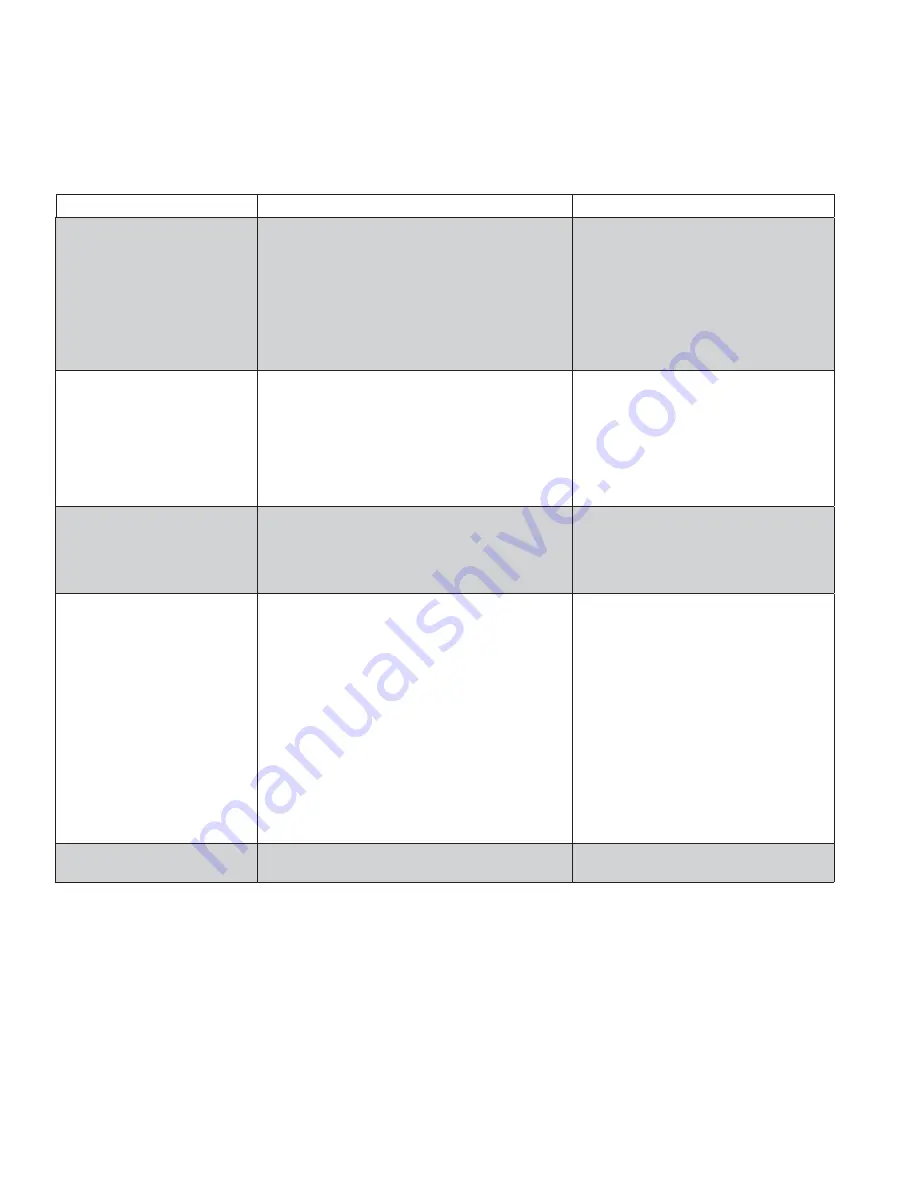
32
Troubleshooting chart
Flashing water LED at any time indicates that water signal to board had been lost for more than one second.
Ten-second delay: There is a 10 second delay in reaction to loss of water (WTR) or bin (B-E) signals. If signals are not lost for
more than 10 seconds, no reaction will occur.
Problem
Indicators/possible cause
Corrective action
1. Ice machine will not run.
System status compressor,
gearmotor, and fan motor
inoperative.
1. No power to unit.
2. Open bin level control.
3. Water OK LED (WTR) not on.
4. 20M or 2ND LED is on indicating that fi rst or
second torque error has occurred.
5. Gearmotor locked up (immediate torque error
indicated by LEDs when board is reset).
6. Open coil on gearmotor start relay causing an
immediate torque error.
1. Check that unit is plugged in, circuit
breakers are on.
2. Adjust or replace ice level control.
3. Check reservoir for water, restore
water to unit.
4. See Problem #6.
5. Repair or replace gear motor.
6. Replace gearmotor start relay.
2. Compressor will not run.
System status: gearmotor
and fan motor run.
1. Condenser coil plugged causing open
overload or high pressure cut-out.
2. Defective starting capacitor.
3. Defective starting relay.
4. Open motor winding.
5. No power output from compressor output
terminal on control board.
1. Clean condenser coil and replace
overload if necessary.
2. Replace start capacitor.
3. Replace
relay.
4. Check Ohm on windings and replace
compressor if necessary.
5. Check terminal connection and
replace control board if necessary.
3. Unit cycles intermittently.
System status: compressor,
gear motor, and fan motor
cycle.
1. Float reservoir running dry, sensing probe
signalling for system to shut down.
1. Check water supply to fl oat and fl oat
operation. PC board will have fl ashing
WTR LED.
4. Low ice production.
Poor quality ice.
1. Dirty condenser coil.
2. Restricted air fl ow to condenser coil.
3. Mineral coated evaporator.
4. High ambient water supply and/or air
temperature.
5. Improper exhaust air provisions.
6. Faulty expansion valve.
7. Low refrigerant charge.
8. Superheat
incorrect.
9. Inefficient
compressor.
1. Clean
condenser.
2. Remove
obstruction.
3. Clean
evaporator.
4. Precool water and/or install air duct
per Follett installation manual.
5. Provide proper exhaust air provisions
per Follett installation manual.
6. Replace expansion valve.
7. Check for leaks; repair, evacuate, and
weigh in correct charge.
8. Check that TEV sensing bulb is
securely clamped in place and not
damaged; check that insulated bulb
cover is in place.
9. Replace
compressor.
5. Water leaks from bottom of
evaporator.
1. O ring seal broken.
1. Replace O ring.