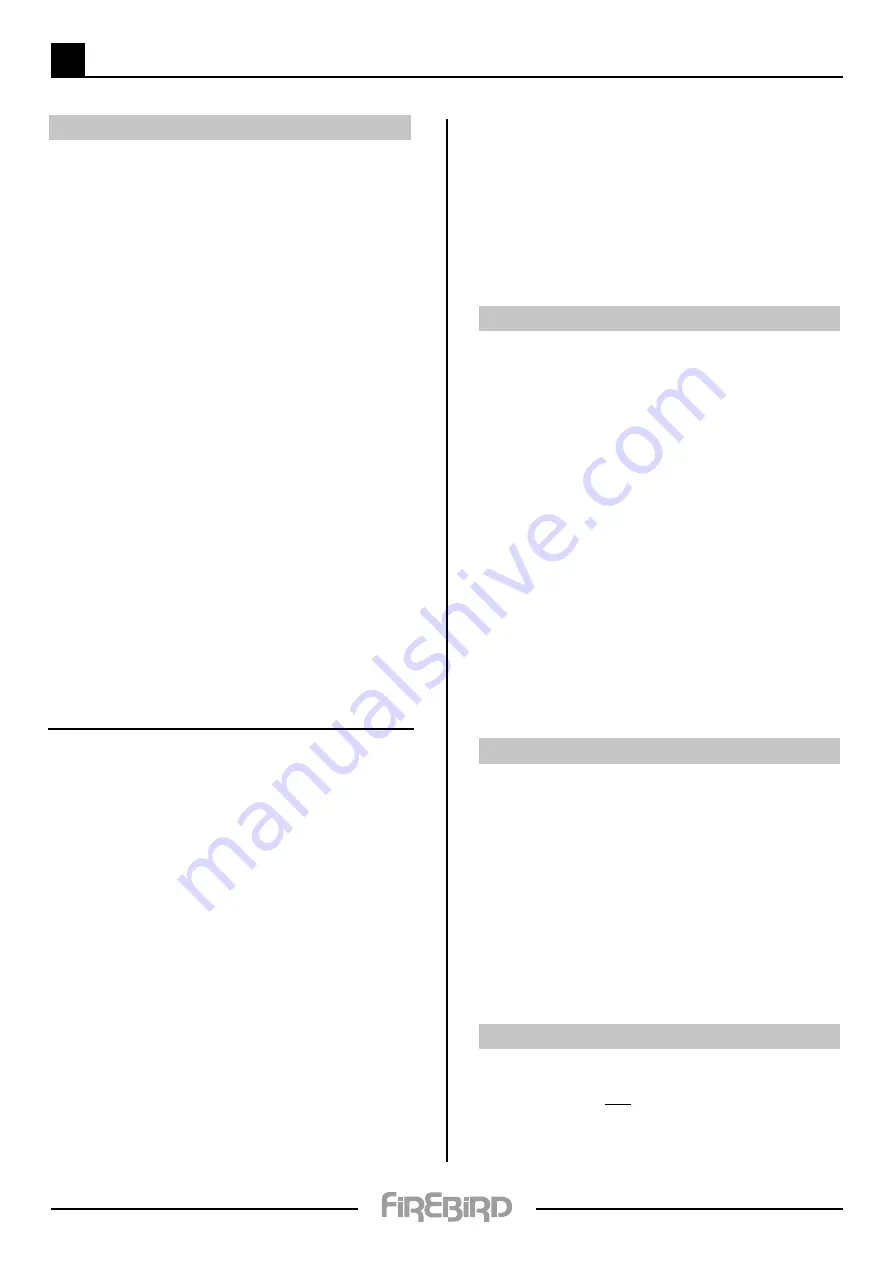
1
2
safety
HealtH & safety InformatIon
tHIs ProduCt Has Been desIgned to tHe folloWIng
standards:
this equipment complies with the low voltage directive
2014/35/eu and directive 2014/30/eu.
emC - conformity was demonstrated by meeting the
following standards:
BS eN 55014-2: 2015: electromagnetic Compatibility -
Requirements for Household appliances, electric Tools and
Similar apparatus - Part 1: emission
BS eN 55014-1: 2017: electromagnetic Compatibility -
Requirements for Household appliances, electric Tools
and Similar apparatus - Part 2: Immunity - Product Family
Standard
BS eN 61000-3-2: 2014: electromagnetic Compatibility (eMC)
Part 3-2: Limits - Limits for Harmonic Current emissions
(equipment input current <16 a per phase)
BS eN 61000-3-3: 2013: electromagnetic Compatibility (eMC)
Part 3-3: Limits - Limitation of Voltage Changes, Voltage
Fluctuations and Flicker in Public Low-voltage Supply
Systems (equipment with rated current <16 a per phase and
not subject to conditional connection)
The installer should be aware of his/her responsibilities under
the current, local Health and Safety at Work act. The interests
of safety are best served if the boiler is installed and
commissioned by a competent, qualified engineer, preferably
OFTeC trained and registered. a Building Notice may be
required in england and Wales and other parts of the United
Kingdom.
Under the Consumer Protection act 1987 (UK), section 6 of
the Health and Safety act 1974 (UK) and the Safety, Health
and Welfare at Work act 2005 (ROI), we are required to
provide information on substances hazardous to health.
InsulatIon and seals
Ceramic Fibre, alumino - Silicone Fibre material are used for
boards, ropes and gaskets. Known hazards are that people
may suffer reddening and itching of the skin. Fibre entering
the eye will cause foreign body irritation. It may also cause
irritation to the respiratory tract.
Precautions should be taken by people with a history of skin
complaints or who may be particularly susceptible to
irritation. High dust levels are only likely to arise following
harsh abrasion. Suitable personal protective equipment
should be worn where appropriate.
generally, normal handling and use will not give discomfort.
Follow good hygiene practices, wash hands before
consuming food, drink or using the toilet.
First aid - medical attention should be sought following eye
contact or prolonged reddening of the skin.
The small quantities of adhesives and sealants used in the
product are cured. They present no known hazards when
used in the manner for which they are intended.
fuel sPIllage
1. Switch off all electrical and other ignition sources.
2. Remove all contaminated clothing to safeguard against
fire risk and skin damage. Wash affected skin thoroughly
with soap and water and remove clothing to a safe well
ventilated area and allow to air before cleaning.
3. Contain and smother the spill using sand or other suitable
oil absorbent media or non-combustible material.
4. Do not allow fuel to escape into drains or water courses.
If this happens, contact the relevant authorities in your
area.
5. Consult local authority about disposal of contaminated
soil.
safety
Safe use of Kerosene. These fuels give off a flammable
vapour when heated moderately. Vapour ignites easily, burns
intensely and may cause explosion. The vapour can follow
along at ground level for considerable distances from open
containers and spillages collecting as an explosive mixture in
drains, cellars, etc.
Fuels remove natural oils and fats from the skin and this
may cause irritation and cracking of skin. Barrier cream con-
taining lanolin is highly recommended together with good
personal hygiene and where necessary appropriate personal
protection equipment (P.P.e.).
gas oil may also cause irreversible damage to health on
prolonged or repeated skin contact.
always store fuels in a properly constructed and labelled
tank. always handle fuel in open air or well ventilated space
away from sources of ignition and refrain from smoking.
always drain fuel using a proper fuel retriever, funnel or
mechanical siphon. Never apply heat to a fuel tank, container
or pipework. Never siphon fuel through tube by mouth.
avoid inhaling fuel vapour as this can cause light headedness
and seriously impair judgement.
fIrst aId
If fuel is accidentally swallowed:
* Seek medical attention immediately.
Do NOT induce vomiting.
If fuel is splashed into eyes:
* Wash out with running water for at least ten
minutes and seek medical attention.
safety - conformity was demonstrated by meeting the
following standards:
BS eN 60335-1: 2012 + a13: 2017: Household and Similar
electrical appliances - Safety - Part 1: general Requirements
BS eN 60335-2-102: 2006 + a2: 2016: Household and
Similar electrical appliances - Safety - Part 2-102: Particular
Requirements for gas, Oil and Solid-fuel Burning appliances
having electrical Connections