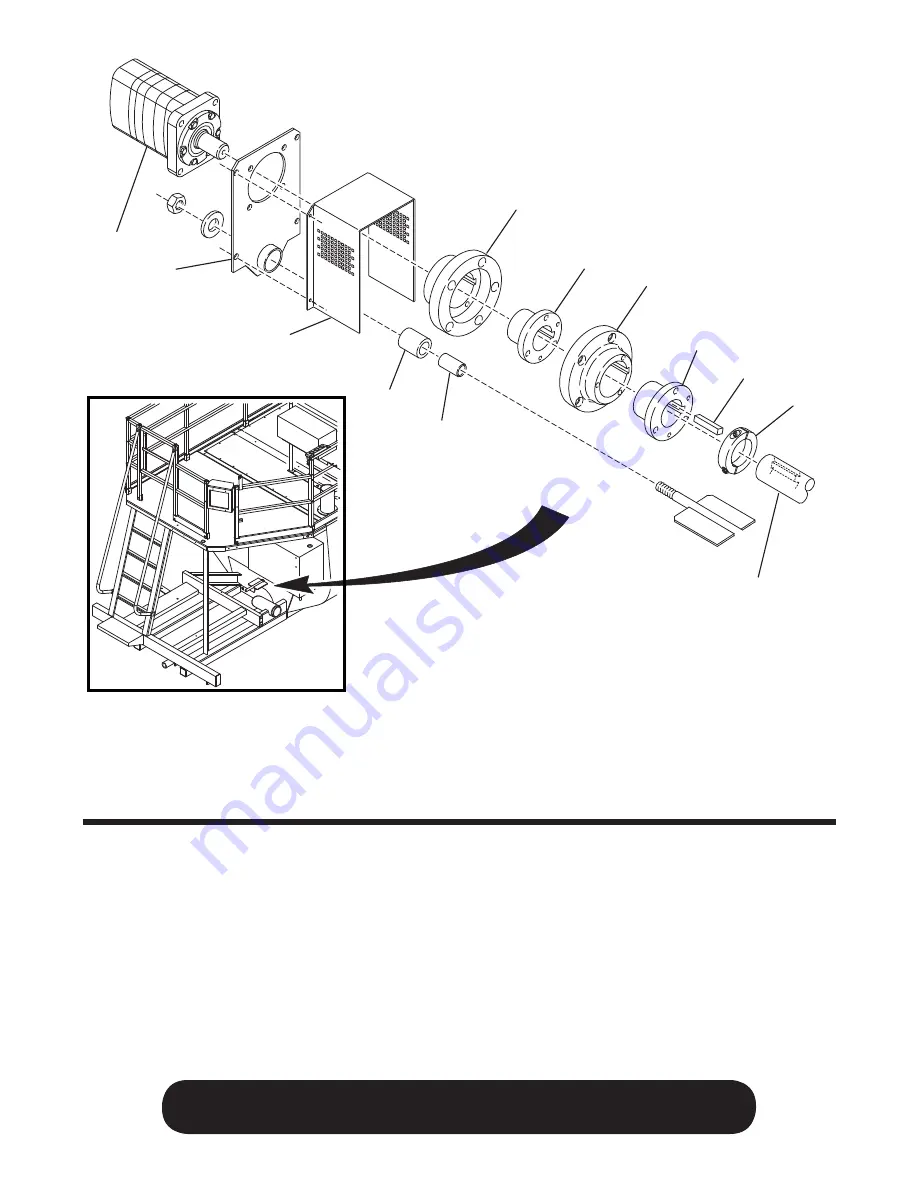
T170 MB0521 Rev. B
WHEN ORDERING PARTS, BE SURE TO STATE
SERIAL NUMBER OF MACHINE
87
HYDRAULIC AGITATOR DRIVE
Ref.
No. Part
Number
Description
No.
Req’d
1
012333
Hydraulic
Motor
1
2
012354
Hydraulic
Motor
Mount
1
3
F330-0029
Agitator
Coupling
Guard
1
4
012522-02
Rubber
Bushing
1
5
012522-04
Torque
Arm
Insert
1
6
011780
Rigid
Coupling
1
7
003055B
Motor
Bushing
1
8
055103
Agitator
Bushing
1
9
190127-40
1/2 in. Square Key x 2-1/2 in. Long
1
10
012625
2 in. Split Collar
2
REFERENCE the
AGITATOR and
BEARING
ASSEMBLIES
4
5
6
2
1
7
8
9
3
6
10
Summary of Contents for HydroSeeder T170 MB
Page 4: ......
Page 30: ...24 DISPLAY LIST SINGLE DATA FORMAT DUAL DATA FORMAT...
Page 50: ...44 12 6 1 5 3 4 3 7 11 8 2 9 10 Figure 9 Lubrication and Adjustment Points...
Page 57: ...51 THIS PAGE LEFT BLANK INTENTIONALLY...
Page 58: ...52 8 ft 10 in 269 cm 16 ft 8 in 508 cm 7 ft 9 in 236 cm...