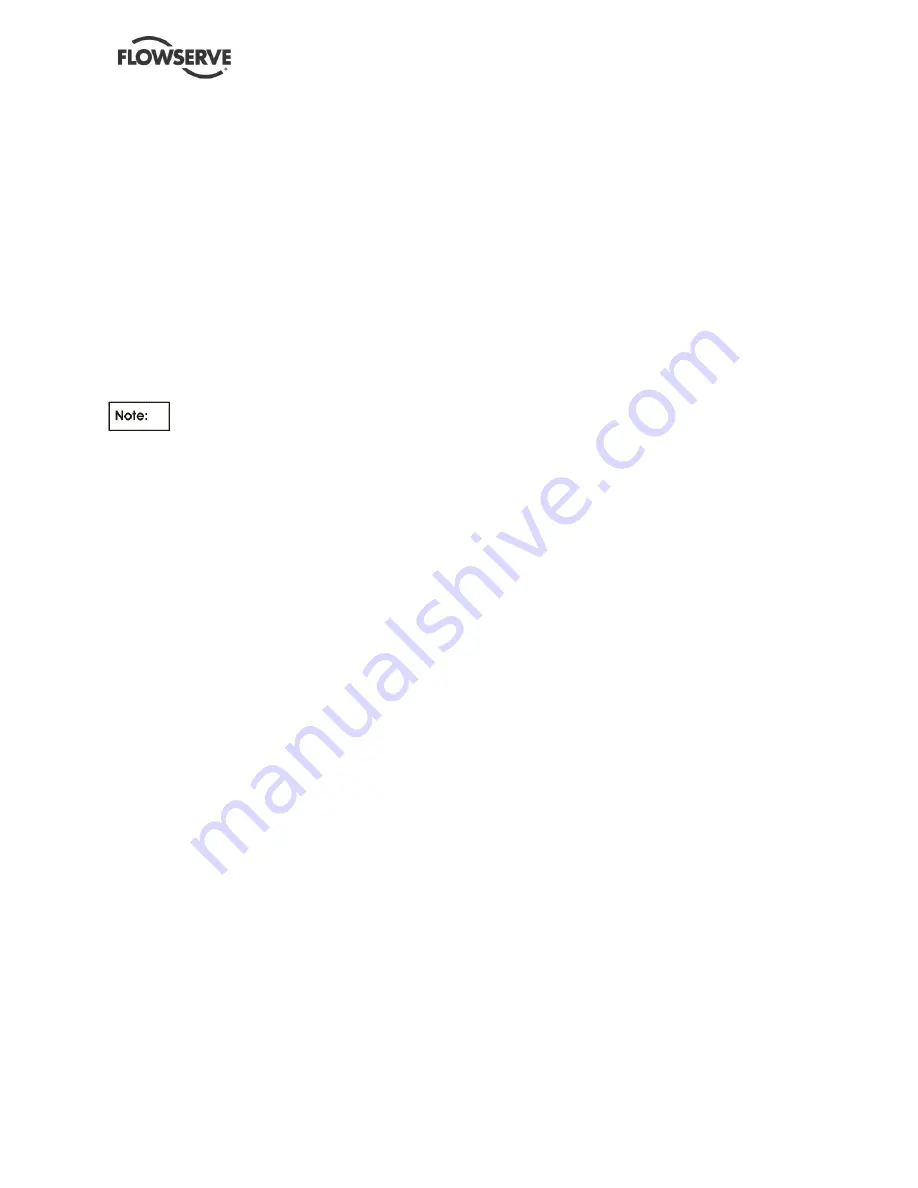
WIK USER INSTRUCTIONS ENGLISH BO2662 5/09
Page 66 of 76
11) Install sensor disc [2900] (if it is located on the
end of the shaft) and outer retaining plate (if
applicable).
12) Apply an even film of Loctite Gasket Eliminator
504 (or equivalent) to parting surface of bottom
halves of bearing housings. Note cure time on
the container.
13) Set top halves of bearing housing on bottom
halves. Install cap screws in flanges and evenly
tighten.
14) Wipe off any excess gasket sealant.
15) Temporarily install end cover [3266] without
sealant. Evenly tighten cap screws [6570.7].
16) Install dial indicator to read on end of shaft.
17) Firmly push shaft in one direction until it stops
solidly and set dial indicator to zero.
lf in doubt about how to machine the end
cover [3266], contact your nearest Flowserve Sales
Office (See section 6.2.1).
18) Push shaft in opposite direction until it stops
solidly. Read dial indicator. Shaft movement
should be within the thrust bearing axial
clearance specified under section 10.3. If a
minute adjustment is necessary, make certain
that bearing, seal units, and internal assembly
parts are correctly sized and assembled, then
machine either:
a) End cover [3266] surface that abuts thrust
bearing [3032] if low limit is exceeded,
b) End cover [3266] surface that abuts bearing
housing [3230], if high limit is exceeded.
19) If pump is equipped with mechanical seal units,
tighten shaft sleeve collars (or nuts) and secure
them with set-screws. Unlock shaft sleeve from
seal plates, see mechanical seal (section 6.9.4).
20) Position deflector rings [2540] or Inproseal rotors
per dimension given in section 10.3.
21) Verify that the rotor turns easily and smoothly by
rotating shaft [2100].
22) To secure the cartridge assembly, install the
tension flange in
place of the pump half-coupling
on the shaft and secure it with the coupling nut
(7411), see
Figure 6-5
: Typical
Tension Flange
Arrangement. Some cartridge assembly may
use coupling nut [7411] and pump half coupling
with the tension flange, then install the tension
flange between the pump half coupling and
bearing housing.
23) Remove thrust bearing housing end cover
(3266). Apply an even film of sealant to parting
surface of end cover that abuts bearing housing.
Install cover with stationary oil baffle or Inproseal
stator (if installed), and evenly tighten cap
screws.
6.9.6 Main Lube Oil Pump Installation
These instructions provide for installation of a
lubricating oil (lube oil) pump that is flange-mounted
to the outboard bearing housing end cover [3266] for
direct and axial coupling of its shaft with the pump
shaft. If your pump is not equipped with such a lube
oil pump, please disregard this section.
6.9.6.1 Installing Half-Couplings (Lube Oil Pump)
To install half-couplings, proceed as follows:
1) Verify that vibration sensor disc [2900] is
installed, if applicable (see assembly drawing),
also verify that bearing end cover [3266] is not
installed (see section 6.9.5).
2) Install half-coupling key in shaft of vibration
sensor disc [2900] or in end of pump shaft,
whichever is applicable (see assembly drawing),
slide half-coupling completely onto key, and fix
half-coupling to shaft of disc or end of pump
shaft, whichever is applicable, with set screw.
3) Install spider in half-coupling on shaft of
vibration sensor disc [2900] or end of pump
shaft, whichever is applicable (see assembly
drawing).
4) Install half-coupling key in shaft of lube oil pump,
slide half-coupling onto key, allowing coupling
face to extend past end of lube oil pump shaft.
Do not install set screw.
5) Solidly butt together flanges of lube oil pump
and bearing end cover [3266]; then withdraw
lube oil pump. Measure 1.5 mm (0.06 in.) from
hub of half-coupling toward lube oil pump case
and mark distance on shaft; then move half-
coupling hub to mark and secure it to shaft with
set screw. There shall be a total gap of 1.5 mm
(0.06 in.) between spider and half-couplings.
6) Remove end cover [3266]. Apply an even film of
sealant to parting surface of end cover [3266]
that abuts bearing housing [3230]. Install cover
with stationary oil baffle or Inproseal stator (if
installed), and evenly tighten cap screws.
7) Wipe off any excess sealant.
6.9.6.2 Installing Lube Oil Pump
To install the lube oil pump, proceed as follows:
1) Ensure:
a) That lube oil pump has been inspected and
assembled for operation as given by
manufacturer's instructions in section 10
b) That half-couplings are free of burrs and
gouges
c) That half-couplings are installed and held
firmly in place by set-screws (see section
6.9.6.1 above).
2) Install spider in half-coupling on shaft of
vibration sensor disc [2900] or end of pump