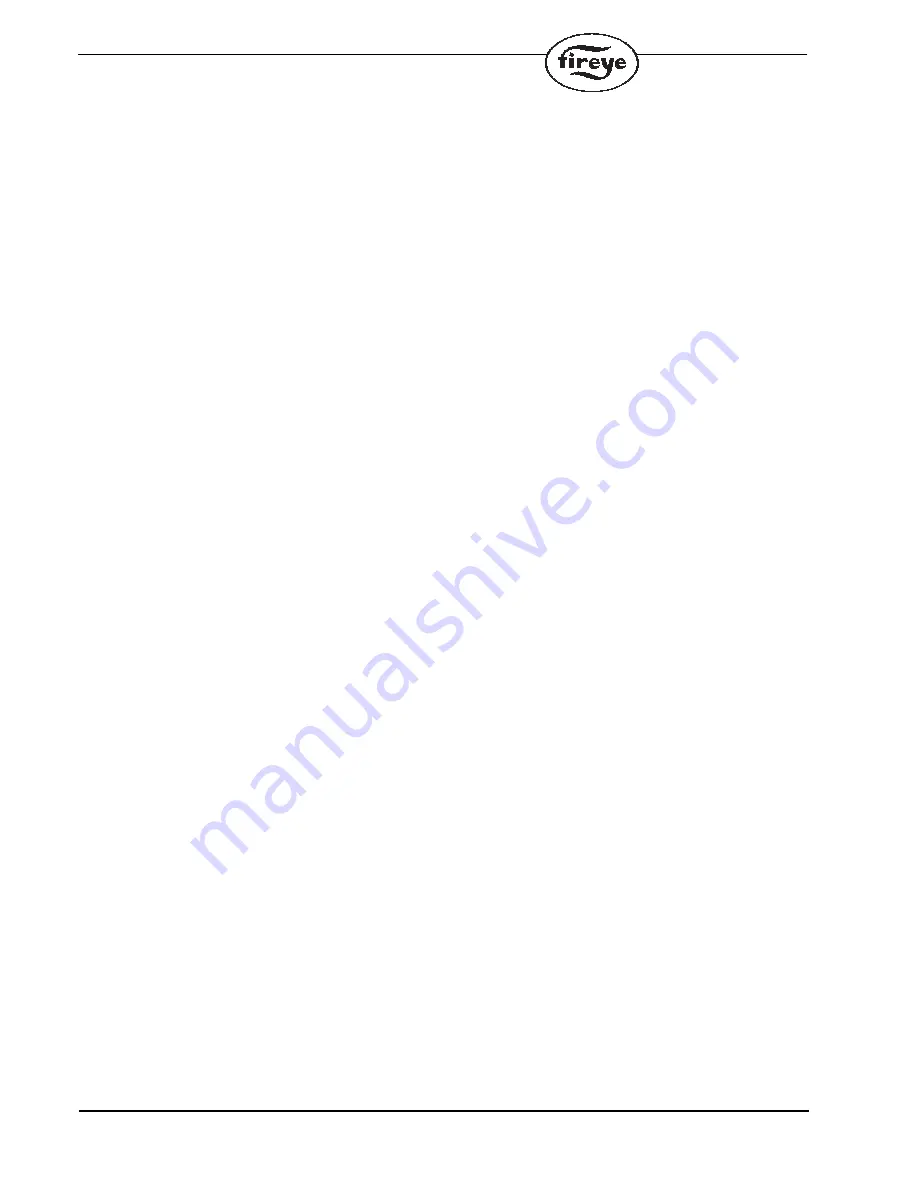
40
4.
Making modifications to any of the VFD parameters in the servo setup submenu, requires the Com-
missioning pass code to be enabled.
5.
Attempting to change a VFD channel to a value other than UNUSED in the ANALOG OUT sub
menu while its ASSIGNMENT > 0 in the SERVO SETUP sub menu is not allowed.
6.
Removal of a VFD from the commissioning table (set ASSIGNMENT to 0), will require a re-com-
missioning without the VFD. That is, lockout will occur if the profile (with the missing VFD) is used
during the next burner cycle.
7.
VFD's normally require motor start signals. This is usually derived from a relay energized by termi-
nal M (combustion blower output) of the flame safeguard. The normally open contacts are connected
to the start input terminals located the VFD.
8.
Using ACCEL/DECEL prevents step changes in the 4-20 mA output signal to the VFD and should
be set appropriately. However, adequate values for ACCEL and DECEL should also be set in the
VFD to prevent over current conditions.
9.
In VFD setup, DISPLAY FORMAT can be set to either CNT or %FS indicating the 4-20 mA feed-
back from the VFD is being used or can be set to ENCOD which requires an encoder connected to
the combustion motor shaft and the maximum encoder counts per second value entered for
ENCODER COUNTS. All of these options are scaled and normalized to a range of 0 - 1000. There-
fore it is possible after commissioning and operating with one method (CNTS), the user can change
the VFD setup to an alternate method (ENCOD). The system will treat this change transparently and
attempt to control with this new setting. As long as the ENCODER COUNTS value entered is cor-
rect or the 4-20 mA is representing full range frequency, the change should be transparent. However,
it is strongly recommended DISPLAY FORMAT be changed only if a complete commissioning or
adjust ratio procedure is executed immediately after the change and for all profiles using the VFD.
Performance notes:
1.
When controlling a VFD, setting GAIN and INTEGRAL to incorrect values can cause unstable oper-
ation of the VFD and subsequently large variations in the combustion blower motor rotation. When
setting GAIN and INTEGRAL, the following is suggested:
a. Make certain that the VFD drive is not using its own PID.
b. Set the PPC4000's VFD RUN MODE to AUTO, and begin with the INTEGRAL set 0.0 and
the GAIN is set to 1%.
c. The GAIN and INTEGRAL settings can only be verified by observing the system's reaction
to a step input. The best way to get a step response is by entering the Commissioning Mode
and cycling between p00 and p01 settings. At p00, the VFD is set to 0Hz. Proceed to p01 by
pressing the NEXT key, after entering the Commissioning Mode, and setting the VFD target
speed to at least 50% if DISPLAY FORMAT is set to %FS or a count of 500 if it is set to
CNTS. Note that the BURNER ON/OFF must also be set to ON and there must be a call for
heat to go to p01. To go back to 0Hz, press the BURNER ON/OFF button so that it is OFF.
Alternately pressing the BURNER ON/OFF will cycle to unit between p00 and p01 posi-
tions.
d. Increase the GAIN until the VFD begins to oscillate after it steps to p01. Once oscillation is
achieved, reduce the GAIN setting by 50%. For example, if a setting of 20 causes oscillation
after the step, reduce the GAIN to 10 then proceed to step (e). Note that with the INTEGRAL
set to 0.0, the VFD may not be able to reach the target speed.
e. Increase the INTEGRAL setting until the VFD is able to reach the target speed with no oscil-
lations.
f. The GAIN and INTEGRAL may have to be adjusted several times to achieve the right balance
of reaction time and oscillation but following the above method will get the settings close.
A steady reading is defined as only the tenths digit changing or the combustion blower motor is
not hunting.