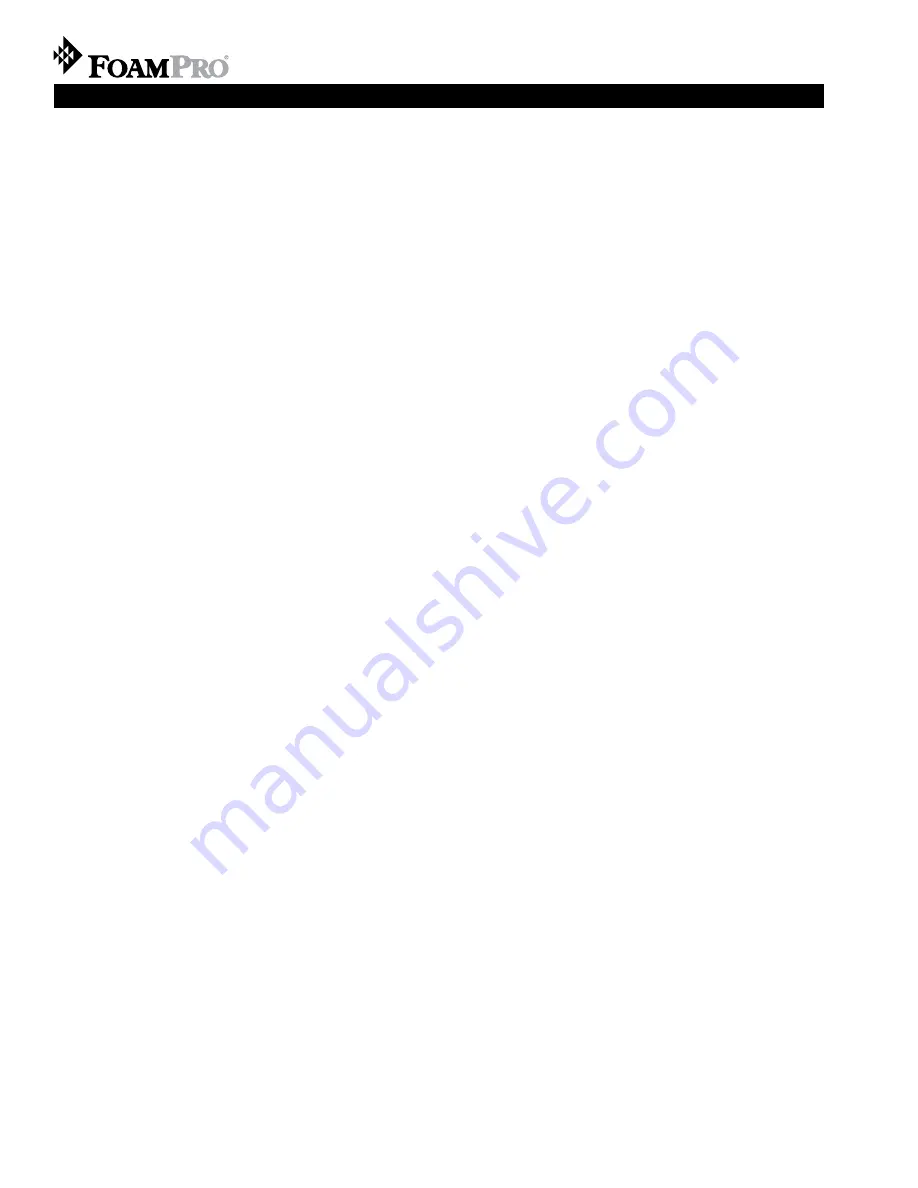
10
Installation and Operation Manual
10
Calibration & Setup
CALIBRATION
The FoamPro High Pressure System has been
calibrated at the factory. To check calibration of the
system, the following procedure should be used:
1) Start the system. Run the engine to an RPM that
produces 8 GPM (3345 Engine RPM) of pump water
inlet flow. Tools needed for the test are a pilot tube
or other calibrated flowmeter to test the system
inlet water flow, a graduated bucket to remove and
calibrate foam concentrate, and a stop watch to
measure volume unit/time of foam concentrate and
water flow.
2) Open the control knob of the display panel to start
foam injection, while holding the spray gun in the
on position, run the system for a few minutes. The
system will not inject foam concentrate while the
system is unloading.
3) Turn the injection control knob to the desired foam
injection calibration point. Start the stop watch and
record the necessary volumes or flow rates of foam
concentrate and water.
4) Measure the amount of foam concentrate in the
container and compare that to the calculated
amount. (Main flow rate X injection rate X minutes
flowed [8.00 GPM X 0.005 (0.5%) injection rate X
5 minutes = 0.20 gallons]).
5) CAUTION: Long periods of pump deadheading
may result in pump damage due to overheating of
water in the system. The system is equipped with a
thermal relief valve to eliminate damage to the pump
during unloading. It is recommended to idle down
the system during unloading if the system must stay
running during transportation.
6) CAUTION: System may only be calibrated with
foams with a viscosity from 60 CPS. Use of
other higher viscosity foams will create an error
in calibration and setup. Use only quality foam
concentrate.
7) Measure the amount of concentrate injected over
time and compare to the level indicated on the
display panel during this time. The output of the
FoamPro High Pressure System must be set at a
constant 8 GPM + 0.20 GPM/-0.5 GPM. Injection
rate is easily changed by turning the foam % control
knob on the display panel. The foam percentage is
indicated on the display panel and is read using the
largest diameter of the foam percent float. Repeat at
each indicated % if desired.
8) The water inlet flow rate may be adjusted by
changing the engine RPM. Increasing the engine
RPM will increase the flow rate. Decreasing the
engine RPM will decrease the water inlet flow rate.
Varying engine RPM will change calibration settings.
NOTE: The viscosity of different foam concentrates may
have an effect on the amount of foam concentrate that
is injected into the water stream. When checking the
calibration of the system, use the foam concentrate that
will be used most frequently during normal operations.
When different viscosity foam concentrates are used, the
actual concentrate injection may vary as much as 100%.
PRESSURE RELIEF VALVE ADJUSTMENT
The pressure relief-unloader valve is factory tested, but
not preset and adjustment is required before system
is used on a continual basis. After setting the valve
properly, no other adjustments will be required. The
following procedure is provided for proper adjustment.
1) Start the system and run the pump to maximum
RPM with the foam spray gun in the open position.
2) Turn the adjustment knob so the pressure on the
gauge is at 1200 PSI (83 BAR).
3) While observing the pressure gauge, slowly
increase the pressure by turning the adjustment
knob clockwise until the pressure gauge is no longer
moving.
4) Turn off the foam spray gun and open it again to
ensure the pressure is at the same pressure as set.
5) Turn off the spray gun and shut off the engine.
Remove the adjustment cap and lock the adjustment
nut into place. Replace the adjustment cap.