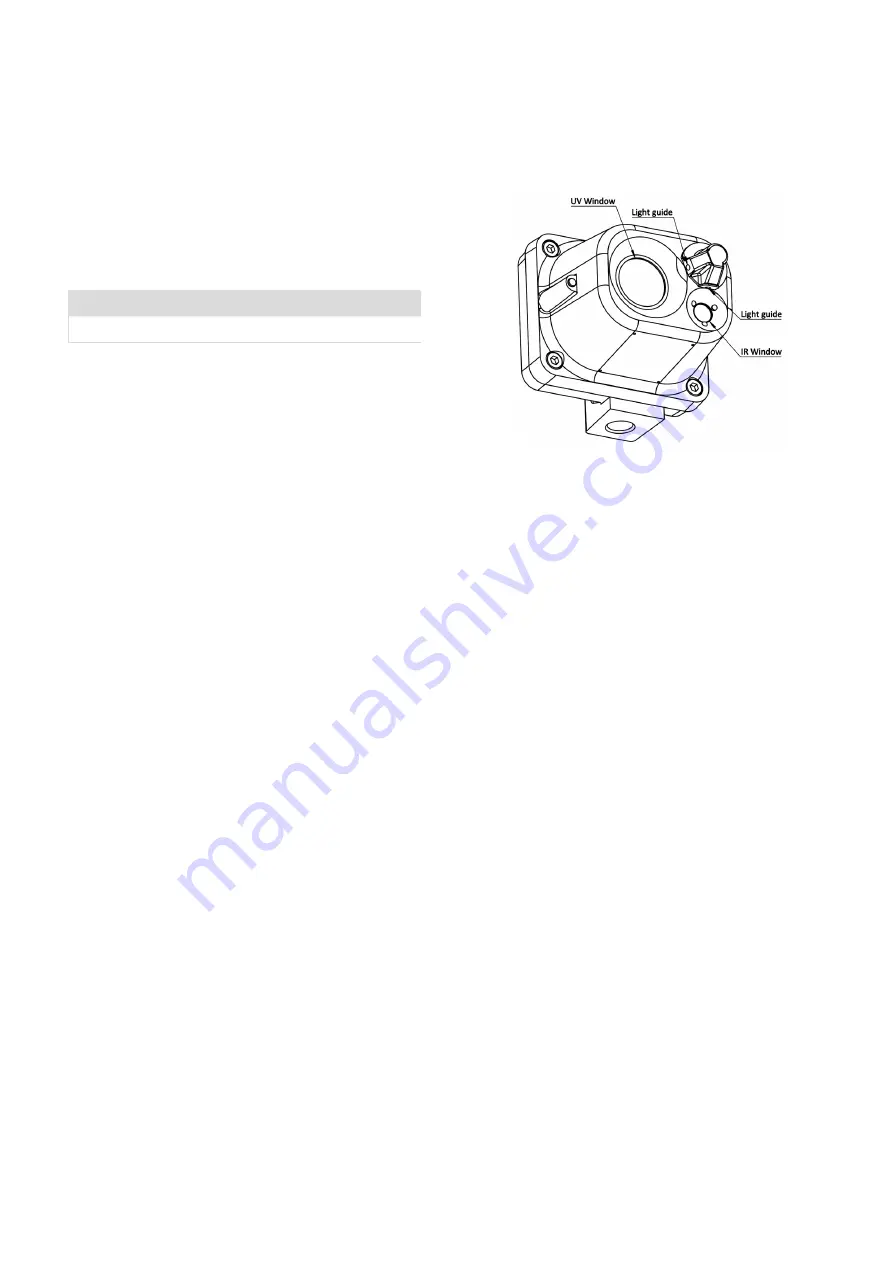
10
©Firefly AB (Oktober 2016)
This option provides the user with a method of programming the
unit number into the non- volatile memory of the microprocessor .To
program the detector address number, first remove power from the
detector . Then toggle the program option “ON” and set the first five
switches on the user selectable interface (USI) to the detector address
number .
In program mode, the USI becomes a binary programmer as illustrated
in Table 6 . When a switch is toggled “ON”, it will equal the binary
weighted number . These binary weighted numbers are added
together when a multiple number of switches are switched “ON” (i .e .,
if SW2 and SW3 were closed, then the detector number would equal
a 6) .
Table 6 Binary Weight for Switch States “ON”
SW1
SW2
SW3
SW4
SW5
1
2
4
8
16
When power is applied to the detector . The detector will sense that
it is in program mode and read the first five switch positions . From
the switch setting, it will determine the detector number . Once the
number has been determined, the detector will enter it into the non-
volatile memory of the microprocessor . Next, the amber LED will flash
“ON” a certain number of times . The number of flashes will be equal
to the detector’s address number . Then it will hold the fault relay and
amber LED “ON” constantly for about 10 seconds . Then the detector
will repeat flashing the detector address number and the delay time . It
will continue this mode for up to 5 minutes .
Once you are sure that the proper number is programmed, then shut
the power “OFF” and set the USI options to suit your application .
Reference the section on the USI if you are not sure which option is
best for your application or call a Firefly AB application engineer .
Note:
In the case that the program option switch is left “ON” and the
detector is installed on the network . The detector will go through the
same process as explained previously, but after 5 minutes the detector
will resume the last USI setting that it had prior to going into the
program mode .
Maintenance and troubleshooting
Model 660 and 860 flame detectors are designed for years of
trouble-free operation with minimal attention . Periodic cleaning of
the optical surfaces is essential, however, for maintaining reliable fire
protection . The frequency of required cleaning will be determined
by the environmental conditions in and around the installation . The
detectors should be regularly inspected for a build-up of dust or other
contaminants on the optical surfaces .
The detection specifications presented in this manual are predicated
on performance with clean sensor windows . Contaminants such as
dust, oil and paint will reduce sensitivity . Severe contamination on the
light guides or sensor windows will cause a failure of the auto-test .
A detector that fails auto-test due to dirty optical surfaces may be
capable of detecting fire, but its effectiveness will be limited from 50 to
70% obscuration .
Cleaning Procedure:
Locate the following optical surfaces: (Figure 11)
Models 660-XX1XX
1 . UV Sensor Window
2 . UV Light Guide End
Model 860-XX1XX
1 . UV Sensor Window
2 . UV Light Guide End
3 . IR Sensor Window
4 . IR Light Guide End
Note:
Models 660-XX0XX and 860-XX0XX are not equipped with light
guides . Clean the optical surfaces with a cotton swab wetted with
commercial liquid glass cleaner, ammonia, methanol, or isopropyl
alcohol . Rinse with clean water and dry with lens quality cloth . Repeat
with methanol if needed to remove smudges .
Caution:
Wiping with excessive force or inappropriate materials may
scratch the optical surfaces and impair performance .
Figure 11 – Optical surfaces
Troubleshooting:
*WARNING*
Do not attempt to repair a detector . Study these
troubleshooting guidelines and review the referenced sections of the
manual prior to performing maintenance on the fire detection system .
New Installations:
Starting with Revision E Software, when the detectors are in
operational mode, and amber LED will be visible for one second
approximately every ten seconds . If any or all the detectors fail to
operate, check the system wiring and power supply . Tight, reliable
wiring connections are essential, as are low-resistance connections
from every detector housing to earth ground . Measure the voltage
between terminals 8 and 10 at the detector locations to verify that the
supply voltage is within range .
Note:
Voltage at detectors installed farthest from power source will be
lower than the no-load supply voltage due to line losses . Maximum
load condition occurs during manual test .
The Model 660 and 860 flame detectors employ sensitive and
sophisticated electronic circuitry in the fire detection process . Power
line transients or excessive power supply ripple may therefore cause
erratic or intermittent operation . DC-powered detectors function best
with ripple-free (less than 1 percent) supply voltage; power supply
filtering may be necessary to improve performance .
Note:
For reliable operation, the instantaneous supply voltage at the
input to any detector must not fall below 20 Vdc or exceed 32 Vdc .
Failure To Alarm:
Upon detection of fire, the fire outputs will activate and the red LED,
visible through the UV sensor window, will turn “ON” .
If during testing, a detector fails to alarm, inspect the sensor windows
for cleanliness . Clean sensor windows are essential for effective
optical fire detection . Clean all the optical surfaces per the cleaning
procedures previously described and retest the detector .
Should the detector continue to be inoperative, check the supply
voltage and all associated wiring . Incorrect power supply voltage or
loose connections will cause marginal or intermittent performance .
DMLieferant
Тел
.: +7 (499) 990-05-50; +7 (800) 775-29-59 dmliefer.ru