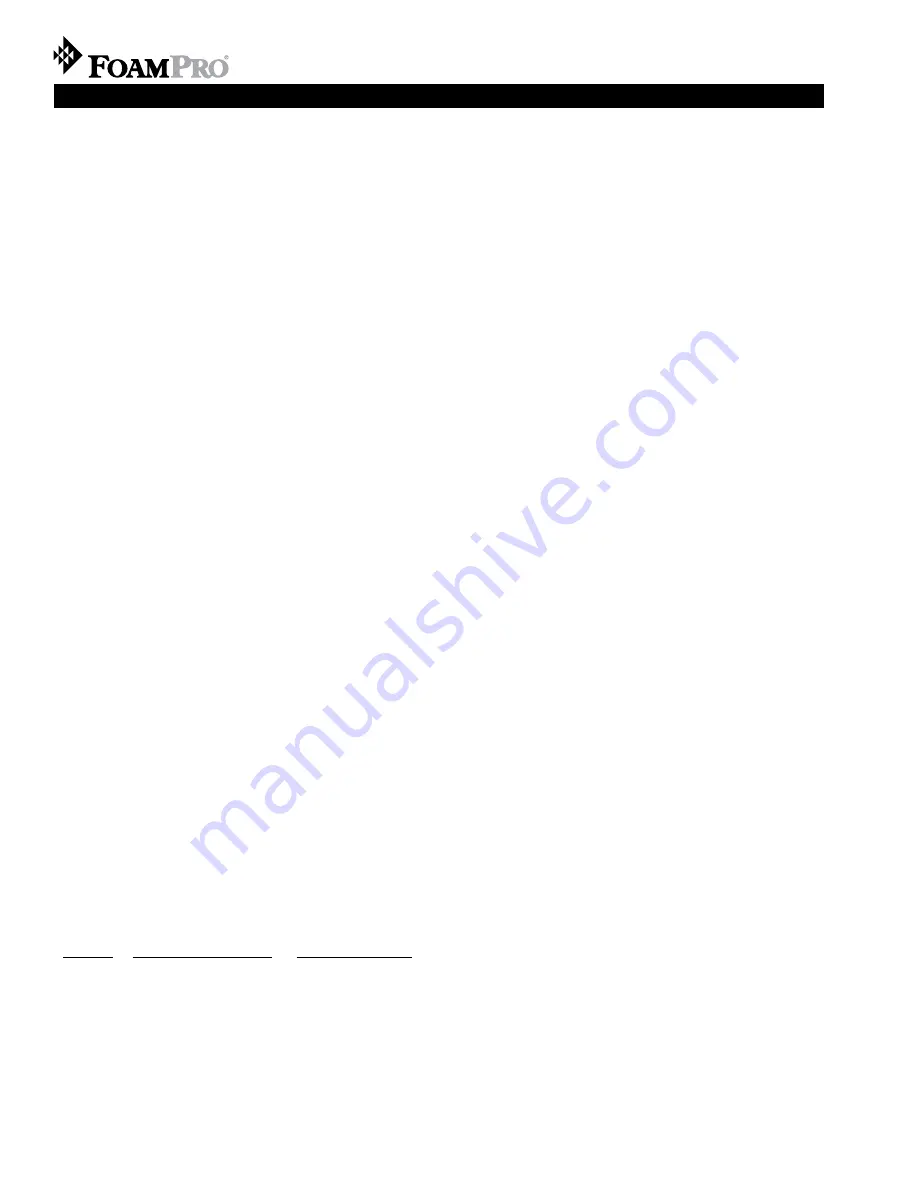
6
Installation and Operation Manual
4
Installer Supplied Parts
The FoamPro High Pressure System is provided with
the major components and accessories required for
installation. Due to differences in chassis and apparatus
configurations, the installer must provide plumbing
to satisfy individual installation requirements. The
following paragraphs list the specifications for selection
of these components. Before beginning system
installation, read this section thoroughly to make sure
the proper components are selected. For detailed
system installation instructions, refer to Sections 5, 6,
and 7.
SUCTION LINES
Corrosion-resistant fittings and hoses from the foam
tank to the foam concentrate inlet of the pump must be
used. Use 5/16-inch to 3/8-inch inside diameter hose
for the foam inlet. Corrosion-resistant fittings and hoses
from the water source to the inlet of the pump must
be used. Use only 3/4-inch minimum inside diameter
hose for the water inlet. Use components that are
rated for 23 in [584.2 mm] Hg vacuum and 50 psi [3
bar] pressure or greater for all suction line inlets. The
components used must be compatible with all foam
concentrates to be used. All fittings used must be
made of brass, 300 series stainless or other corrosion-
resistant materials. Before selection of components,
check for compatibility with foam concentrate. The use
of clear suction hose is recommended to allow viewing
of foam and water priming operations.
DISCHARGE LINES
Fittings and hoses from the foam solution discharge of
the pump to the foam spray nozzle must be supplied by
the installer. Hoses and fittings of 1/2-inch [12.7 mm]
minimum INSIDE diameter, rated for 1800 psi [124.1
BAR] minimum working pressure, must be supplied by
the installer. Fittings are required to be 1/2-inch male
NPT on hose ends.
The following guidelines should be followed in choosing
hose length and hose diameters.
Hose ID
Approximate Pressure
Drop Per 1 ft. of Hose
Recommended
Max. Hose Length
1/2”
1.15
50’
5/8”
.47
100’
3/4”
.23
200’
1”
.07
400’
Fittings and hoses must be compatible with all foam
concentrates to be used. Use fittings of brass, 300
series stainless or other corrosion-resistant material
that is compatible with foam concentrates to be used.
Thermal relief valve must be plumbed to discharge
away from operator.
CHECK VALVES
Check valves have been included with the system
at the water inlet to help prevent back flow of foam
concentrate or foam solution. The system should be
disconnected from exterior water supplies when not
in use. A complete system flush should be performed
before storage to prevent component failure due to
evaporation of foam and water within the system.
FOAM CONCENTRATE TANK
A foam concentrate tank must be supplied to suit the
capacity required for the apparatus application. The
tank should meet NFPA minimum standards for the
design capacity, including filler size, venting and drain
facility. A shut-off valve is recommended to allow
cleaning of the strainer.
ELECTRICAL REQUIREMENTS
Electrical wiring must be supplied to the engine starter
switch. Use AWG No. 4 cable for power and ground
connection, not to exceed 5 ft. SEE ENGINE MANUAL
for detailed electrical hook-up specifications.
CAUTION: Always disconnect ground before electrical
arc welding on any FoamPro equipment. Failure to do so
will result in a power surge through the system that could
case irreparable damage to the electronic components.
HYDRAULIC REQUIREMENTS
FoamPro hydraulic-drive Turbo Stream systems
are provided with only the hydraulic motor. All
other components and accessories required for
installation must be provided by the installer due to
differences in chassis and apparatus configurations.
The installer must provide hydraulic pump, controls,
hoses, reservoir, fittings, filters, strainers, cooler and
appropriate oil to satisfy installation requirements.
Before beginning system installation, read this manual
thoroughly to make sure the proper components are
selected. It is the installer’s responsibility to choose
the proper type of hydraulic system, i.e. positive
displacement or load sense to drive the Turbo Stream
at the proper RPM.
CAUTION: All DOT, SAE or other applicable standards
must be followed when installing the hydraulic system.
Pay close attention to engine and transmission
manufacturer’s drive limitations.