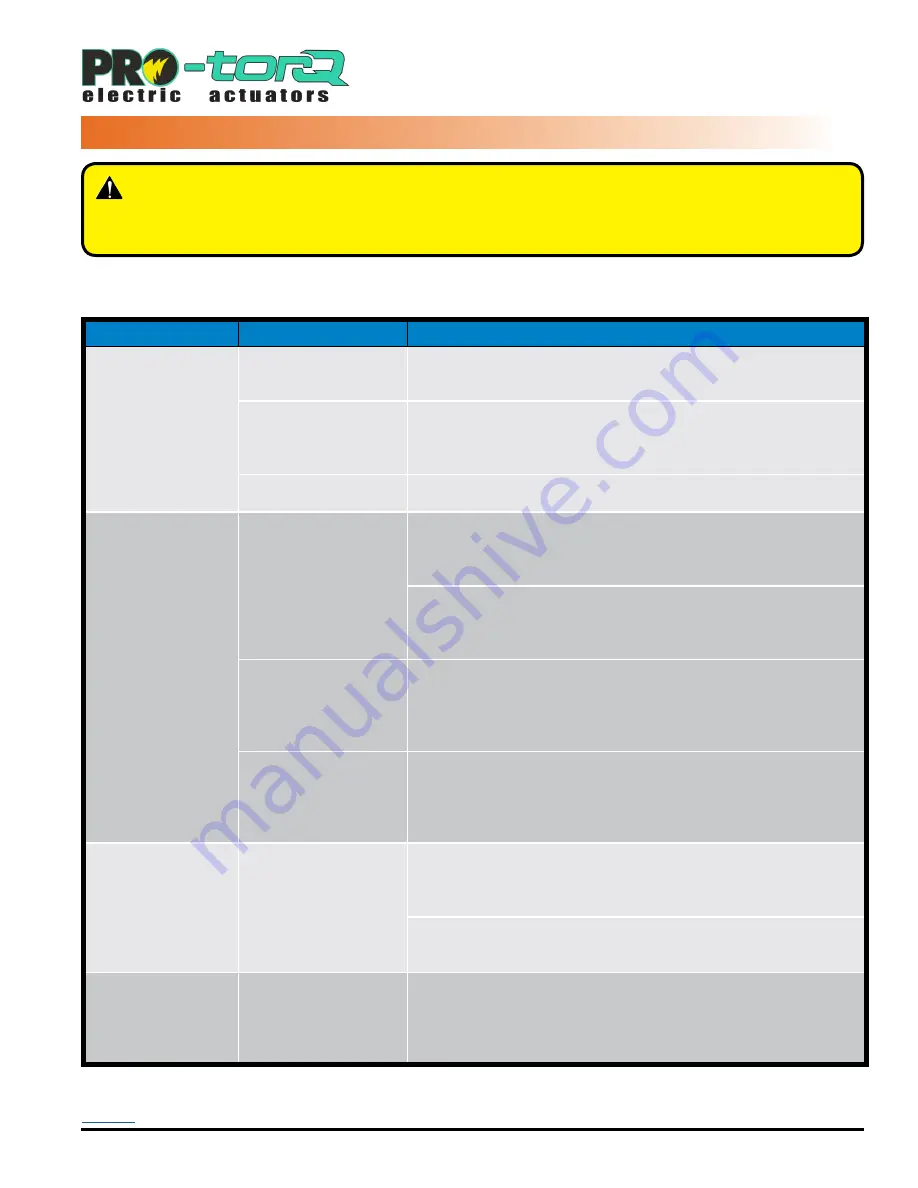
Symptom
Target
Action
Actuator does
not move when
commanded
to do so .
Power Source
Measure incoming power AT the actuator terminal block.
Reference the correct wiring diagram.
Control Problem
Generate move commands by the fi eld device. Measure correct
voltage changes between HOT and terminal #6 (CCW) and HOT
and terminal #4 (CW).
Wire Sizing
Check for correct wire size per Wire Sizing Chart.
Supply and
controls are
measured to
be correct, but
actuator still does
not move .
Overtorque
Remove the actuator from the driven device. If the actuator now
moves, the torque required by the mechanical device exceeds
that of the actuator. Increase actuator size.
With the actuator removed from the mechanical equipment,
manually rotate the valve or damper through its intended range
of travel to check for mechanical problems.
Insuffi cient power
supply and/or
incorrect wire size
during installation.
Measure the voltage between terminals 1 & 2 WHILE
commanding the actuator to move. The measured voltage
cannot drop more than 10%.
Cams improperly
set.
REMOVE POWER. Check to see if cams rotate freely on the
cam shaft using your fi nger. Cams MUST be secure and set
according to the procedures in the Adjusting CW/CCW End of
Travel section.
Motor is extremely
hot to the touch .
Control “noise” or
excessive duty cycle
Check for stray voltage fl uctuations on the incoming control
signals. The on/off line voltage actuators have a maximum 25%
duty cycle. While the low voltage models have a 75% duty cycle.
Check for parallel wiring of multiple on/off actuators. Review the
site as-built wiring diagrams to verify.
Actuator does not
stop at correct
position at either
end of travel
Travel cams and/or
mechanical stops not
positioned correctly
Reset end-of-travel cams and/or mechanical stops as detailed
in the Adjusting CW/CCW End of Travel section.
After completing all mounting and wiring procedures and main power is available, if the actuator does NOT respond
as expected, the following procedure(s) may help in identifying the problem.
WARNING –
To avoid dangerous or fatal electrical shock, turn OFF power to all electrical
equipment before working on electrical connections. If it is necessary to
troubleshoot with live power to the actuator, please use EXTREME CAUTION,
and follow your company's safety protocols and procedures at all times.
ON/OFF MODELS
TROUBLESHOOTING
USE ONLY FLO-TITE GENUINE REPLACEMENT PARTS
ELo Rev C ECR 044V
Page 1
7
of 28
www.flotite.com