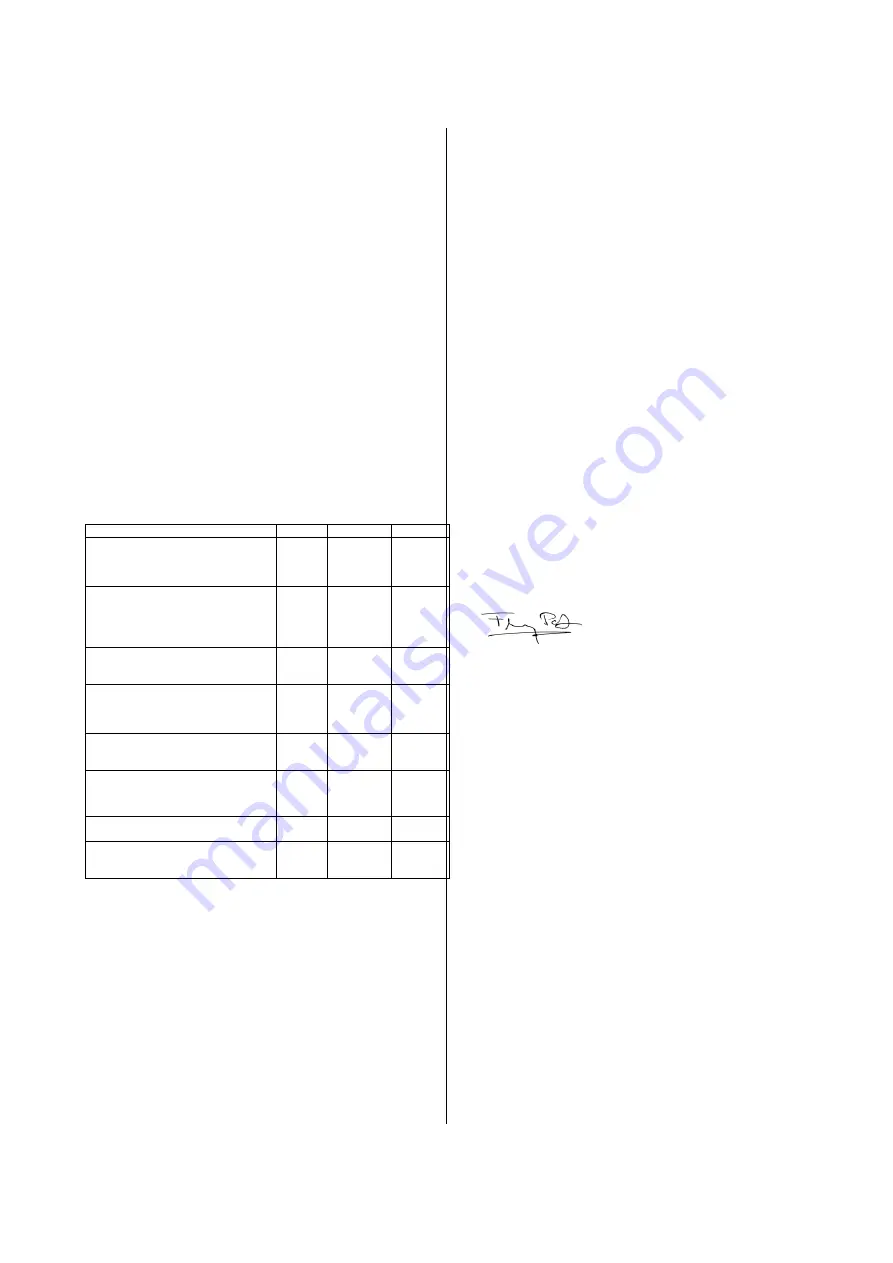
FL
AIR
MO ApS
–
Lundeborgvej 3
–
DK-9220 Aalborg
–
Denmark
Phone: +45 53717220 Web: www.flairmo.dk - E-mail: [email protected]
9. Vacuum pump starts and stops more frequently than
usual:
a) Leaks. See point 4f.
10. Vacuum pump does not start at minimum vacuum or
does not stop at stop vacuum:
The following points only apply to units with vacuum gauge:
a) Vacuum switch defective. Replace.
b) Vacuum switch is not adjusted correctly. Adjust correctly.
11. Compressor does not switch on against pressure or
does not switch off at max. pressure:
a) Defective pressure switch. Replace.
Test the non-return valve
·
Once a year.
·
Switch off compressor on the main switch and pull out the plug.
·
Pull the ring at the end of the safety valve (fig. 3).
Warning:
Loud noise!
·
Let pressure fall to 0 bar. The pressure is to be read on the
pressure gauge for receiver pressure.
·
If the compressor is mounted with a TÜV-approved safety
valve, the receiver is emptied by loosening the screw at the
end of the safety valve.
·
Dismount non-return valve from receiver (fig. 4).
·
Disassemble non-return valve and clean it (fig. 5)
·
R
e-assemble and mount the non-return valve again
(fig. 4).
Preventive maintenance (all)
Weekly
Monthly
Annually
Drain condensate from air receiver.
If equipped with autodrain, this will
take place automatically, however,
drain bottle has to be emptied.
x
If compressor is fitted with outlet
filter, check and empty for water
by pressing the black button at the
bottom. If fitted with autodrain, this
will take place automatically.
x
Check motor, air tubes, hoses and
equipment for leaks, and check the
pumping time.
x
Clean unit or wipe with a soft, damp
cloth. If necessary, use paraffin on
rag to remove sticky adhesions.
Dust and dirt prevent cooling.
x
Check intake filter. Clean or replace
if necessary. Min. annually or every
2000 hours whichever comes first.
x
Check the O-ring in the non-return
valve and replace, if necessary.
Note! Empty receiver of air before
dismounting.
x
Check filter and filter elements for
optimum efficiency.
x
Test the safety valve by gently
pulling the ring with pressure in the
receiver.
x
Check the pumping time (Comp.)
The pumping time indicates the condition of the compressor
provided that there are no leaks in the system where the
compressed air may leak. Test the compressor as follows:
1. Empty the air receiver of compressed air (the pressure
gauge shows 0 bar).
2. Close the outlet on the air receiver and check that the drain
cock is closed.
3. Start the compressor and note how long it takes until it
switches off.
Ensure that the pressure in the air receiver is 8 bar/120 psi
as deviations may indicate the wrong results.
Pump up time for this compressor is approx. 60sek.
Important!
Always test the compressor when cold as the time
indicated refers to the pumping time of a cold
compressor. The pumping time of a warm compressor
is much longer and consequently, the result would be
misleading.
Pressure vessel
Directions for use
Application: Receiver for compressed air.
Receiver specifications: See name plate.
Installation: Tubes, etc. must be made of suitable materials.
Placement: Observe the working temperature of the receiver.
Ensure that sufficient room for inspection/maintenance is
available in a horizontal position.
The receiver must be kept in a horizontal position..
Corrosion protection The surface treatment must be maintained
as required.
Internal inspection at least every 5 years.
Drain moisture at least once a week.
Alternation/repair No welding must be made on pressurized parts..
Safety valve Ensures that PS will not be exceeded.
Never adjust to a higher pressure than PS.
The capacity of the valve must be calculated in accordance
with the volume of air supplied by the compressor.
(PS = Maximum working pressure of the receiver)
Declaration of Conformity
NOTE: The declaration of conformity is only valid for units
operating at 230 V/50 Hz, 3x400 V/50 Hz, 12 V DC or 24 V DC.
The manufacturer, FLAIRMO ApS, declares that the products
mentioned in this manual are in conformity with:
• 87/404/EEC - 90/488/EEC - 93/68/EEC Council Directive
relating to Simple Pressure Vessels
• 98/37/EC Machinery Directive
• 89/336/EEC EMC Directive
• 73/23/EEC Low Voltage Directive
Flemming Steen Petersen
Teknisk Direktør