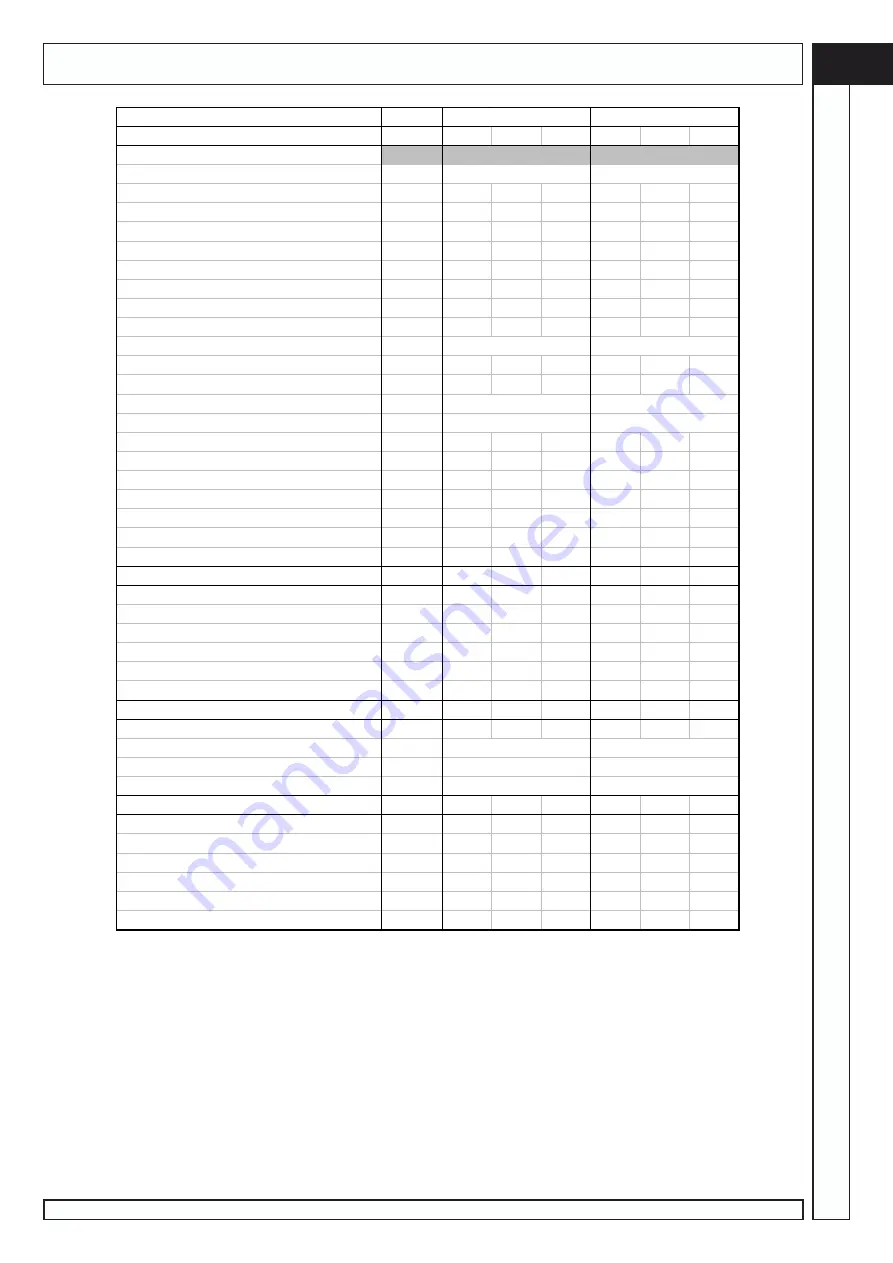
Rotar Plus 20-25 Easytronic - Cod.197AA2702 - Edition 00 01/2004
5
GB
SPECIFICATIONS
7HFKQLFDOIHDWXUHV
Pressure
EDU
Compressor type
FS 50 TM
FS 50 TM
Compressor rotation speed
RPM
4830
4330
3460
5640
5200
4120
Air volume supplied
l/min
2350
2050
1750
2700
2450
2050
Oil quantity
l
7
7
7
7
7
7
Oil quantity for topping-up
l
0,5
0,5
0,5
0,5
0,5
0,5
Max. final over temperature
°C
5
5
6
10
8
7
Removed heat
kJ / h
51300
51300
51300
63270
63270
63270
Fan flow rate
m³ / h
3100
3100
3100
2931
2931
2931
Oil residues in the air
mg / m³
4
4
4
4
4
4
Electric motor (bipolar)
160 L/2 B3 B5
Motor power
kW
15
15
15
18,5
18,5
18,5
Max. power absorbed
kW
18,4
18,4
18,4
21,5
21,5
21,5
Voltage
V/Hz
Auxiliary voltage
V/Hz
230-24 / 50-60
230-24/50-60
Electrical box protection class
IP
54
54
54
54
54
54
Motor insulation class
F
F
F
F
F
F
Full load current
A
31
31
31
36
36
36
Starting load
A
70
75
73
98
104
107
Max. Start-up per hour
n°
10
10
10
10
10
10
Ambient limit temperature
°C
50
50
50
50
50
50
Noise level at 1 m (Cagi pneurop)
dB (A)
70
70
70
71
71
70
3URWHFWLRQGHYLFHV
Max compressor temperature
°C
110
110
110
110
110
110
Min. oil temperature
°C
-7
-7
-7
-7
-7
-7
Thermal motor cut-out
A
19,8
19,8
19,8
23
23
23
Safety valve setting
bar
14
14
14
14
14
14
Start-up pressure switch setting
bar
1,5
1,5
1,5
1,5
1,5
1,5
'LPHQVLRQVDQGZHLJKW
Dimensions mm
Weight
Kg
Air cock fitting
Rp
3RZHUFRQQHFWLRQ
Power
kW
15
15
15
18,5
18,5
18,5
Cable section (max. lenght 3 mt.)
mm²
6
6
6
6
6
6
Absorbed current
A
31
31
31
36
36
36
Relay setting
A
19,8
19,8
19,8
23
23
23
Switch
A
50
50
50
63
63
63
+3
+3
132 MD/2 B3 B5
3/4"
3/4"
400 / 50
400/50
1030×680×1030
1030×680×1030
300
360