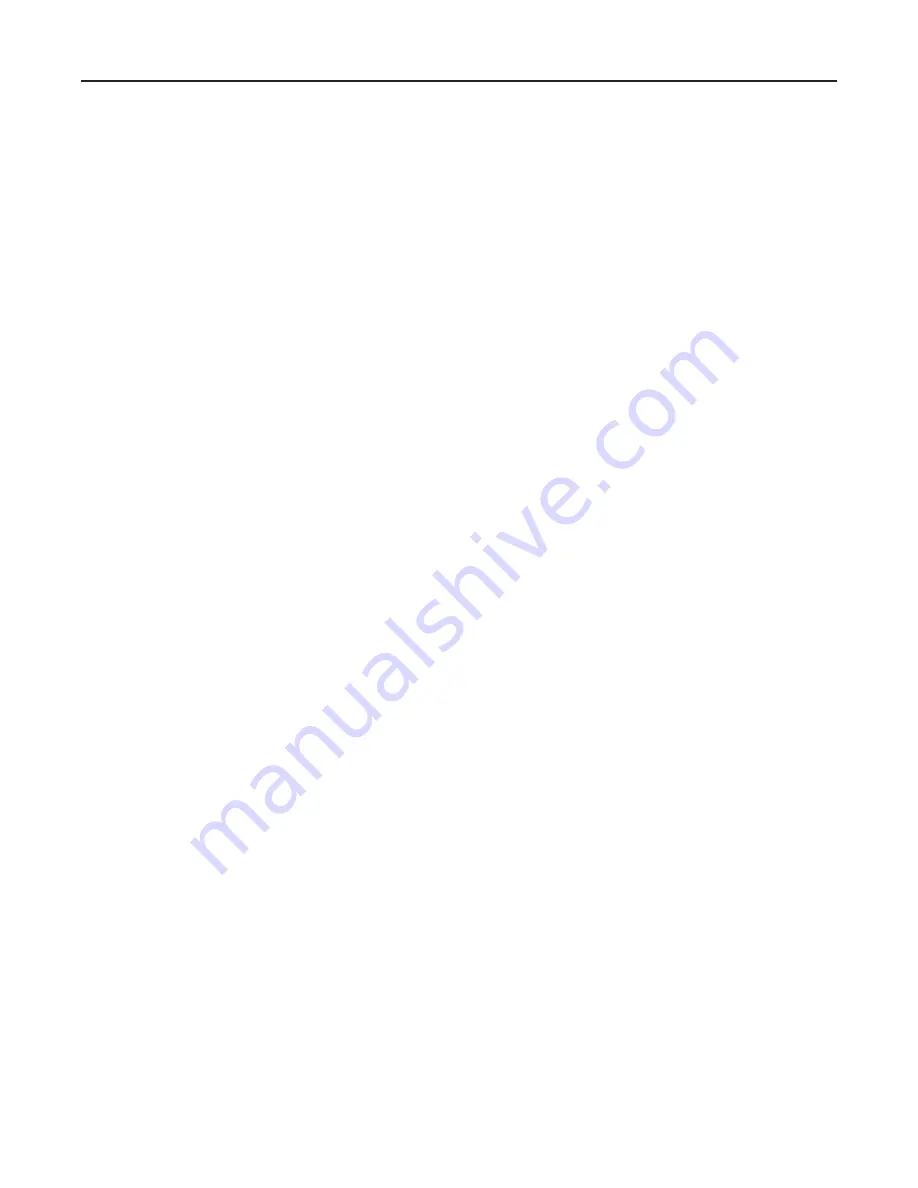
Type 627F
7
These procedures are for gaining access to the disk
assembly, orifice, diaphragm casing, O-ring, and stem
assembly. All pressure must be released from the
regulator before the following steps can be performed.
Refer to Figure 3 for key number locations.
Replacing the Disk Assembly or Orifice
If it is necessary to perform maintenance on the disk
assembly (key 9) or orifice (key 2), continue with the
following steps:
1. Remove the closing cap (key 36) and loosen the
lock nut (key 34) relieving tension spring pressure.
Hold the spring seat bolt (key 61) to prevent
turning of the bolt from the tension spring (key 32).
Remove the cap screws (key 3), and separate the
diaphragm casing (key 5) from the body (key 1).
Note
If the body cap screws (key 3) are evenly
removed and replaced very carefully,
then the tension spring force will not
need to be released.
2.
Inspect and, if necessary, remove the orifice
(key 2). If removed, coat the threads of the
replacement orifice with lubricant and torque to
25 foot-pounds / 34 N•m.
3. Inspect the disk assembly and, if necessary,
remove the hairpin clip (key 13) that holds the
disk assembly (key 9) in place. If replacing the
disk assembly is the only maintenance required,
refer to the Startup procedure.
Replacing the Stem Assembly
If it is necessary to perform maintenance on the stem
assembly, continue with the following steps.
1. Remove the boost body (key 6), O-ring (key 7),
and stem guide (key 8) from the diaphragm casing
(key 5). Unhook the stem (key 10) from the lever
(key 15) and remove from the diaphragm casing
(key 5).
2. Remove and inspect the diaphragm casing O-ring
(key 4) and stem O-ring (key 11), replace
if necessary.
3. Install the replacement diaphragm casing O-ring
(key 4) onto the boost body (key 6). Apply lubricant
to the stem O-ring and install on the stem (key 10).
4. Apply lubricant to the stem (key 10) and insert the
stem into the diaphragm casing (key 5) and hook it
on the lever (key 15).
5. Apply lubricant to the O-ring (key 7) and insert
parts removed in steps 1 and 2 into the diaphragm
casing (key 5).
6. Install the disk assembly (key 9), line up the hole
in the disk assembly and stem (keys 9 and 10) and
insert the hairpin clip (key 13).
7. Position the diaphragm casing plus attached parts
in relation to the body (key 1) so that they are
correct for the application.
8. Secure the diaphragm casing to the body with
the cap screws (key 3). For an aluminum
diaphragm casing (key 5), torque the cap screws
(key 3) to 16 foot-pounds / 22 N•m. For ductile
iron or steel diaphragm casings, torque the
cap screws (key 3) to 25 foot-pounds / 34 N•m.
Torque the two body cap screws (key 3) very
evenly to square up the orifice (key 2) and disk
assembly (key 9) seating relationship.
9. It may be necessary to reposition the diaphragm
spring case to prevent rain, ice, and foreign debris
from entering the pilot spring case through the vent.
Diaphragm and Spring Case Area
Maintenance Procedures
These procedures are for gaining access to the tension
spring, diaphragm assembly, and lever assembly. All
spring pressure must be released from the diaphragm
casing before these steps can be performed. Refer to
Figure 3 for key number locations.
1. To release the tension spring force, remove
the closing cap (key 36), the lock nut (key 34),
and washer (key 62). Hold the spring seat bolt
(key 61) to prevent turning of the bolt from the
tension spring (key 32).
2. Remove the spring case cap screws (key 37), the
nameplates, and lift off the spring case (key 29). If
changing the tension spring (key 32) or repositioning
the spring case (key 29) is the only maintenance
required, remove the spring seat bolt (key 61) from
the tension spring (key 32) and unscrew the spring
retainer (key 53). Install the replacement tension
spring. Install left hand threaded end of spring