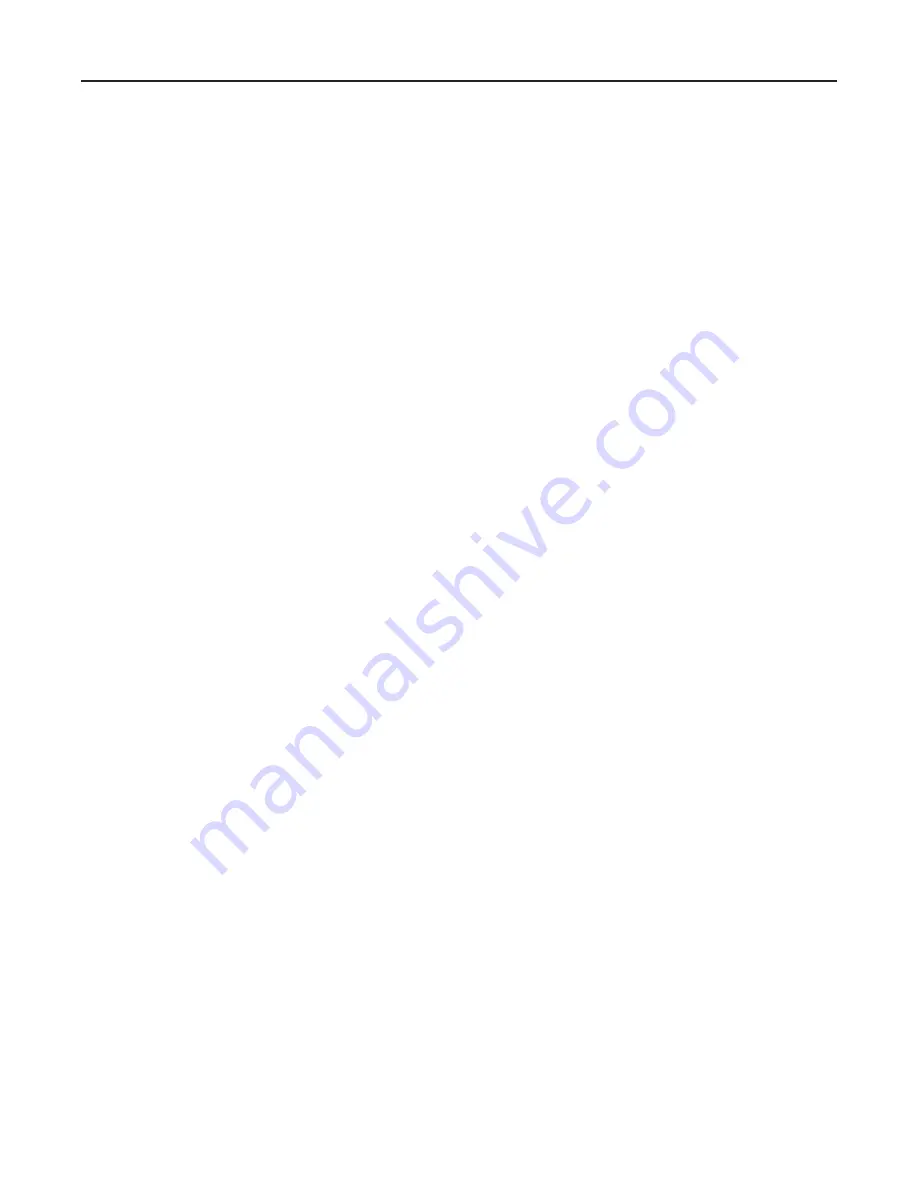
Type 627F
8
seat bolt (key 61) into tension spring (key 32) until
the spring is flush with the top of the bolt threads
as shown in Figure 3. Rotate the spring case so it
is correct for the application. Skip to step 14. For
Diaphragm Area Maintenance, continue with step 3.
3. Remove the diaphragm assembly by tilting it so that
the pusher post (key 19) slips off the lever (key 15).
4. If it is necessary to replace the lever assembly,
remove the lever cap screws (key 18).
5. Install the replacement lever (key 15) into the
lever retainer (key 16) by inserting the lever pin
(key 17). Secure the lever into the diaphragm
casing with the cap screws (key 18) and torque
the cap screws to 7 foot-pounds / 9.5 N•m. If
it is necessary to perform maintenance on the
diaphragm assembly, continue with steps 6
through 15.
6. Unscrew the diaphragm connector (key 54) and
remove the lower spring seat (key 31). Separate
the diaphragm (key 23) from the diaphragm
head (key 24), gasket (key 55) and the pusher
post (key 19).
7. Install the diaphragm (key 23), in reverse order
in step 6, apply lubricant to the threads of the
diaphragm connector (key 54) and finger tighten.
8. Hook the pusher post on the lever (key 15), then
turn the diaphragm (key 23) to match the holes in
the diaphragm with the holes in the spring casing.
9. Unhook the pusher post from the lever, hold the
pusher post and torque the diaphragm connector
(key 54) to 7 foot-pounds / 9.5 N•m.
10. Apply lubricant to the pusher post (key 19), then
hook the pusher post on the lever (key 15) and
check the hole alignment. If necessary, loosen the
diaphragm connector (key 54) and reposition the
diaphragm (key 23) on the pusher post (key 19).
Tighten the diaphragm using 7 foot-pounds /
9.5 N•m of torque.
11. To change the tension spring, remove the
spring seat bolt (key 61) from the tension
spring (key 32) and unscrew the spring
retainer (key 53).
12. Install the tension spring (key 32) on the lower
spring seat (key 31), insert and tighten the
spring retainer (key 53). Install the tension
spring on the spring seat bolt (key 61) until the
spring is flush with the top of the bolt threads as
shown in Figure 3.
13. Install the spring case (key 29) over the spring
seat bolt and so that the pilot assembly will be
in the correct position for the application. Place
the nameplate (key 39) over the screw holes,
insert the spring case cap screws (key 37), and
finger tighten.
14. Install the locknut (key 34), and hold the spring
seat bolt (key 61) to prevent turning, by running
the locknut all the way down the threads and
tighten as shown in Figure 3. Install the closing
cap gasket (key 63). Apply lubricant to the
threads on top of the spring case (key 29) and
install the closing cap (key 36).
15.
Using a crisscross pattern, finish tightening the
spring case cap screws (key 37, see Figure 3).
Pilot
These procedures are for gaining access to the
Type 6351F pilot trim and diaphragm parts. All
pressure must be released from the regulator and
pilot before the following steps can be performed.
Refer to Figure 4 for key number locations.
Trim Parts
1. Remove the body plug (key 3) and the valve
spring (key 6), and inner valve assembly (key 4)
from the body.
2. Inspect the removed parts and body plug gasket
(key 23), replace as necessary, and make sure the
plug seating surfaces are free from debris.
3. Sparingly apply lubricant to the body plug gasket
(key 23) and the threads of the body plug (key 3).
Install the body plug gasket over the body plug.
4. Install the plug spring (key 6), and inner valve
assembly (key 4) into the body (key 1). Torque the
body plug (key 3) to 6 foot-pounds / 8.1 N•m.