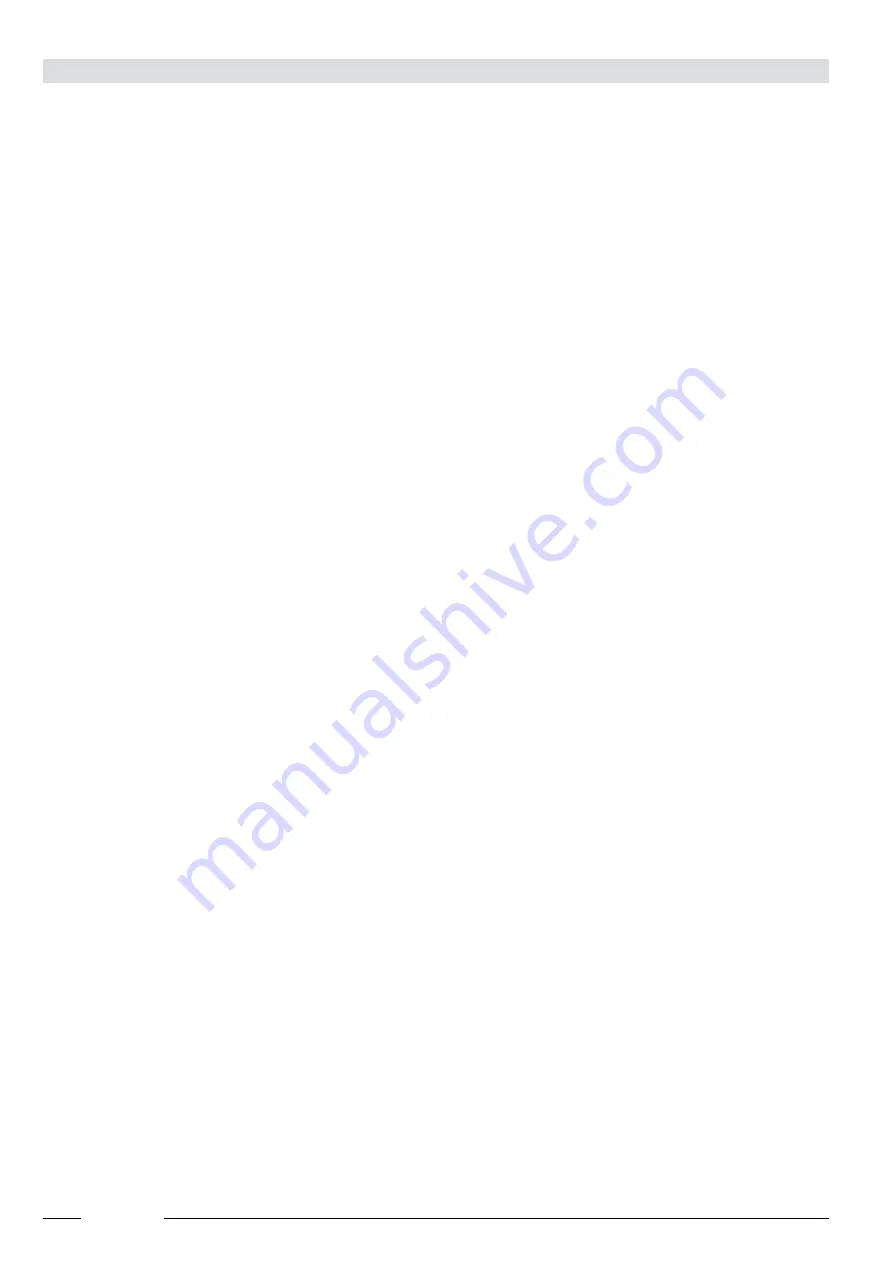
14
3. TECHNICAL CHARACTERISTICS AND SIZES
3.1 Technical features
Gazelle EVO
is a gas convective stove with sealed chamber, forced draught and premixing, available in the following versions:
Gazelle EVO 3000
from 2.72 kW of useful heat output
Gazelle EVO 5000
from 4.52 kW of useful heat output
Gazelle EVO 7000
from 5.88 kW of useful heat output
The gas convective stove Gazelle EVO satisfies the essential requirements under:
• Regulation (EU) 2016/426 of 9 March 2016;
• EMC Directive 2014/30/EU of 26 February 2014;
• Low Voltage Directive 2014/35/EU of 26 February 2014;
• ERP Directive 2009/125/EC of 21 October 2009;
• Labelling Directive 2010/30/EU of 19 May 2010;
and is equipped with all the safety features required by the prevailing regulations on these products, namely:
Safety electronic equipment
with ionisation flame detection device. With no flame, this system inhibits equipment operation thereby
preventing gas leakage.
Differential air pressure switch
that stops equipment operation if vent or intake pipes are clogged or in case of intake fan malfunc-
tion.
Gas valve with double solenoid valve
in class B+J.
Safety thermostats
in air (all models) and on the exchanger (models 5000 and 7000 only), that can stop equipment operation in case
of faulty temperature increase.
Temperature probe
on the exchanger that can stop equipment operation in case of faulty temperature increase.
The key characteristics of the gas convective stove Gazelle EVO include:
•
Seasonal energy efficiency class A
•
High-efficiency die-cast aluminium fin-type heat exchanger.
• Dual channel heat recuperator in die-cast aluminium.
• Separate and extendable intake and vent pipes.
•
Centrifugal combustion fan with high-efficiency brushless motor.
•
Tangential convection fan with high-efficiency brushless motor.
• Electronic ignition.
•
Ionisation flame control.
• Microprocessor-based electronic equipment for safety, adjustment and control.
• User interface with adjustment knob (encoder), four keys and large backlit LCD.
• Safety air pressure switch.
• Safety thermostat (2 on models 5000 and 7000).
• Ambient temperature probe.
• Temperature probe on exchanger body (models 5000 and 7000).
• Gas valve with constant air/gas ratio.
• Ambient temperature selector with antifreeze function.
•
Built-in humidifier.
• Weekly programming.