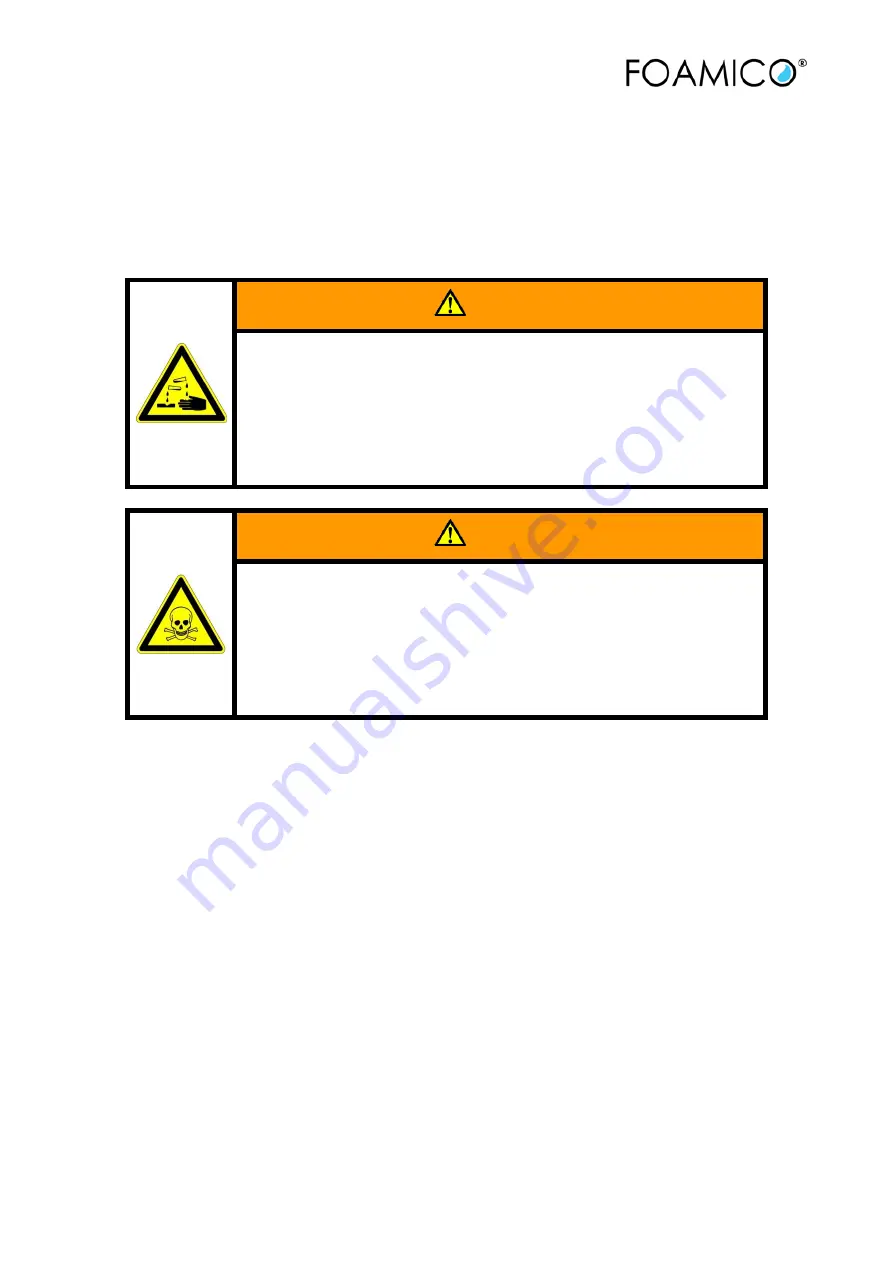
18
B 540-27-F + feed pump_7009077
US – 07-02-2019
6
Maintenance
ATTENTION! When the system is serviced, the main power switch must always be switched off.
6.1 Rinsing hose.
WARNING
Risk of chemical burns
Damaged hoses can lead to injury from chemical burns.
The rinsing hose should be checked for any damage or week point before taking
it into use every day.
Do not drive across the hose. Be careful not to damage the hose on any sharp
edged or corners.
WARNING
Danger of poisoning
A damaged hose can cause injury from poisoning or harmful vapours.
The rinsing hose should be checked for any damage or week point before taking
it into use every day.
Do not drive across the hose. Be careful not to damage the hose on any sharp
edged or corners.
For security reasons it is recommended to change the hose at least once every 12 months.
6.2 Nozzles.
Nozzles are warned over time. And warned out nozzle is less effective. It can result in less rinsing power,
higher water usage, higher chemical consumption. Check the nozzles on a regular basis. 1 to 2 times every
month is recommended. Change the nozzle if they are damaged. To be sure you will get the optimized result
we recommend using FOAMICO nozzles.
6.3 Low pressure valves / guns
They must be checked regular. The nut on the handle has to tighten regularly. Check couplings, swivels,
handles for any damaged. A damaged part must be changed for security reasons.
6.4 Couplings.
Couplings should be cleaned and greased on a regularly basis. Use only approved grease. This will extend
the live time of couplings. Always make sure there is a nozzle or lance mounted in the coupling before
opening. Rinsing through an open coupling can damage the O-rings.