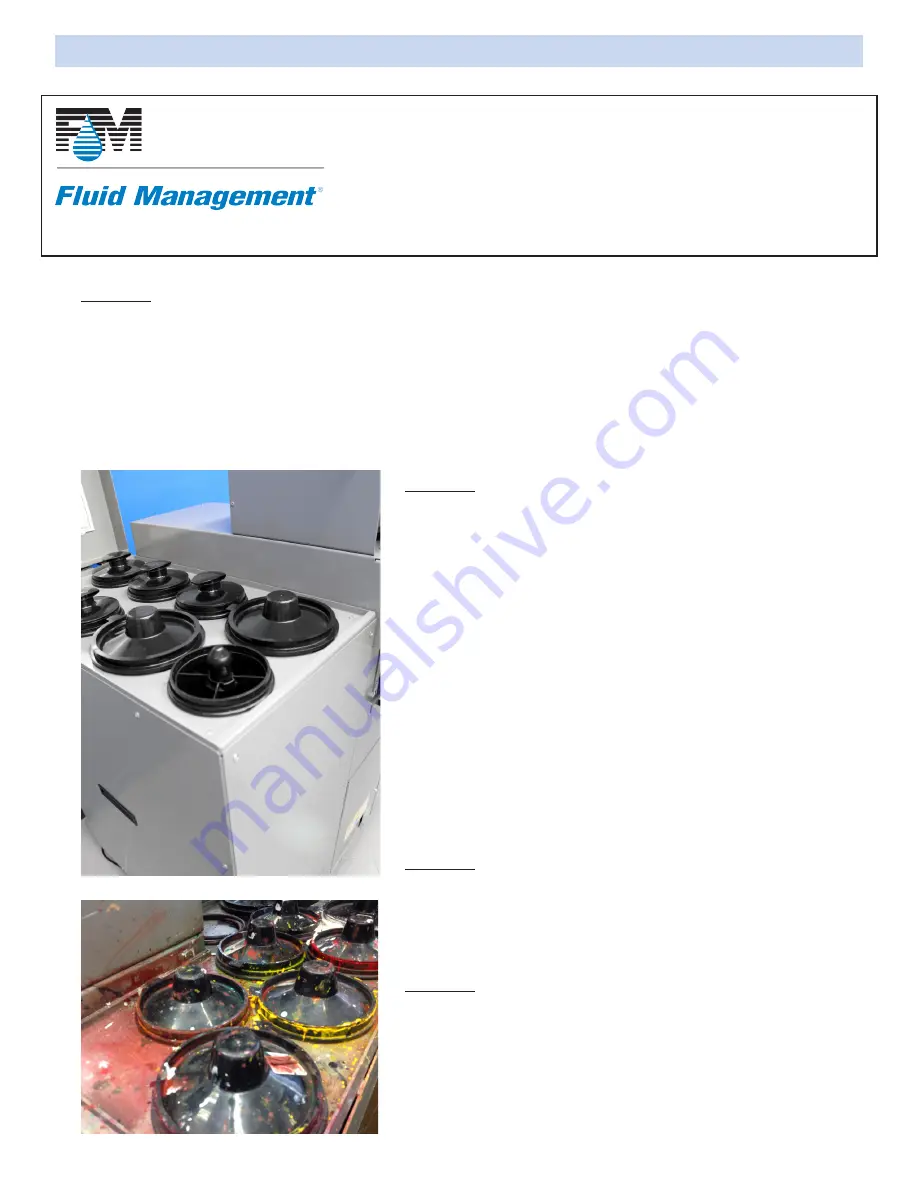
S
uggeSted
C
leaning
M
aintenanCe
g
uide
Step 1
Clean all accessible surfaces and cabinet with a non-flammable mild
cleaning solution or cleaning wipes.
DO NOT USE SOLVENT BASED CLEANING AGENTS OR FLUIDS WITH
FLASHPOINTS BELOW 100°F.
Step 2
When cleaning spill tray and around
canisters,
Use caution around each
canister so that liquids do not spill into
the machine chassis.
Use caution around the O-rings (on select
machines) between the canisters and the
top spill tray as to not damage them.
Do not attempt to lift or remove
canisters from spill tray.
Step 3
Spilled or excess liquids should be
removed immediately.
Step 4
Replace damaged decals.
If O-rings
(on select machines)
are
damaged, contact Fluid Management to
replace them.
Appendix A: Suggested Cleaning Maintenance Guide
Summary of Contents for Accutinter 1600
Page 2: ......