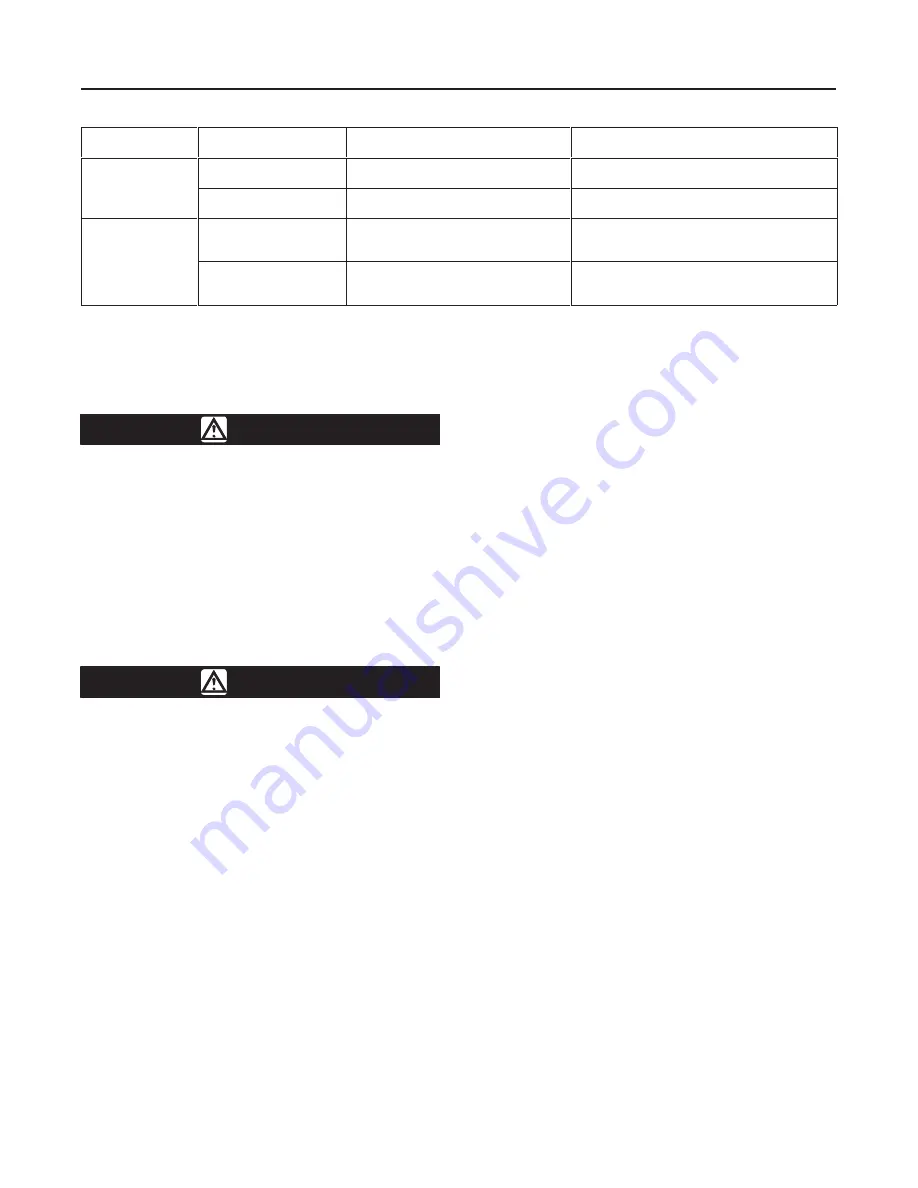
14 through 20-Inch Design V150 and V300
3
Table 3. Valve Sizes, End Connection Styles, and Ratings
VALVE BODY
MATERIAL
FLANGE COMPATIBILITY
RATING
FACE-TO-FACE DIMENSION
WCC steel
ANSI Class 150 (V150)
raised-face
ASME/ANSI B16.34-1988 Class 150
14 and 16-Inch Valves: ASME B16.10 Short
20-Inch Valves: 20 inches (508 mm)
WCC steel
(standard)
ANSI Class 300 (V300)
raised-face
ASME/ANSI B16.34-1988 Class 300
14-inch Valves: 15 inches (381 mm)
16-inch Valves: 16 inches (406 mm)
CG8M (317 SST)
ANSI Class 150 (V150)
raised-face
See tables in Bulletin 51.3:V150 for
maximum inlet pressure and
temperature
14 and 16-Inch Valves: ASME B16.10 Short
20-Inch Valves: 20 inches (508 mm)
CG8M (317 SST)
ANSI Class 300 (V300)
raised-face
See tables in Bulletin 51.3:V300 for
maximum inlet pressure and
temperature
14-inch Valves: 15 inches (381 mm)
16-inch Valves: 16 inches (406 mm)
Key numbers are shown in figure 9, unless otherwise
indicated.
WARNING
Personal injury or equipment damage
caused by sudden release of pressure
may result if the valve assembly is
installed where service conditions could
exceed either the valve body rating or
the mating pipe flange joint rating. To
avoid such injury or damage, provide a
relief valve for overpressure protection
as required by government or accepted
industry codes and good engineering
practices.
CAUTION
When ordered, the valve configuration
and construction materials were se-
lected to meet particular pressure, tem-
perature, pressure drop, and controlled
fluid conditions. Because some valve/
trim material combinations are limited in
their pressure drop and temperature
ranges, do not apply any other condi-
tions to the valve without first contact-
ing your Fisher Controls sales office or
sales representative.
1. If the valve is to be stored before installation, pro-
tect the flange mating surfaces and keep the valve
cavity dry and free of foreign material.
2. Install a three-valve bypass around the control
valve assembly if continuous operation will be neces-
sary during inspection and maintenance of the valve.
3. Mounting the Actuator:
a. The valve is normally shipped as part of a con-
trol valve assembly, with the actuator mounted on
the valve. The factory makes actuator/valve adjust-
ments before the valve is shipped.
b. If the valve and actuator have been purchased
separately or if the actuator has been removed,
mount the actuator according to the
Actuator
Mounting instructions in the Maintenance section of
this manual.
4. Be certain the valve and adjacent pipelines are free
of any foreign material that could damage the valve
seating surfaces.
5. Be sure the mating line flanges are aligned. Pro-
vide standard flat sheet flange gaskets (or spiral
wound gaskets with compression-controlling centering
rings) that are compatible with the process fluid.
Refer to figure 2 for required clearance for valve instal-
lation and stud length. Lubricate the studs with Never-
Seez Pure Nickel Special or an equivalent lubricant.
6. Install the valve using studs and nuts to connect
the valve flanges to the pipeline flanges. The seal pro-
tector ring (key 3) end of the valve requires longer line
flange studs than standard (see figure 2). Do not at-
tempt to use standard-length line flange studs for the
seal protector end of the valve. Refer to figure 2 for
length of flange studs required.
Install all remaining studs. Tighten the nuts in a criss-
cross sequence to ensure the flange gaskets are prop-
erly loaded.
Note
The valve drive shaft is not necessarily
grounded when installed in a pipeline.
Personal injury or property damage
could result—if the process fluid or the
atmosphere around the valve is flam-
mable—from an explosion caused by a
discharge of static electricity from the
valve components. If the valve is
installed in a hazardous area, electrical-
ly bond the drive shaft to the valve body
(see figure 4).