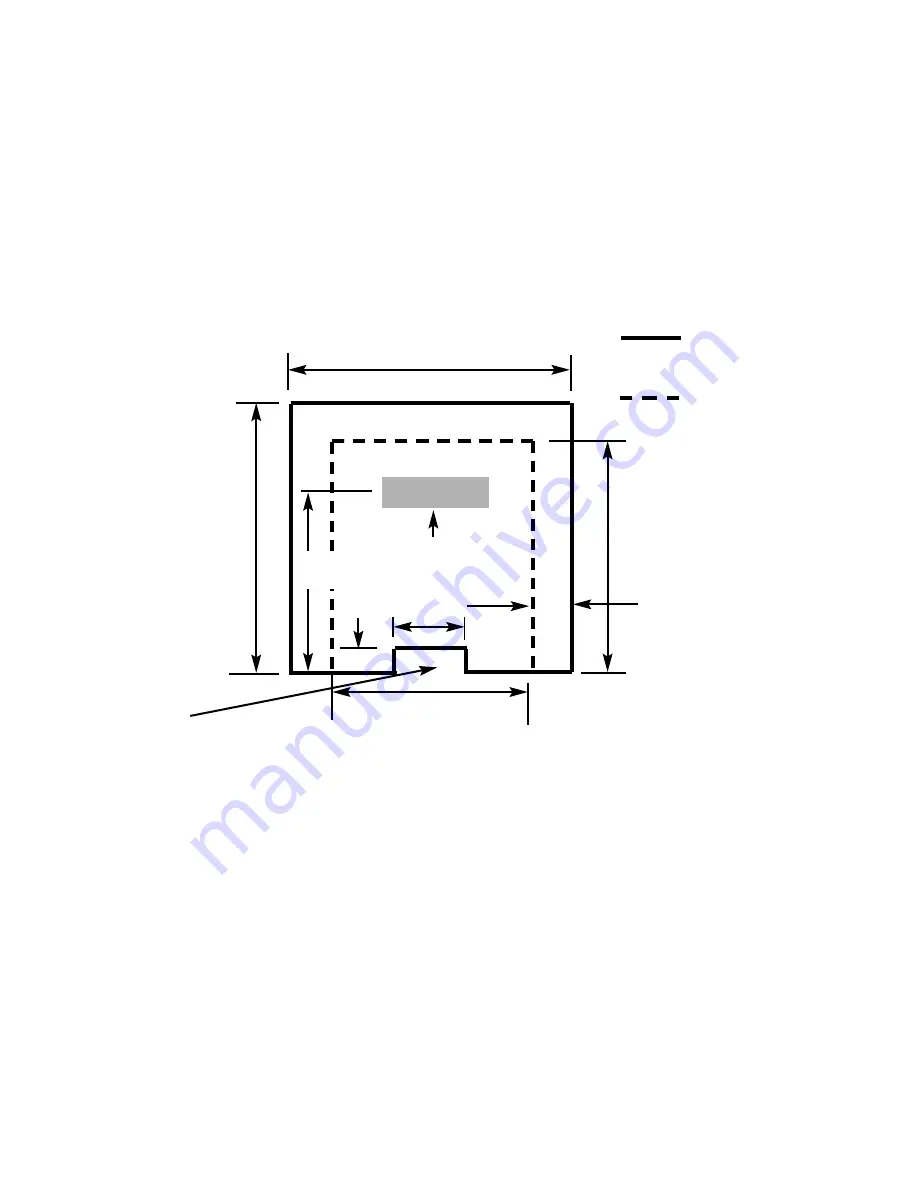
Closure plate
a)
Fit the closure plate to the fireplace opening and ensure that it has a flat
sealing area of at least 10mm sealed on all sides. See Fig. 3 below
Dimensions stated are for closure plate supplied
Check the operation of the chimney as follows:-
Apply a smoke match to the flue spigot opening in the closure plate and observe
the smoke. If there is a definite flow into the opening then proceed with the instal-
lation. If there is not a definite flow into the opening, pre-heat the chimney for
about two minutes and retest for flow. If there still is no definite flow into the open-
ing, the chimney may require attention. DO NOT FIT THE FIRE-SEEK EXPERT
ADVICE.
10
Minimum 10mm
Flat Sealing Area
Spigot Opening
168 x 68mm
660mm
460mm
462mm to
CTR
525mm Minimum
650mm Maximum
Fireplace
Opening
Dimensions
Closure
Plate
Dimensions
Air Relief Openings
Fig. 3
305mm Minimum
440mm Maximum
100mm
15mm