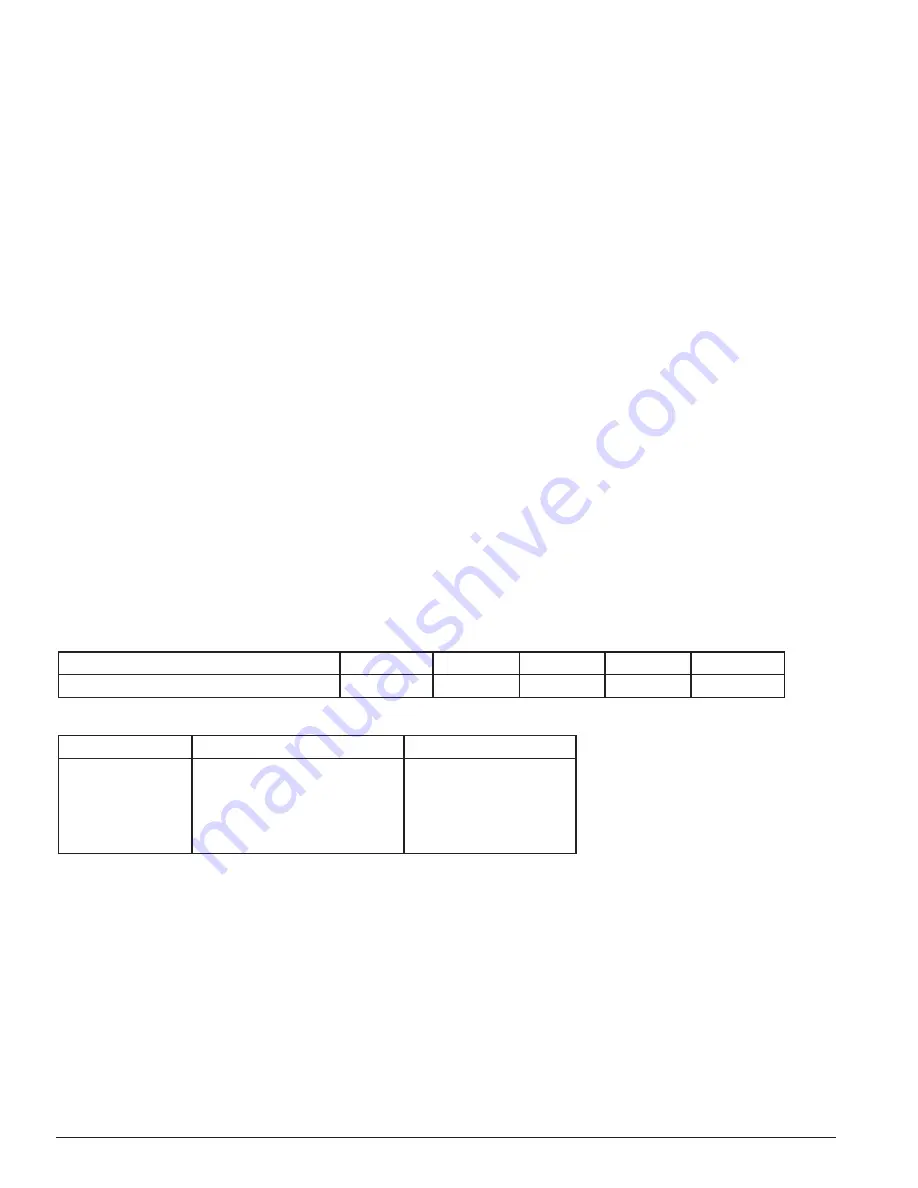
26
Horizon HCD700R/N, HMD700R/N Ice Machines
Refrigeration system
Condenser unit operation
The condensing unit is weatherproof and equipped to operate in ambient temperatures from –2 0 F to 120 F
(–29 C to 48.9 C). The condensing unit is controlled by a low pressure control, which works in concert with a
refrigerant solenoid valve on the evaporator module. On start-up, the refrigerant solenoid valve opens and suction
pressure rises above the “on” set point of the control. The compressor and fan turn on and the refrigeration system
operates. Upon shut down, the refrigerant solenoid closes. The compressor will pump down the ice machine
evaporator and suction line until the low “off” set point is reached, at which point the compressor and fan will turn off.
Low ambient operation: Reliable operation at low outdoor ambient temperature is achieved with a pumpdown cycle,
a crankcase heater and a head pressure control valve. When the outdoor ambient falls, the condensing pressure
falls. This causes the discharge pressure to fall as well. When the discharge pressure falls below the dome pressure,
the valve modulates open to the discharge port which allows discharge gas to bypass the condenser. Mixing the
discharge gas with the liquid creates a high pressure at the condenser outlet, reducing the flow and causing liquid
to back up in the condenser. Flooding the condenser reduces the area available for condensing. This reduction in
effective condenser surface area results in a rise in condensing pressure. During summer conditions, the discharge
pressure is high, thus closing the discharge port of the valve. Hence, there is full liquid flow from the condenser to the
receiver.
A check valve is installed in the liquid line between the receiver and the condenser to prevent liquid migration from
the receiver to the condenser during the off cycle. The low pressure control will start the condensing unit anytime the
low side pressure rises above the set point and pump the refrigerant out until the pressure falls to the set point. The
crankcase heater, which is energized whenever the condensing unit has power, keeps the compressor oil warmer
than the coldest location in the system. This minimizes off cycle refrigerant migration. If power to the condensing unit
is interrupted after the system is charged, the compressor should not be started unless the crankcase heater has
been energized for at least 24 hours immediately prior to compressor startup. However the compressor can safely be
started during the refrigeration system charging process (without the warm-up period) once sufficient refrigerant is in
the system to maintain a positive pressure on the suction side of the compressor.
Under normal ambient operating conditions the left side condenser fan motor, when viewing the outdoor condensing
unit from the compressor side, is not energized; therefore, the fan will pinwheel. During hot summer days, at elevated
temperatures, the left side condenser fan will be energized to maintain the BTU efficiency of the condensing unit.
For additional information, please reference Horizon ice machine installation instructions for remote condensing units.
Refrigerant pressure data
Air-cooled condensers (air)
60 F/16 C
70 F/21 C
80 F/27 C
90 F/32 C
100 F/38 C
Pressure (psig) discharge/suction
170/27
190/29
211/31
232/34
245/36
R404A ice machine refrigeraant charge specifications
Model
Line Run
Charge
700
0 – 50 ft (0 – 15.2m)
50 – 75 ft (15.2 – 22.9m)
75 – 100 ft (22.9 – 30.5m)
100 ft+ (30.5m+)
8 lbs (3.6kg)
9 lbs (4.1kg)
10 lbs (4.5kg)
Consult factory