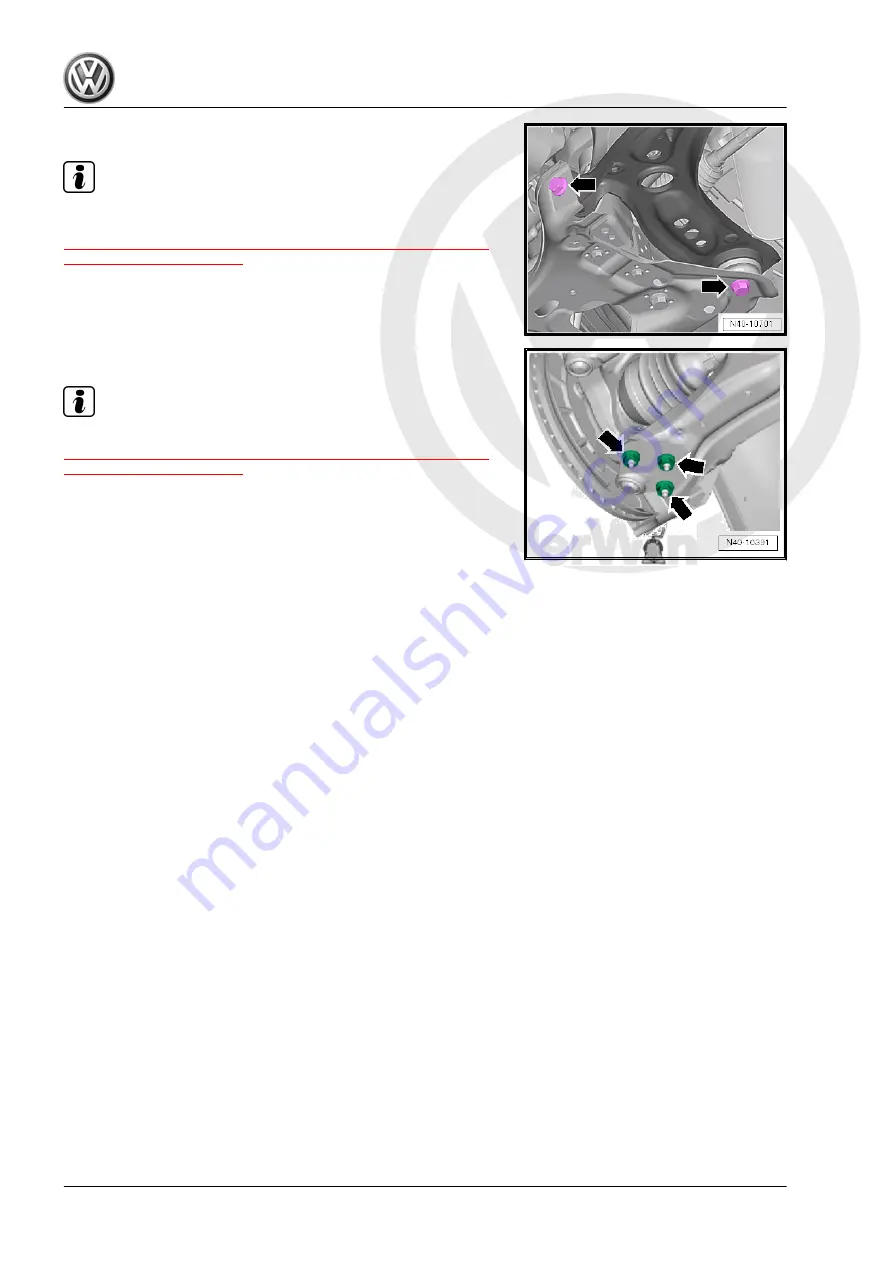
Pro
te
c
t
ed
b
y
co
p
y
rig
h
t.
C
o
p
y
in
g
fo
r
pr
iv
a
t
e
o
m
m
e
r
c
ia
l
p
u
rp
o
s
e
s
,
i
n
p
a
rt
o
r i
n
w
h
o
le
n
o
t
p
e
r
m
it
t
e
d
u
n
l
e
s
s
a
ut
ho
r
i
s
ed
b
y
V
olk
sw
a
ge
n AG
.
V
olk
s
w
a
g
en
AG do
es
n
ot g
uar
ante
e
or a
c
c
ep
t
a
ny
li
a
b
i
li
t
y
w
ith
r
e
s
p
e
c
t
t
o
th
e
c
o
rr
e
c
t
n
e
s
s
o
f
in
fo
r
m
a
tio
n
in
th
is
d
o
c
um
en
t.
C
o
py
rig
ht b
y
V
olk
sw
a
ge
n
A
G.
– Tighten the screws -arrows-.
Note
Tighten the bolts -arrows- and nuts in curb weight position. Refer
to
⇒ “3.8.1 Wheel Bearing in Curb Weight, Lifting Vehicles with Coil
.
– Tighten nuts -arrows-.
Note
Tighten the nuts -arrows- in curb weight position. Refer to
⇒ “3.8.1 Wheel Bearing in Curb Weight, Lifting Vehicles with Coil
.
– Remove the -T10533- .
– Remove the exhaust system double clamp. Refer to ⇒ Rep.
Gr. 26 ; Exhaust Pipes/Mufflers; Exhaust Pipes/Mufflers, Sep‐
arating .
– Install the pendulum support. Refer to ⇒ Rep. Gr. 10 ; Sub‐
frame Mount; Pendulum Support, Removing and Installing .
Golf 2015 ➤ , Golf Variant 2015 ➤
Suspension, Wheels, Steering - Edition 03.2016
60
Rep. Gr.40 - Front Suspension