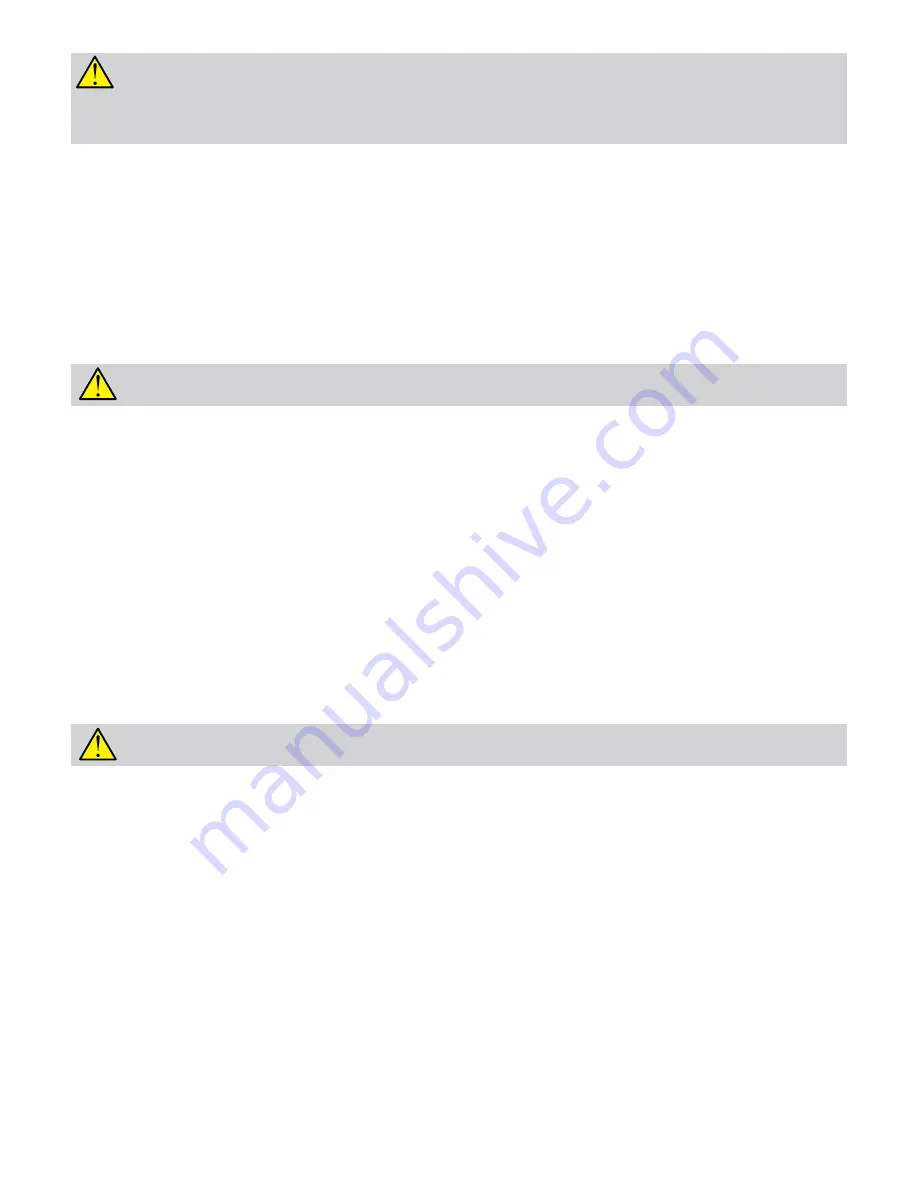
63
3.7.
Adaptation to other gas types and burner adjustment
This boiler is built to run on the type of gas specified on the order, which is shown on the packaging and on the boiler rating
plate.
Any later transformation is to be exclusively carried out by qualified personnel, using manufacturer designed accessories and
following the procedure and adjustment instructions for an accurate boiler setting-up.
3.7.1.
Switching from NATuRAL GAS to PRoPANe
- Disconnect the boiler from the electric power supply.
- Remove boiler outer front panel;
- Loosen the three screws securing combustion chamber front panel to frame, then remove panel.
- Loosen the screw securing intake pipe to mixer, and remove air-intake pipe (fig. 33).
- Disconnect gas pipe from mixer (fig. 33).
- Loosen the three socket head screws, and remove the mixer (fig. 34).
- Loosen the two retaining screws, and slide out mixer plastic body (fig. 35).
- Using a 6 mm Allen wrench, loosen the two mixer nozzles (fig. 35).
- Screw the new nozzles for propane listed in table 22, taking care to drive them fully home, without tightening.
- Only for model KC 32, install 7.2 mm diaphragm on the gas valve outlet.
In case the nozzle idles when reaching the bottom of the nozzle threaded seat, it means that the thread is damaged and perfect
sealing is not ensured. The whole mixer shall be replaced.
- To refit the plastic body (Venturi), insert it inside mixer and secure it in place with the retaining screws. Take care not to damage the o-rings
assembled on plastic body ends (fig. 35) and to respect the assembling direction (fig. 36).
- Refit the reassembled mixer onto the fan with the socket head screws, making sure to insert the O-ring between mixer and fan (fig. 35).
- Reconnect boiler to electric power supply, and open the gas cock.
- Access the programming page to set the parameters P4-P5-P6-P7 to the propane gas values, as described in tab. 15.
- Adjust the gas valve (see next paragraph, 3.7.3.).
3.7.2.
Switching from PRoPANe to NATuRAL GAS
- Disconnect the boiler from the electric power supply.
- Remove boiler outer front panel;
- Loosen the three screws securing combustion chamber front panel to frame, then remove panel.
- Loosen the screw securing intake pipe to mixer, and remove pipe (fig. 33).
- Disconnect gas pipe from mixer (fig. 33).
- Loosen the three socket head screws, and remove the mixer (fig. 34).
- Loosen the two retaining screws, and slide out mixer plastic body (fig. 34.
- Using a 6 mm Allen wrench, loosen the two mixer nozzles (fig. 35).
- Screw the new nozzles for propane listed in table 22, taking care to drive them fully home, without tightening.
- Only for model KC 32, remove 7.2 mm diaphragm on the gas valve outlet.
In case the nozzle idles when reaching the bottom of the nozzle threaded seat, it means that the thread is damaged and perfect
sealing is not ensured. The whole mixer shall be replaced.
- To refit the plastic body (Venturi), insert it inside mixer and secure it in place with the retaining screws. Take care not to damage the o-rings
assembled on plastic body ends (fig. 35) and to respect the assembling direction (fig. 36).
- Refit the reassembled mixer onto the fan with the socket head screws, making sure to insert the O-ring between mixer and fan (fig. 35).
- Reconnect boiler to electric power supply, and open the gas cock.
- Access the programming page to set the parameters P4-P5-P6-P7 to the propane gas values, as described in tab. 15.
- Adjust the gas valve (see next paragraph, 3.7.3.).
Summary of Contents for ITACA KC 12
Page 71: ...71...