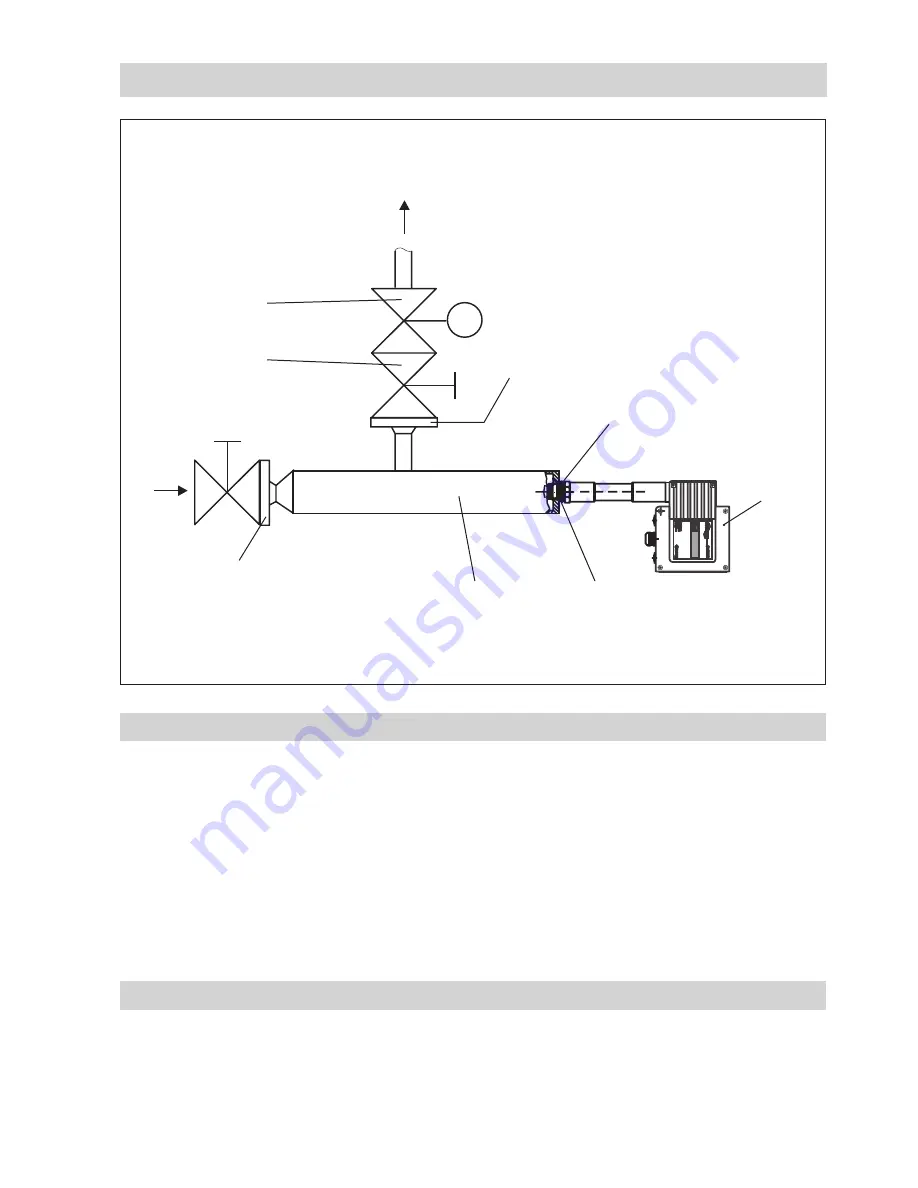
17
Examples of Installation
– continued –
A
Ring joint 33 x 39, form D, DIN 7603, 1.4301, bright annealed
4
Boiler drum
5
Shut-off valve GAV
6
Continuous blowdown valve BAE
7
Measuring pot
8
T-type connector
Key
Fig. 9
Conductivity monitoring and continuous blowdown control, installation of conductivity transmitter in
blowdown line via separate measuring pot
M
G
E
S
T
R
A
S
te
a
m
S
ys
te
m
s
G
E
S
T
R
A
S
te
a
m
S
ys
te
m
s
G
E
S
T
R
A
LR
G
T
....
G
E
S
T
R
A
LR
G
T
µ
S
-p
p
m
6
5
1" BSP
EN ISO 228-1
DN 15-40
Outlet
Inlet
DN 15-40
7
A
Tools
Open-end spanner 18 (19) A. F.
Open-end spanner 41 A. F.
Screwdriver for hexagon-socket head screws, size 1.3
Screwdriver for cross-recess head screws, size 1 and 2
LRGT 16-1
LRGT 16-2
LRGT 17-1