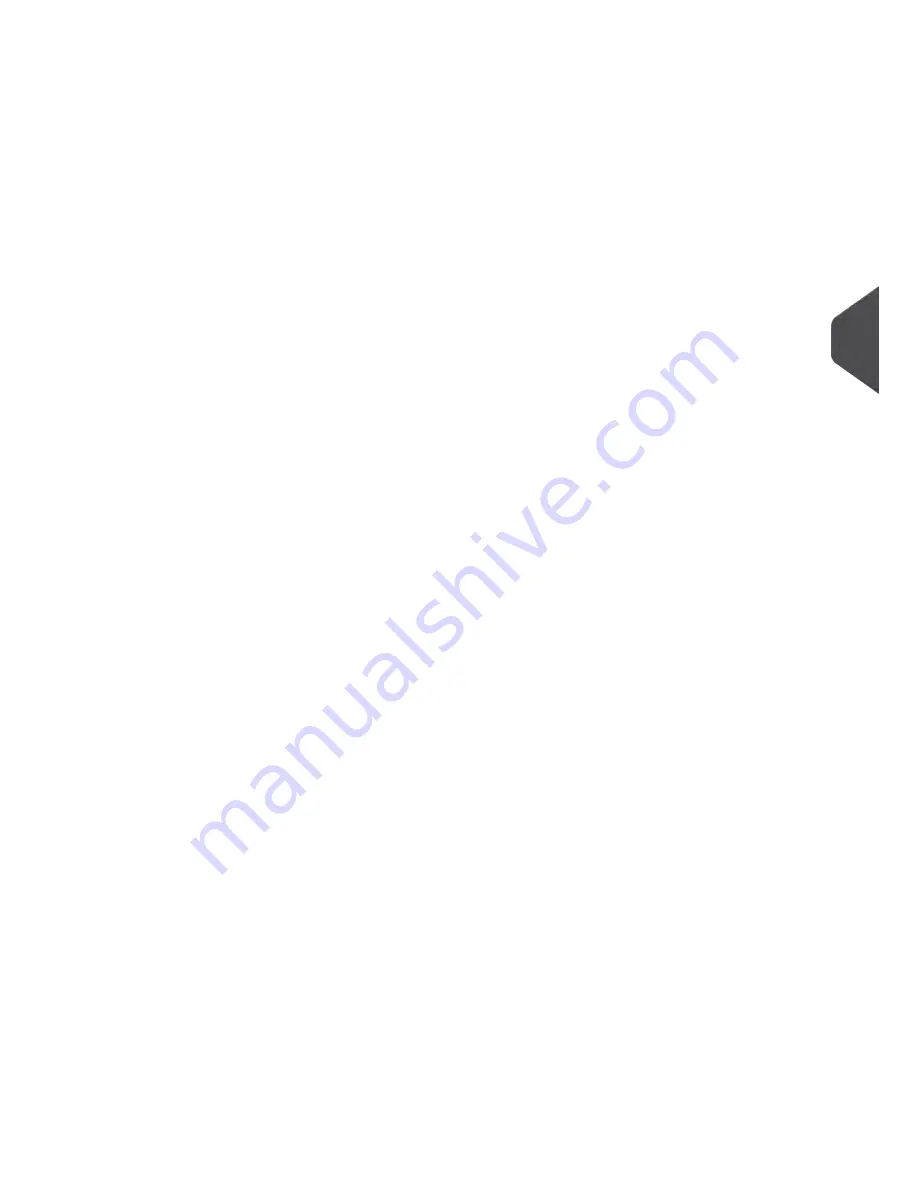
Second fold
• After leaving the fold rollers (35 and 36), the paper enters the second fold table. The flap (34) moves up.
Paper that enters the second fold table will be directed in upward direction.
• The paper guide (33) also moves up. This guide is necessary in the second fold table to retain the fold that
has been made in the first fold table.
• The paper is limited to a small area between the paper guide (33) and a fixed vertical guide plate (not shown
in the figure, but to the left of 33).
• At the appropriate time the flap (34) moves back and both the fold plate (32) and the guide plate (33) move
forward. This is the second fold.
• Directly after the fold has been made, the fold plate (32) returns to its rest position. The movement of the fold
plate (32), the paper guide (33) and the flap (34) is controlled by the second fold table clutch (CL7). The clutch
drives the curve gear (29). The axle for the curve gear also carries the brake disc (30). The slotted photocell
(SPH4) monitors the status of the curve gear.
• The 360 degrees fold cycle of the brake disk consists of a 120 degrees part (flap and paper guide upwards)
and a 240 degrees path (flap and paper guide downwards plus “karate” action of 32). The brake disc is
mechanically loaded by a positioning lever and a torsion spring. The hinge axle (31) also carries the lever for
the actuator of flap 34. In this way all movements related to the second fold table are synchronized.
Finally the paper leaves the fold unit on its way (transported by 27 plus 28 and 13 plus 14) to the insert table.
The timing of the fold plate movement is based on the detection of the paper by the folder entry photocell PH6, on
machine parameters and on operational fold parameters.
Envelope feeding
• All the rollers for this process stage (1, 4, 6, 8, 10 and 11) are engaged to the main drive by the envelope
track clutch (CL8). During the document and insert stage these rollers are disengaged.
• The envelope transport subsystem can be manually moved by the right-hand knob, at the left-hand side of
the machine.
• The counter rollers (3, 5, 7, 9 and 12) can be de-coupled from there driven counterparts by a counterclockwise
movement of the release handle at the left-hand side of the machine.
The envelope feeding process
• First of all by the action of the feed and separation rollers (1 and 2) an envelope is separated from the stack
in the hopper and transported via three pairs of transport rollers (3 - 8). The envelope track photocell (PH7)
detects the leading and trailing edge of the envelope.
• The envelope then passes the flap rollers (9 and 10).
• The combined action of the flap scraper and the lower linear speed of the flap rollers (9 to 12) compared with
the speed of rollers 3 to 8, results in some buckling and the opening of the envelope.
• The flap is the trailing part of the envelope passing the flap rollers and the envelope flap track photocell (PH8).
• Pulse measurements (measured via slotted photocell SPH1) during the presence of the envelope under the
photocells (PH7 and PH8) provide information on the length of the not yet opened envelope, the opened
envelope and the time at which the envelope transport is suddenly stopped with the envelope on the insert
table.
• The sudden stop is the result of disengaging by the envelope track clutch (CL8) and the friction brake (9a).
The envelope flap now is fixed between two rollers (11 and 12).
• In the final ejecting, sealing and exiting stage the driven rollers are engaged once again to release the envelope
(held between 11 and 12) and to feed a new envelope to the insert table.
3
063.1
Service
Guide
19
Summary of Contents for 6204 Series
Page 1: ...6204 Series Low Volume Inserter MAINTENANCE MANUAL 6 2012 ...
Page 3: ......
Page 7: ...4 1 063 1 Service Guide ...
Page 47: ...1 2 44 5 063 1 Service Guide ...
Page 48: ...3 4 5 063 1 Service Guide 45 ...