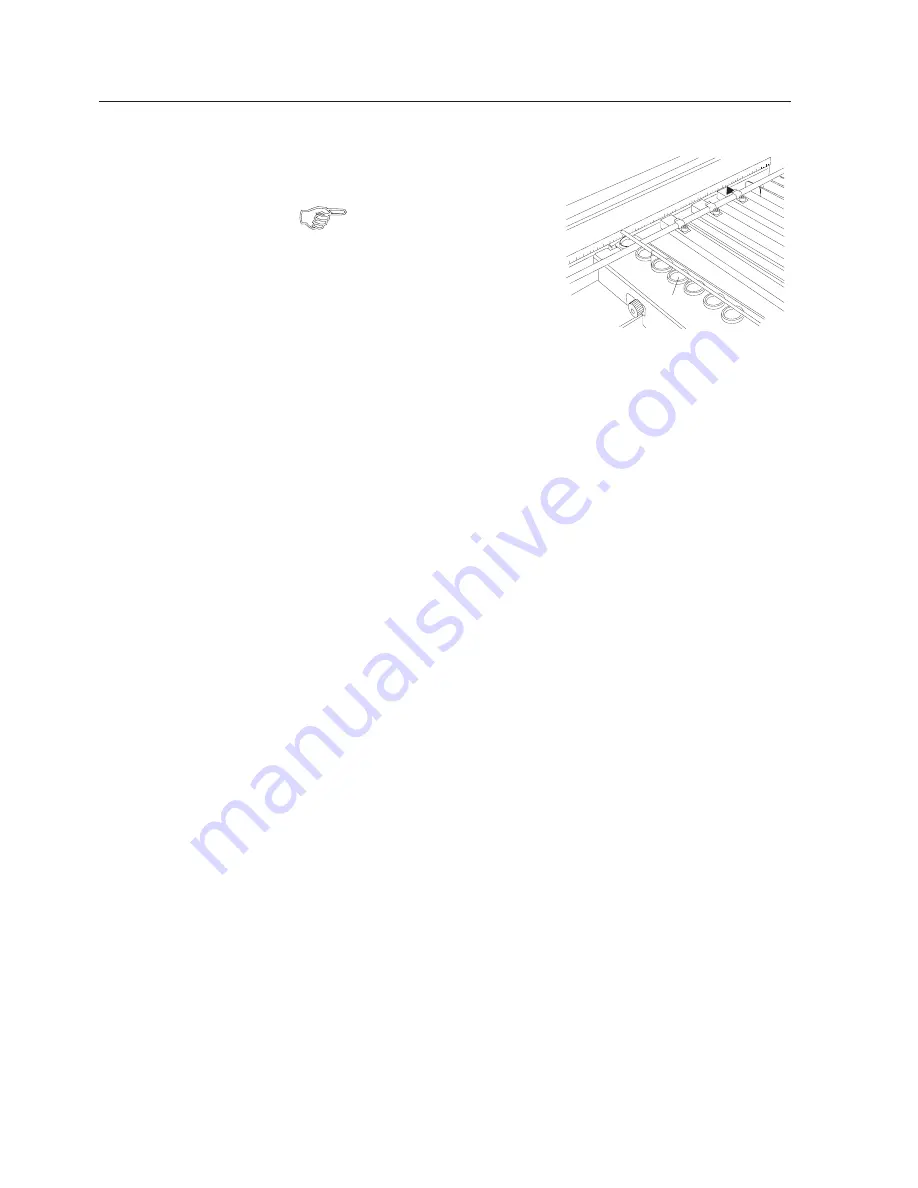
Operator's Manual
3950 Series RegisterTable
34
Type of Balls
The number and type of balls in the ball cage
(1) depend on format and type of paper.
1
Always try to use as few balls as
possible. Balls not needed for a
particular job should be removed
to avoid wear of the transport belt.
It is recommended to use the following balls:
Paper grades below 60 GSM:
Plastic balls
Paper grades from 60 - 150 GSM: Plastic balls, every 6th should be a steel ball
Paper grades above 150 GSM:
Mainly steel balls
In the infeed section (the first 4 to 6 balls) it is recommended to always use one
or two steel balls.
For very light paper grades every second ball opening should be left free.