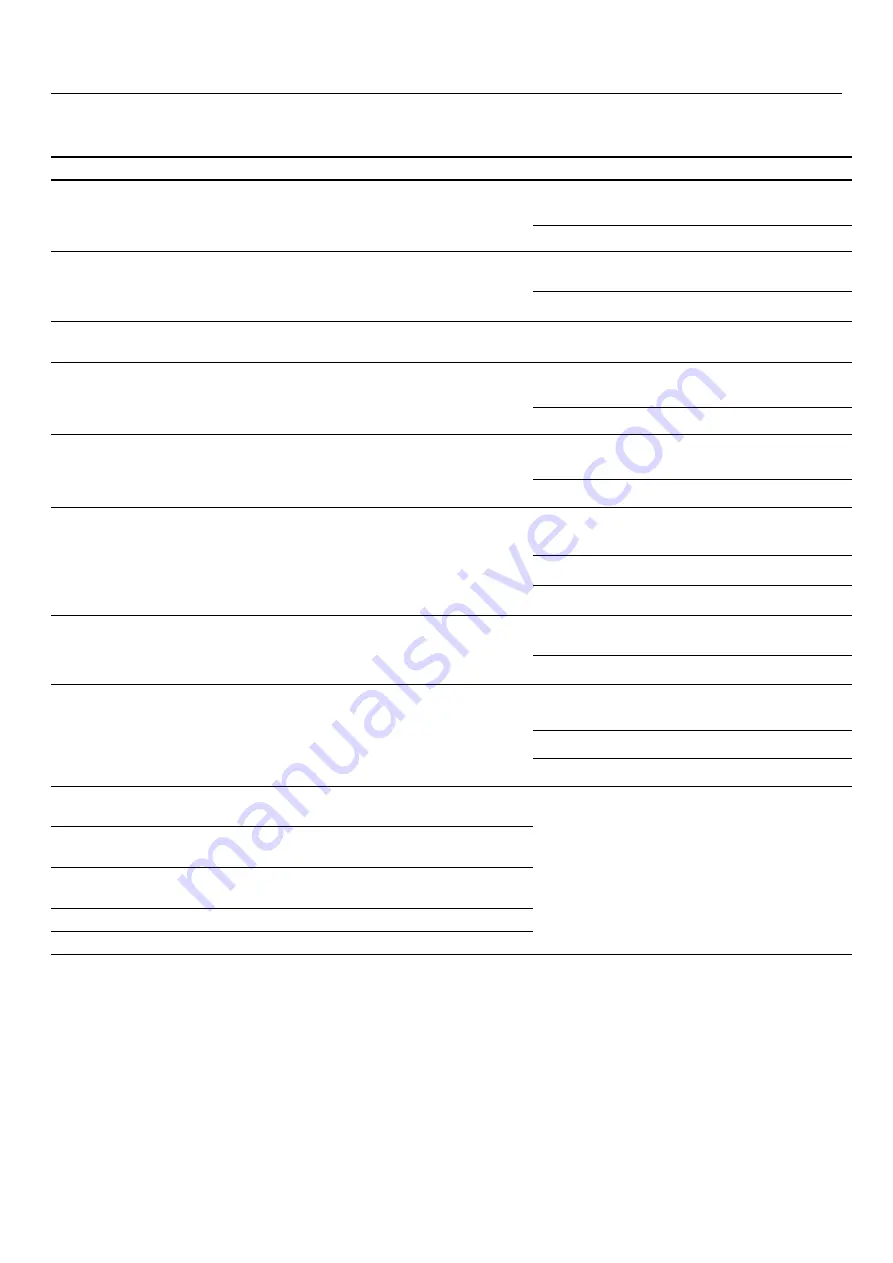
26
7 FAULT DIAGNOSTICS
FAULT CODE
POSSIBLE CAUSE
WHAT TO CHECK
FC0 - Motor Alarm
(shown in display to
customer)
abort of wash cycle
1.Check the wiring harness connections
between motor and controller.
2.Replace the main board.
EE0 deverter motor failed to start
1.Check the wiring harness connections
between the motor and controller.
2.Replace the deverter motor
Shown in Service Mode Menu
E:
EC1
motor driver device error
1.Check the wiring harness connections
between the motor and controller.
2.Replace the main board.
EC2
PWM signals inconsistency of BLAC
motor
1.Check the wiring harness connections
between the motor and controller.
2.Replace the main board.
EC3
motor winding test failed
1.Check the wiring harness connections
between the motor and controller.
2.Replace the main board.
3.Replace the wash pump.
EC4
BLAC motor too hot
1. Visual check of the wash pump, is it
blocked?
2.Replace the wash pump.
EC5
lost control of motor
1.Check the wiring harness connections
between the motor and controller.
2.Replace the main board.
3.Replace the wash pump.
EC6
Resistance measurement of BLAC
motor failed
1. Replace the main board.
EC7
DC voltage too low for resistance
measurement
EC8
Invalid current during resistance
measurement
EC9
Motor current plausibility check failed
ECA
Motor current offset out of range
FC6 model Only