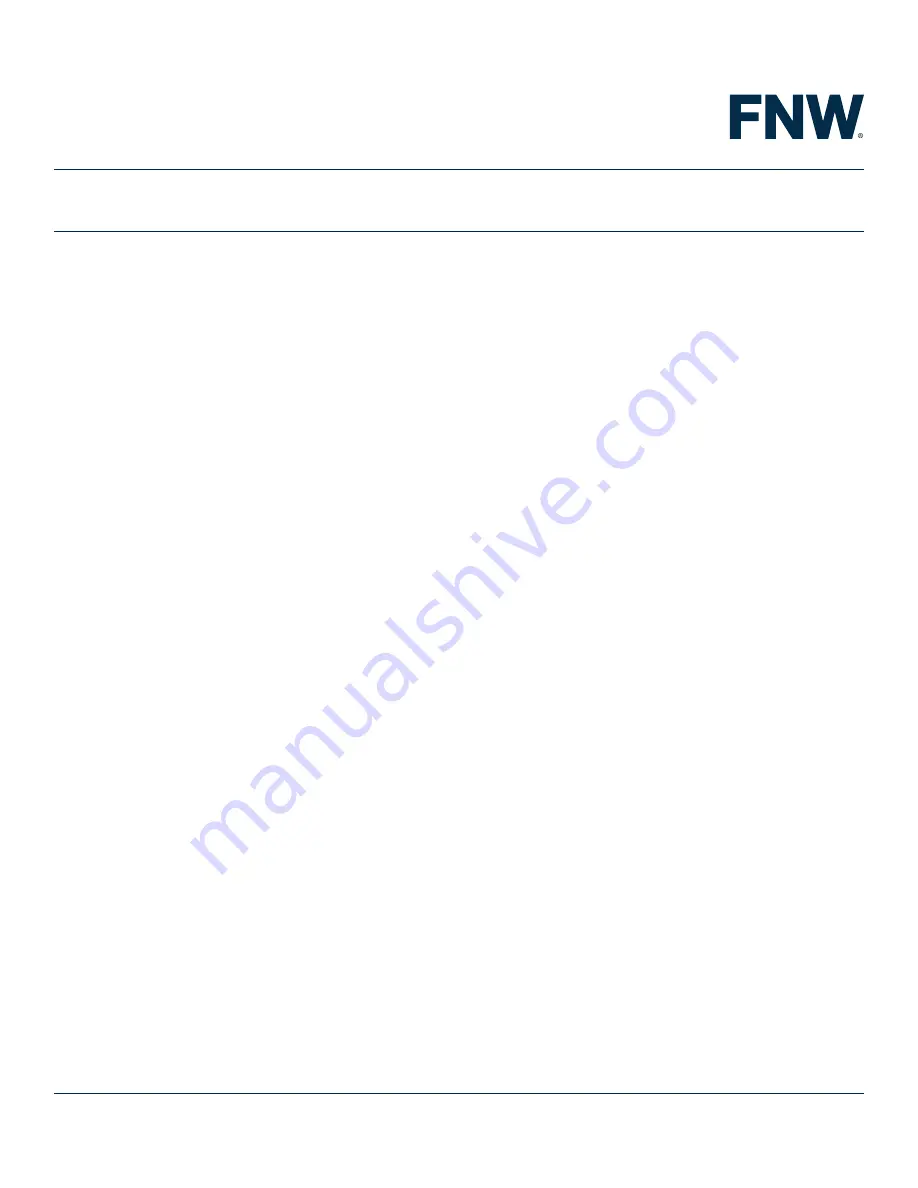
RESILIENT-SEATED CARTRIDGE STYLE
FNW7XX
BUTTERFLY VALVE
INSTALLATION INSTRUCTIONS
FNW.COM
We reserve the right to modify or improve the designs or
specifications of our products at any time without notice.
6
7. INSTALLATION CONSIDERATIONS IN PIPING
It is important to make sure the ID of the pipe and pipe flanges are large enough to allow the disc edge to swing into the opening without
interference. Damage to the disc edge can severely affect the performance of the valve. Information below shows probable compatibility
to various flanges and pipe types; however, due to manufacturing tolerances, the valve disc should always be checked for proper
clearance once installed.
Metal Flange
Resilient-seated butterfly valves are designed to meet many different types of flange standards, including ASME, DIN, JIS and other
international flange standards. Whether flat faced, raised faced, slip-on, welding-neck, etc., proper alignment of any butterfly valve
between flanges is critical to good performance of valve. The flange bolts must be evenly tightened around the valve, providing
consistent flange compression of the molded o-ring in the seat face. See piping bolt pattern in section 8 when tightening bolts.
A uniform flange face is critical to proper valve sealing. Most welding-neck and slip-on flanges conforming to ASME specifications have
an appropriate flange face. Type A and B butt-weld stub-end flanges also provide a suitable mating surface for the molded o-ring in
butterfly valve seat. Buyer is to ensure that the face of the flange selection creates a proper sealing contact with the valve seat face.
It should be noted that Type C butt-weld stub-end flanges have an “as formed” flange face. The varying surface of this flange face
can create sealing problems between any resilient-seated butterfly valve and the flange face. For this reason, Type C flanges are not
recommended for use with resilient-seated butterfly valve.
The seat ring might become damaged or the flange may leak if the flange faces contact the valve seat ring as below.
•
Excessive weld – The resulting oversized inner pipe diameter may cause a flange leak.
•
Sharp Edge – Flange face with sharp edge may cause damage to the seat ring.
•
Rough Surface from grinding on flange face also may cause flange leak.
Make sure that there is no distortion to the flange and that there is no damage, such as scratches, uneven surface in flange faces.
Non-Metal Flange (PVC/Plastic Flange)
When non-metallic flanges, such as plastic or PVF, are used with resilient-seated butterfly valves, be careful not to overtighten the
flange bolts. The inherent flexibility of non-metallic flanges allows them to be overtightened relatively easily. Flexing caused by this
overtightening can actually reduce the compression of the valve between flanges, causing leaks between the valve and the flange face.
Proper alignment and firm even, but not excessive tightening, of flange bolts is especially important with non-metallic flanges. In some
cases, non-metallic flanges of low quality will not mate tightly with butterfly valves regardless of the care taken during installation.
Valve Orientation
FNW recommends valve be installed with the stem in vertical position and the actuator mounted vertically directly above the valve. When
space restrictions do not allow, valve can be installed in upside down position. There are special applications where stem should be
horizontal. For slurries, sludge, mine, pump stock, dry cement and any other media with sediment or particles, it is recommended that
you install with stem in the horizontal position with the lower disc opening in the downstream direction.