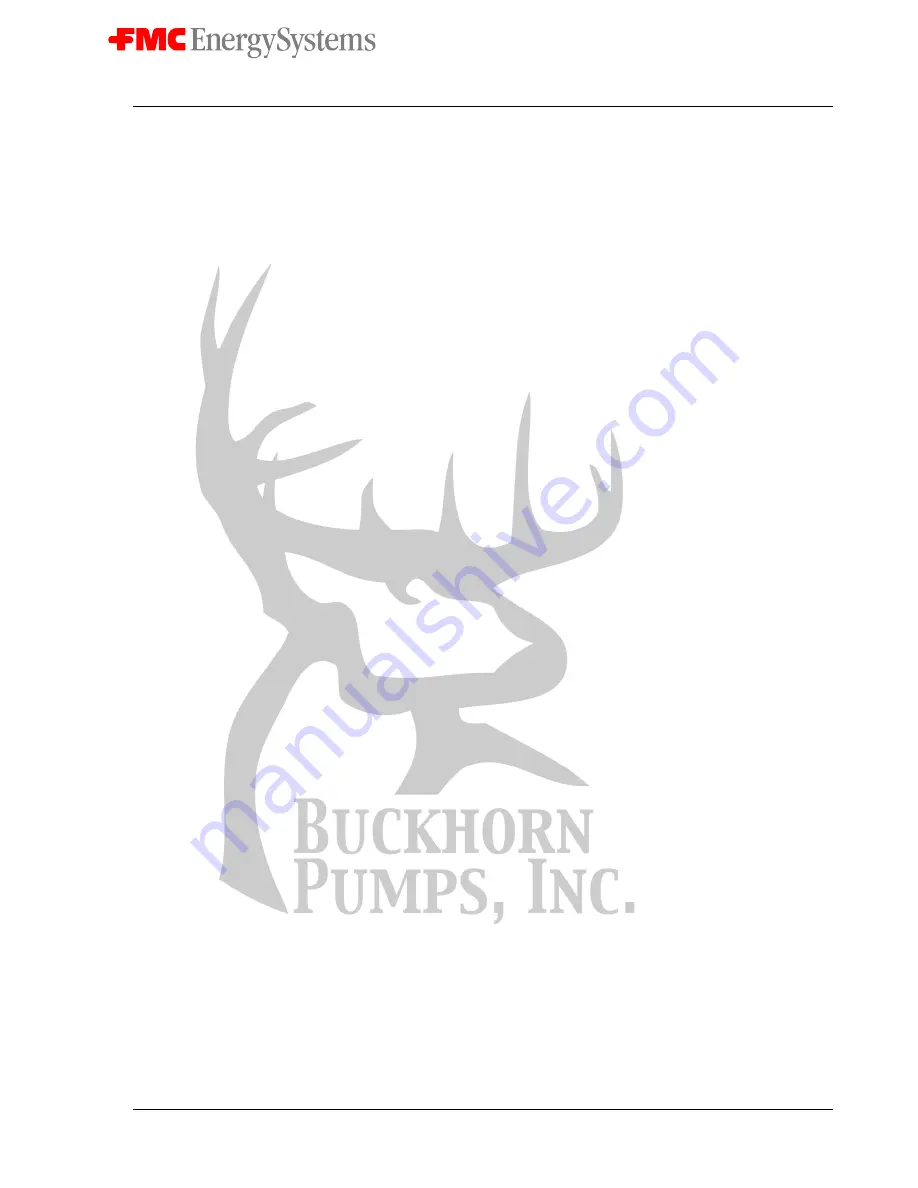
Doc. No.: OMS500000104
Rev: A Page 8 of 42
Subject to contractual terms and conditions to the contrary, this document and all the information contained herein are the confidential and exclusive
property of FMC Technologies, and may not be reproduced, disclosed, or made public in any manner prior to express written authorization by FMC.
3. Spray a rust preventative onto all exterior machined surfaces paying careful attention to
any unpainted areas like the crankshaft extension and plunger rods. Remove the power
end breather cap and store in a dry place. Cap the breather opening with a plug or other
suitable means in order to keep the preservative atmosphere sealed inside the power
frame.
4. Never store the pump on the floor or ground. Always place it on a shelf or pallet that is
several inches above ground level. Cover the entire pump with a canvas or plastic tarp.
Periodically inspect the unit and rotate the crankshaft by hand several turns during each
inspection. Drain and replace the rust inhibitor after every six (6) months of storage.
5. Before operating the pump, drain the preservative and lubricating oil mixture from the
power end. Reinstall the drain plug, breather/filler cap, and any other components that
were removed for storage. Once these steps have been completed, follow the normal
pump start up procedures outlined in this manual. FMC can factory prepare units for
extended storage for a nominal fee if specified at the time of order.
3.4
Precautions during Freezing Weather Conditions
1. Freezing weather can cause problems for equipment when pumping water based fluids
that expand in volume when changing from a liquid to a frozen solid state. For example,
when water is left in a pump fluid end and exposed to freezing temperatures, the
expansion of the water as it freezes can rupture the fluid cylinder of the pump and cause
permanent equipment damage or personal injury.
2. Whenever the pump is stored or idle in conditions that are near or below freezing, any
water based fluids should be removed from the pump. The best way to do this is to run
the pump for a few seconds with the suction and discharge lines disconnected or open to
atmosphere. This will clear the majority of the fluid from the pumping chamber as well
as the suction and discharge manifolds. After the run, blow compressed air through the
fluid end to remove all traces of fluid. If possible, lift up the suction valve seats to insure
that all fluid is drained from the pumping chamber between the suction and discharge
valves.
3. As an alternative to the previous procedure, a compatible antifreeze solution can be
circulated through the fluid end. RV antifreeze, propylene glycol, is recommended for
this purpose.