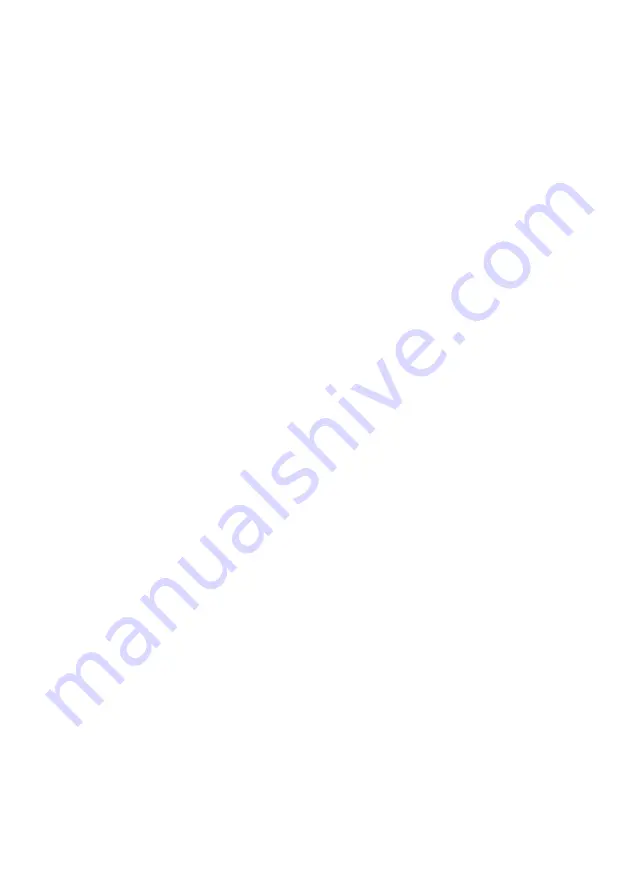
13
3. Operating environment:
a. Place the machine in a well-ventilated area.
b. Avoid rain, moisture, liquids, or direct sunlight.
c. The ambient temperature should be between 5°C and
35°C (41°F and 95°F), and humidity between 10% and
75%.
d. If venting outdoors, make sure that changing conditions
do not cause extreme temperatures or humidity to affect
the machine through the exhaust duct. Disconnect the
duct from the outside air when the machine is not in use.
e. Place the machine on a stable surface to prevent it from
moving or overturning.
Electrical Safety
1. The machine comes in 2 versions, 110V and 220V. Do not use
a power source other than the AC rated voltage. If in doubt,
contact FLUX Support. (110V: 100 - 127V / 220V: 200 - 240V)
2. Make sure that the grounding pin is properly connected. If
not grounded properly, static electricity might be generated
that could affect performance and even increase the risk of
electric shock.
3. Do not use the power cord if it is damaged.
4. When maintaining or disassembling the machine with the
consent of FLUX Support, be sure to turn the power off and
unplug the unit.