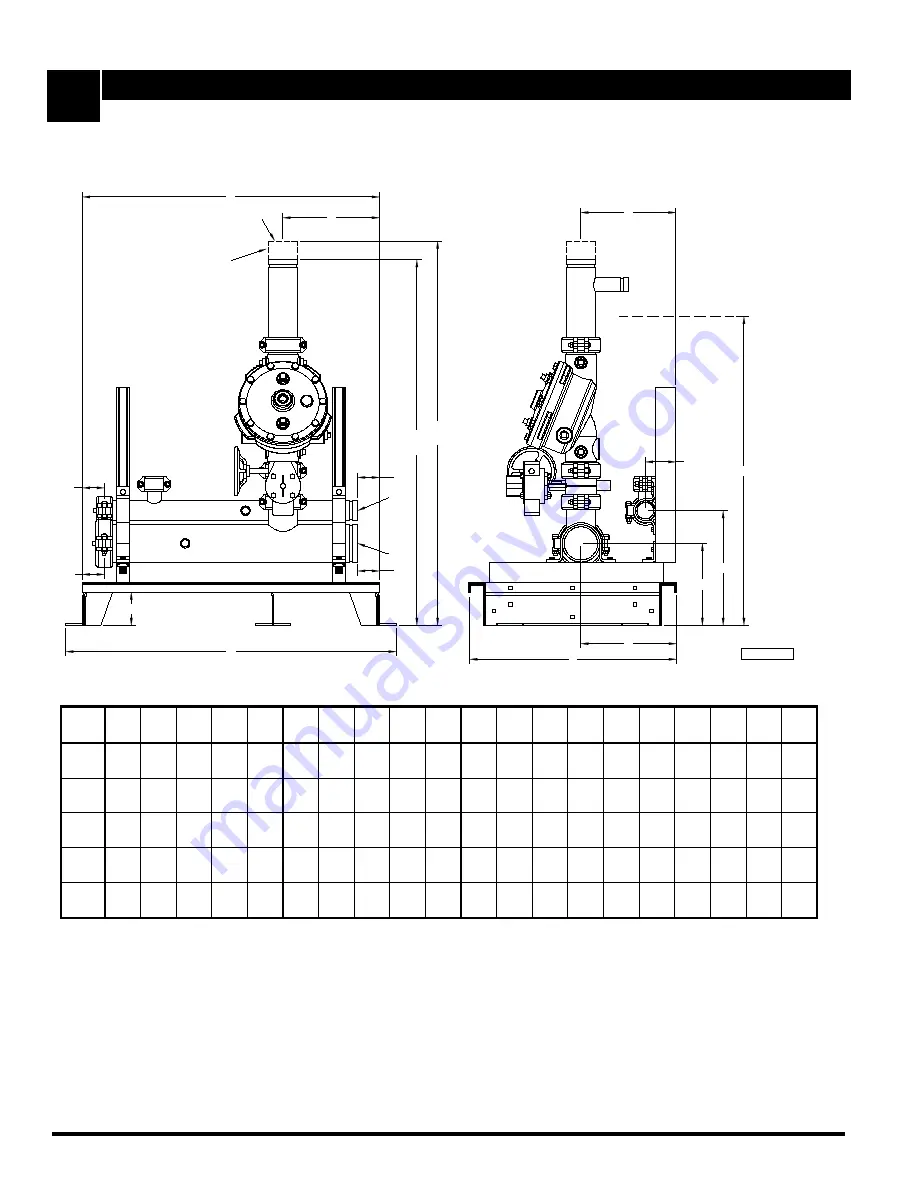
Page 6 of 8
T
OTAL
P
AC
®
3
G
Integrated Fire Protection System
Dimensional Data & Cabinet - Deluge System
FM-076A-0-108A
Figure 7 - Skid and inlets/outlets dimensions
(figure is shown without trim for clarity)
Optional Fire Dep't Connection
Outlet (not shown)
T
Q
A = Main Inlet Manifold Diameter
B = Sprinkler Riser Diameter
C = Drain Manifold Diameter
N
E
F
M
P
G
L
ØA
Optional Shut-off Valve
H
D
L
R
(U)
S
(V)
FM-061H-0-133A
K
ØB
ØC
J
M
Table 7 - Cabinet dimensions
- dimensions are in inches (mm)
Unit
size
A
B
C
D
E
F
G
H
J
K
L
M
N
P
Q
R
S
T
U
V
1½"
(40)
2"
(51)
1½"
(38)
2"
(51)
23"
(584)
25"
(635)
4"
(102)
8¾"
(222)
11½"
(292)
13¾"
(349)
3¾"
(95)
2¾"
(70)
2¾"
(70)
8"
(203)
11½"
(292)
27"
(686)
43"
(1092)
47"
(1194)
34¼"
(870)
48½"
(1232)
52½"
(1334)
2"
(50)
2"
(51)
2"
(51)
2"
(51)
23"
(584)
25"
(635)
4"
(102)
8¾"
(222)
11½"
(292)
13¾"
(349)
3¾"
(95)
2¾"
(70)
2¾"
(70)
8"
(203)
11½"
(292)
27"
(659)
45¼"
(1149)
49¼"
(1251)
34¾"
(883)
51¾"
(1314)
55¾"
(1232)
3"
(80)
4"
(102)
3"
(76)
2"
(51)
35¾"
(908)
25"
(635)
4"
(102)
10"
(254)
11½"
(292)
13¾"
(349)
3¾"
(95)
2½
(64)
2½
(64)
11½"
(292)
11½"
(292)
39¾
(1010)
44"
(1118)
47¾"
(1213)
37"
(940)
51"
(1295)
54¾"
(1391)
4"
(100)
4"
(102)
4"
(102)
2"
(51)
35¾"
(908)
25"
(635)
4"
(102)
10"
(254)
11½"
(292)
13¾"
(349)
3¾"
(95)
2½
(64)
2½
(64)
12"
(305)
11½"
(292)
39¾
(1010)
48½"
(1232)
53¼"
(1353)
42"
(1499)
56½"
(1435)
61¼"
(1556)
6"
(150)
6"
(152)
6"
(152)
2"
(51)
46"
(1168)
25"
(635)
4"
(102)
11"
(279)
11½"
(292)
13¾"
(349)
3¾"
(95)
5¼
(133)
5¼
(133)
17¾"
(451)
11½"
(292)
50"
(1270)
59½"
(1511)
65¼"
(1657)
51½"
(1308)
70½"
(1791)
76¼"
(1937)
Notes:
1. Dimensions are nominal and may vary ±¼" (±5mm).
2. Dimensions T, U & V are for optional fire department connection.