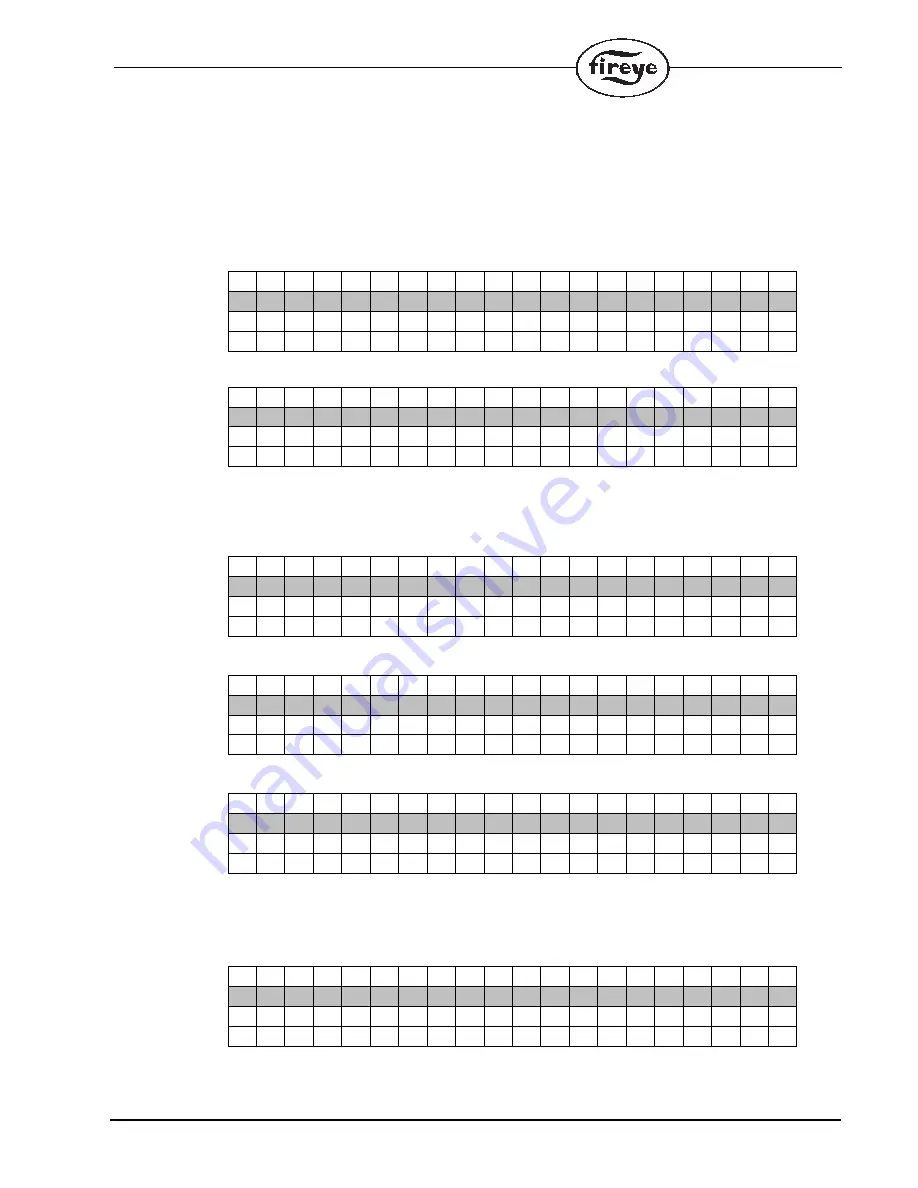
51
If a control was previously commissioned then the currently stored profile will be loaded and be
used as the base setpoints. Note: this can only occur when a profile is actually selected. If not com-
missioned (out of the box condition) then the succeeding Pxx point should be the same as the preced-
ing Pxx point. For example, when moving from P02 to P03, P03 assumes the same values as P02.
The NEXT key is used to move to the next setpoint, P01, P02, etc.
For illustrative purposes the shaded line represents the > < characters on the keypad and the AIR
servo shown below is selected for modifications.
To move a servo press the MDFY key and use the UP and DOWN keys to select the target position.
When done, the user presses the SAVE key to direct the system to move the servo to the target posi-
tion. After the SAVE key is pressed the value on the line showing the servo being modified will
change back to the current position. This value will be changing as the servo moves to the new target
position.
Repeat as necessary for the GAS and OIL servo. The NEXT key is used to move to the next profile
setpoint, P01, P02, etc.
Moving from P00 to P01 depends on the following. Since there might not be a profile selected the
display should indicate as follows:
P00 is considered the CLOSED position to which the servos will move to when the burner is off,
STANDBY or in lockout. While commissioning P00, regardless of the position of the burner on
C
O
M
M
I
S
S
I
O
N
I
N
G
p
0
0
>
A
I
R
(
1
)
3
.
1
°
<
G
A
S
(
3
)
1
.
9
°
O
I
L
(
2
)
2
.
6
°
C
O
M
M
I
S
S
I
O
N
I
N
G
p
0
0
>
A
I
R
(
1
)
8
.
4
°
<
G
A
S
(
3
)
1
.
9
°
O
I
L
(
2
)
2
.
6
°
C
O
M
M
I
S
S
I
O
N
I
N
G
p
0
0
>
A
I
R
(
1
)
3
.
1
°
<
G
A
S
(
3
)
1
.
9
°
O
I
L
(
2
)
2
.
6
°
C
O
M
M
I
S
S
I
O
N
I
N
G
p
0
0
>
A
I
R
(
1
)
5
.
2
°
<
G
A
S
(
3
)
1
.
9
°
O
I
L
(
2
)
2
.
6
°
C
O
M
M
I
S
S
I
O
N
I
N
G
p
0
0
>
A
I
R
(
1
)
8
.
4
°
<
G
A
S
(
3
)
1
.
9
°
O
I
L
(
2
)
2
.
6
°
C
O
M
M
I
S
S
I
O
N
I
N
G
p
0
0
>
N
O
P
R
O
F
I
L
E
S
E
L
E
C
T
E
D
<