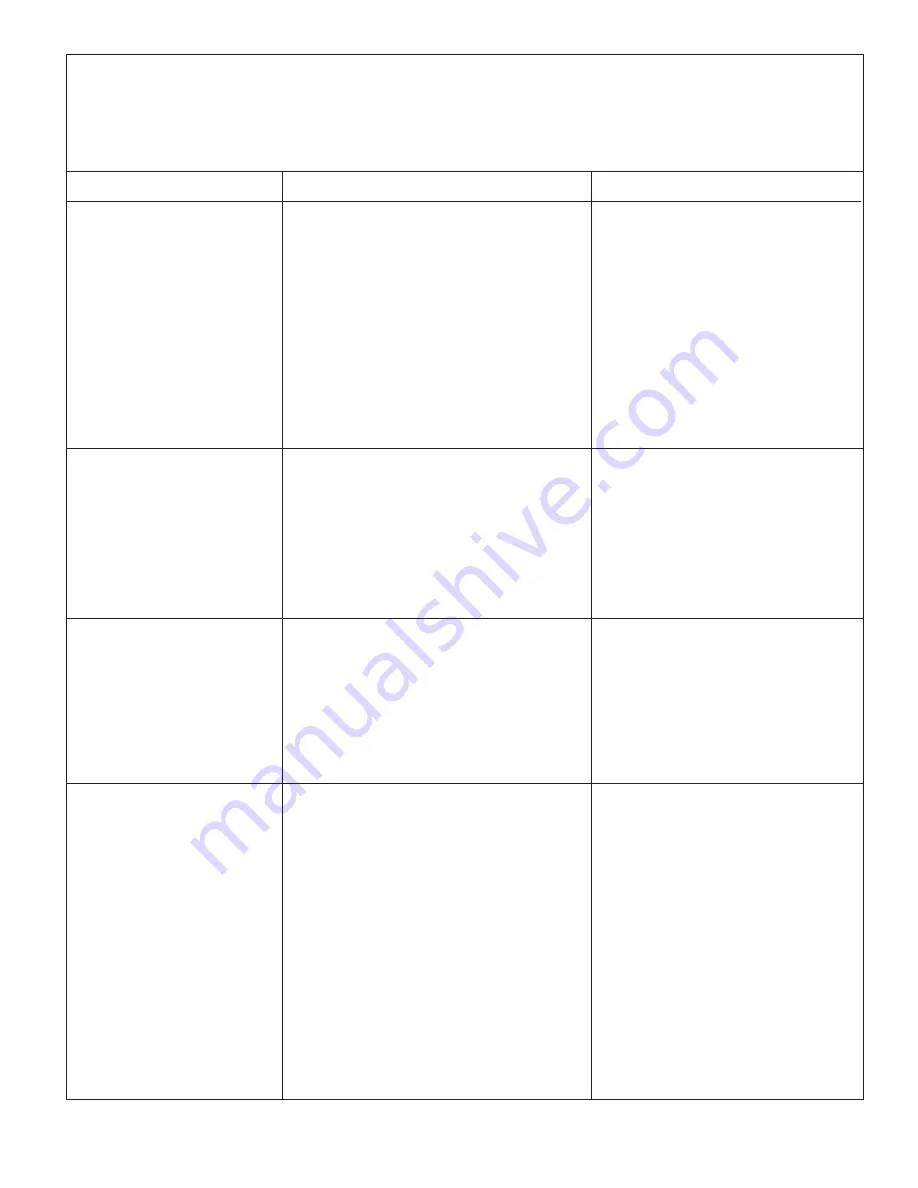
Problem
1. Icemaker will not run.
System status:
compressor, gearmotor,
and fan motor inoperative.
2. Compressor will not run.
System status: gearmotor
and fan motor run.
3. Unit cycles intermittently.
System status:
compressor, gearmotor,
and fan motor cycle.
4. Low ice production.
Poor quality ice.
Indicators/possible cause
1. No power to unit.
2. Open bin level control.
3. Water OK LED (WTR) not on.
4. 20M or 2ND LED is on indicating that first
or second torque error has occurred.
5. Gearmotor locked up (immediate torque
error indicated by LEDs when board is
reset).
6. Centrifugal switch stuck in open or closed
position (immediate torque error indicated
by LEDs when board is reset).
1. Condenser coil plugged causing
overheating.
2. Defective starting capacitor.
3. Defective starting relay.
4. Open motor winding.
5. No power output from compressor output
terminal on control board.
1. Hi temp cut out open (W/C units only)
due to high head pressure.
2. Float reservoir running dry, sensing
probe signalling for system to shut down.
1. Dirty condenser coil.
2. Restricted air flow to condenser coil.
3. Mineral coated evaporator.
4. High ambient water supply and/or air
temperature.
5. Improper exhaust air provisions.
6. Faulty expansion valve.
7. Low refrigerant charge.
8. Superheat incorrect.
9. Inefficient compressor.
Corrective action
1. Check that unit is plugged in, circuit
breakers are on.
2. Adjust or replace ice level control.
3. Check reservoir for water, restore
water to unit.
4. See Problem #6 below.
5. Repair or replace gearmotor.
6. Replace centrifugal switch.
1. Clean condenser coil and replace
overload if necessary.
2. Replace start capacitor.
3. Replace relay.
4. Ohm out windings and replace
compressor if necessary.
5. Check terminal connection and
replace control board if necessary.
1a. Check supply and temperature of
water to condenser.
1b. Check discharge pressure and
adjust water regulating valve.
1c. Clean condenser coil.
2. Check water supply to float and
float operation. Part #207588 will
have flashing WTR LED.
1. Clean condenser.
2. Remove obstruction.
3. Clean evaporator.
4. Precool water and/or install air duct
per Follett installation manual.
5. Provide proper exhaust air
provisions per Follett installation
manual.
6. Replace expansion valve.
7. Check for leaks; repair, evacuate,
and weigh in correct charge.
8. Check that TEV sensing bulb is
securely clamped in place and not
damaged; check that insulated bulb
cover is in place.
9. Replace compressor.
Troubleshooting chart
• Flashing water LED at any time indicates that water signal to board has been lost for more than one second.
• Ten-second delay: There is a 10 second delay in reaction to loss of water (WTR) or bin (B-E) signals. If signals
are not lost for more than 10 seconds, no reaction will occur.
13